This article aims to explain and show how to switch between constant time step control and adjustable time step control in transient CFD simulations.
What is the Time Step in Transient Simulations?
In transient CFD simulations, we simulate the flow in real-time. This is solved by starting at
Where:
is the next time step is the current time step is the time increment
Constant Delta T
The first option is to set
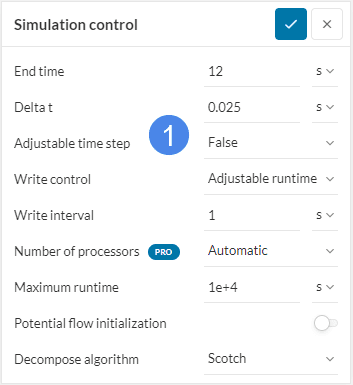
If the flow field is assumed to be mostly constant/stable in time and transient effects are restrained to the temperature field, a fixed time step for the complete simulation can be chosen. This gives users more direct control of the simulation.
Adjustable Time Step
In addition to the constant time increment
Where:
is the Courant number is the fluid velocity in a given cell is the time increment is the cell length
For multiphase simulations, the Courant number
The image below shows the simulation control panel when adjustable time step is true:
If the flow field in the simulation domain is expected to show relevant transient behavior, then an Adjustable time step and a maximal CFL number should be chosen. As such, the solver reacts to transient velocity peaks that might introduce instabilities or inaccuracies by reducing the time step. This way, when the velocity reduces, the time step is increased again ensuring a minimal simulation run time.
Starting Time Step for Adjustable Time Steps
In the SimScale Simulation Control Panel, the Adjustable time step is active per default. Note that the user can still choose the
A possible approach is to inspect the size of the mesh elements and estimate the velocity in the domain due to the boundary conditions. By using the equation 2 and assuming a value of Courant number equal to 1, we obtain the following:
Where:
is the first time step is the smallest cell size is the fluid velocity in a given cell
Note that using even smaller values for Delta t is possible for additional robustness. Since the Adjusted time step option is enabled, SimScale will automatically increase the time step size as the simulation progresses.
Ratio of Velocity to Mesh size
When adjustable time step is active, a high velocity
Note
If none of the above suggestions solved your problem, then please post the issue on our forum or contact us.