Hi everyone,
I want to get the velocity and temperature field of the flow around a motorcycle.
So I run an Incompressible simulation and then a Convective Heat Transfer Simulation, using the same geometry, mesh, initial and boundary conditions.
In the Convective Heat Transfer simulation I set all the heat fluxes equal to zero, in order to examine if I will get the same velocity field with the Incompressible simulation.
As you can see on the results below, this didn’t happen. Does anyone know why there is this difference?
Incompressible Simulation Result:
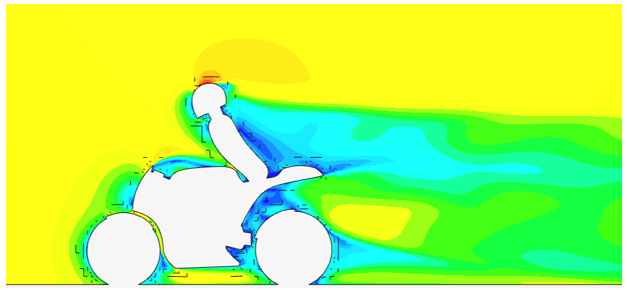
Convective Heat Transfer Simulation Result:
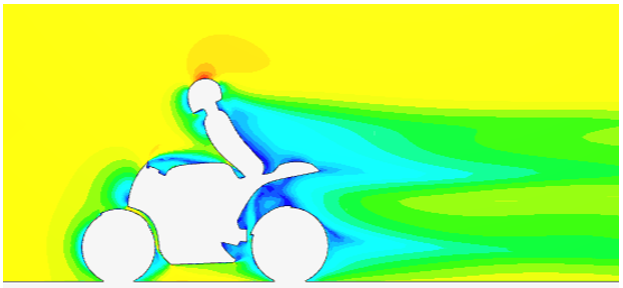
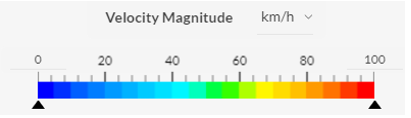
Hi, and welcome to SimScale!
Could you please post the project link so we can have a closer look? It’s the page URL, just over the Workbench environment.
In a general sense, there are a lot of factors that need to be checked to draw a conclusion. For instance, if the meshes were the same, if the simulations are fully converged (and to the same level of convergence).
Cheers
Thanks for the reply.
This is the link:
I compare the results from “07 Run BASE” Incompressible Simulation and “02 Run BASE” Convective Heat Transfer Simulation. The mesh that I used in both cases, was the “Base Mesh”.
The only parameter which I assume that could cause this difference is the initial condition of Turb. Thermal Diffusivity. I left the default value in this one, because I didn’t know who to calculate it.
In any case, please let me know if you have any other idea about the difference between the results.
Perfect, thanks!
There are some differences between the settings from the two solvers (simpleFoam vs boussinesqSimpleFoam). For instance, the absolute/relative tolerances of the solvers, amongst other numerics settings. Most notably, the divergence scheme for velocity (div phi,U) is first-order accurate for the convective heat transfer, versus 2nd order accurate for your incompressible simulations, which can definitely cause differences.
In any case, the simulations have been run for around 600 iterations. For a better comparison, it would be best to have closer settings and also longer runtimes, and ensuring a similar level of convergence.
Cheers
2 Likes
Ok, I can see the differences in numerics. Thank you very much!
Two last questions:
-
As for the level of convergence, it seems that in both cases the residuals reach asymptotically a steady value. Isn’t it a good indicator that the 600 iterations are enough? If not, how can I find the appropriate number of iterations?
-
Could you suggest a way to calculate a good initial value for Turb. Thermal Diffusivity?
Cheers!
Hi!
It’s not a good approach to trust only the residuals to assess convergence. I’ve seen cases with “very low” residuals (e.g. most parameters under 1e-6) which hadn’t converged, and also cases with “high” residuals which had converged.
Convergence should be a mix of:
- Residuals
- Parameters of interest (e.g. drag coefficient, forces at a particular face, pressure at the inlet, etc.). These parameters should be tracked with result controls
- Manual inspection of the results. “Does anything look non-physical? Are the values in the realms of what I expected?”
For your second question, alpha_t is given by (k*\rho)/(\omega*Pr_t), so you can either use the default setting (which shouldn’t be a big issue), or you can estimate your own value based on the initial conditions for k and omega, and the material properties.
Cheers
2 Likes
Thank you very much for your replies!