In the design phase of equipment, oftentimes the user wants to understand how their system behaves under different conditions. Using SimScale’s capabilities for parametric studies, you can automatically run multiple simulations for various conditions and efficiently optimize your designs.
Overview of Parametric Studies
In the design process, the user may be interested in how their system performs under different conditions. With parametric studies, the user can quickly set up, run, and compare results for several configurations in parallel saving heavily on computational time.
When parametric capabilities are available, the following icon is visible in the setup window:
In the example above, the user wants to define several mass flow rates of interest for one of their inlets. A table appears after clicking the parametric icon, where the user defines the flow rates to analyze in the simulation phase:
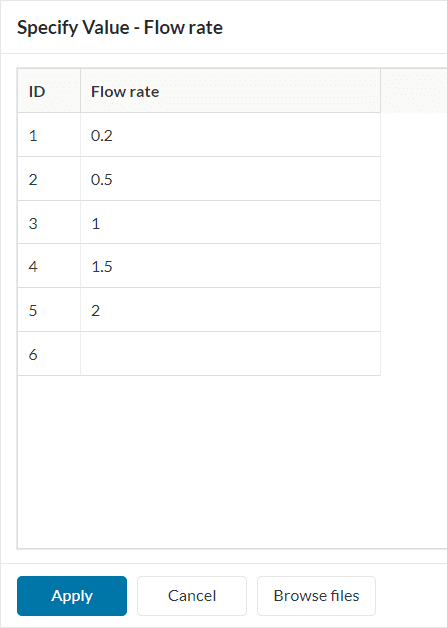
With the configuration above, when the user starts a simulation, SimScale sweeps through the table definition and launches an Experiment containing one simulation run for each configuration of interest.
Important
Currently Supported Parameters
Parametrization is available for the following settings:
- Velocity inlet: volumetric or mass flow rate
- Velocity inlet: fixed value for velocity
- Rotating zones: rotational velocity
- Inlet conditions (velocity, pressure, etc.): fixed temperature value
- Natural convection inlet-outlet: ambient temperature
- Velocity outlet: volumetric or mass flow rate
- Velocity outlet: fixed value for velocity
- Pressure inlet: fixed or total pressure
- Pressure outlet: gauge or mean pressure
- Power source: absolute or specific power source value
- Momentum sources: average velocity
- Centrifugal force: rotational velocity
Example
A cold plate is often used in electronics cooling applications, aiming to transfer heat from the sources to a cooling liquid. In this example, a cold plate design undergoes a test for different mass flow rates.
The objective is to see how the temperature of the transistors changes and decide on the most cost-efficient configuration. In the setup, the cooling fluid is defined with 5 flow rates of interest, ranging from 0.2 to 2 \(kg/s\):
Once the parametric Experiment starts, one simulation for each flow rate of interest will launch in parallel. The results from each simulation are available by expanding the Experiment tab:
If any result control has been defined, the results from all simulation runs will be compiled in a single plot. For example, we can check how the temperature of the transistor changes based on the water mass flow rate:

In the image above, we can easily see how much the temperature of the transistor changes with an increased water flow rate, allowing the user to choose the most efficient configuration.
With an improved simulation setup and result comparison, SimScale’s parametric experiments are a powerful tool in the design process of many equipments.