Moving onto simulation settings. I am starting to read up on the correct numerics for my situation. I have read through some of your old threads such as Initial Values for turbulence coefficients and continued with the paper from Spalart and Rumsey. I am trying to start at the beginning with understanding the Initial Conditions settings as the FSAE tutorial said to use do the following changes:
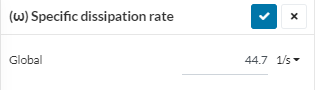
Based on my brief reading on these topics, this recommendation from the Spalart and Rumsey paper gave a good explanation.
B. Boundary-Layer Levels, and Device Reynolds Numbers
Another very concrete consideration in aerospace applications is the gap regions between different elements of a wing. These are normally designed to allow a “potential core” between the two boundary layers. It is all too easy to set the ambient νt so high that this potential core is smeared, and to be ignorant of this fact, deeply hidden in the flow field. Yet, this will make CFD inaccurate, and sensitive to ambient values.
- As i understand it, the initial condition values for (k) and (w) are for the ambient air in the bounding box. These values can be set so that the ambient air has laminar or turbulent characteristics, which through the paper, suggests that there is an effect on boundary layer transition, simulation convergence ability, and effects slot gap boundary layer measurement accuracy.
A. Free Decay
As mentioned earlier, for large decay rates, the coarseness of the grid far from the body may make the solver unable to support an accurate computation and the decay can be grossly underestimated.
- Would this be a factor when our level 0 mesh size is 1m?
Using significantly lower values for freestream ω, however, the decay rate is dramatically reduced, and CFD predicts the levels with greater precision on all three grids (lower curves).
- Does a low (w) value, even with a coarse mesh from #2 mean that precision is not a problem?
III. Ambient Values
We also consider the common situation in which the ambient values are picked to trigger turbulence in all boundary layers without local tripping, except perhaps at very low Reynolds numbers.
- Should I be purposely picking a turbulent ambient flow?
C. Recommended Values
the SST model can encounter a particular problem when the ambient value of νt/ν is large and ω is set too small. The main problem with this erratic behavior is that convergence can stall. Figure 3 suggests that values of ωc/U up to 100 would be more than safe, so that the useable range is not too narrow.
To summarize, the following ambient freestream turbulence values (in the region near the body) are recommended for general use for most typical external aerodynamic applications with two-equation turbulence models: k/U2 = 1 × 10−6 (or Tu near ≈ 0.1%), εc/U3 = 4.5 × 10−7, ωc/U = 5. These values yield an ambient eddy viscosity ratio of νt/ν ≈ 2×10−7 ×Rec. Thus, for example, for Rec = 10 million, νt/ν ≈ 2; and for Rec = 1 million, νt/ν ≈ 0.2. Again, these ambient levels are not achievable if the turbulence variables are allowed to decay naturally according to the turbulence equations. One easy way to achieve these ambient levels in practice is to impose them as both inflow and floor values.
- From what i have read, an FSAE car operates under low turbulence intensity of less then 1%. My (k) and (w) values are dependent on desired laminar or turbulent ambient air. turbulence model plays a factor on these values. Having multi-element wings play a part. Cell size before and i assume after the model have an effect on the consistency of results.
Am i going too deep into these values? Is this really that important for my results?