In the 19th century, large turbine-driven power generators were replaced with fossil-fuel-powered engines to meet industrial needs and economic demands. Paired with this was the implementation of nationally distributed power networks, running on, you guessed it, fossil fuels. But when global energy demands and climate change began to encroach on societal demands, a return to wind energy occurred in the early 21st century. This was also helped by a greater understanding of aerodynamics and advances in materials (particularly polymers). In this article, we will discuss how wind turbine design, and specifically wind turbine blade design, is being optimized yet again, but this time with the help of online simulation.
Wind Turbines: Advantages and Disadvantages
Today, the majority of wind turbines are designed to generate electricity, and are actually considered one of the fastest-growing energy sources in the world. The advantages of wind turbines include, but are not limited to, cost-effectiveness, being a clean-fuel source, sustainability, and the ability for these mechanisms to be built on existing plots of land such as farms or ranches (in some cases, they are even placed offshore as ocean wind farms!).
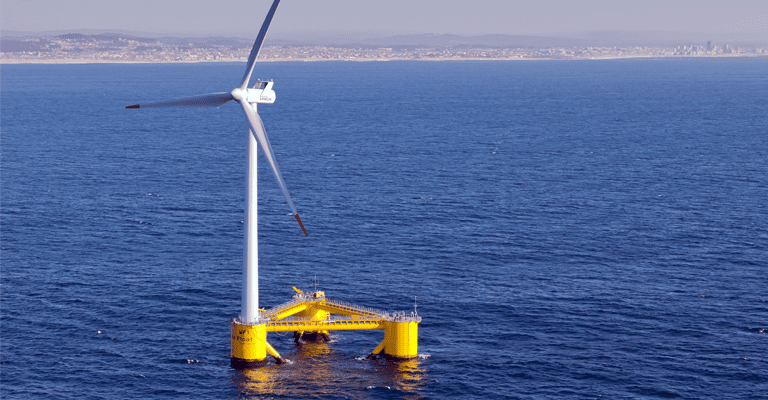
However, wind power is also challenging as areas of high wind are usually remote and far from those that need the electricity. Wind power still needs to compete on a cost-basis with fossil fuel sources in order to be implemented, and is not considered the most profitable use for a given plot of land in some cases. Along with this, the wind turbine blade design could hurt local wildlife (i.e., birds). Due to these reasons, it is more important than ever to optimize wind turbine designs to mitigate these challenges.
Wind Turbine Design
A turbine with a shaft-mounted horizontally parallel to the ground is called a horizontal axis wind turbine or HAWT. Most HAWTs have two- or three-bladed rotating propellers. A vertical axis wind turbine (VAWT) has its shaft normal to the ground. Whether horizontally or vertically oriented, wind turbine blades convert the energy of the wind into usable shaft power called torque. This is produced by taking the energy from the wind by decelerating the wind as it moves over the blades. The forces which decelerate the wind are equal and opposite to the thrust type lifting forces which rotate the blades. The key to an optimized turbine, and thus increased wind power generation, lies within the wind turbine blade design.
Wind Turbine Blade Design
Wind turbine blades generate lift with their curved shape. The side with the most curve generates low air pressure, while at the same time high-pressure air beneath forces on the other side of the blade-shaped aerofoil. The net result is a lifting force perpendicular to the administration of flow of the air over the turbine’s blade. The trick here is to design the rotor blade in such a way as to create the right amount of rotor blade lift and thrust, producing optimum deceleration of the air and therefore better blade efficiency.
If a turbine’s blades rotate too slowly, there is too much wind that passes through undisturbed, and thus it does not obtain as much energy as it potentially could. On the other hand, if the propeller blade rotates too quickly, it acts upon the wind like a large flat rotating disc, which creates a great amount of drag having an equal but opposite effect.
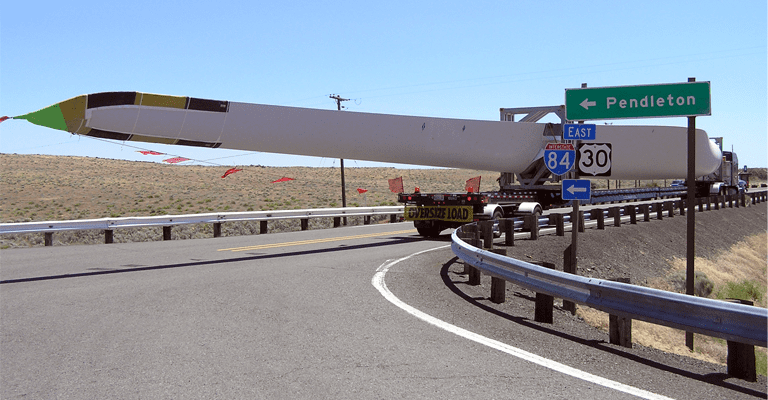
The optimal tip speed ratio (TSR), which is defined as the ratio of the speed of the rotor tip to the incoming wind speed, depends on the rotor blade shape profile, the number of turbine blades, and the wind turbine propeller blade design itself. So which is the best blade shape and design for wind turbine blades?
Generally, wind turbine blades are shaped to generate the maximum power from the wind at the minimum construction cost. But wind turbine blade manufacturers are always looking to develop a more efficient blade design. Constant improvements in the design of wind blades have produced new wind turbine designs which are more compact, quieter and are capable of generating more power from less wind. It’s believed that by slightly curving the turbine blade, they’re able to capture 5 to 10 percent more wind energy and operate more efficiently in areas that have typically lower wind speeds.
The aerodynamic design principles for a modern wind turbine blade are detailed, including blade plan shape/quantity, aerofoil selection, and optimal attack angles. These designs can be further optimized and tested using an online wind turbine simulator tool.
How to Optimize Your Wind Turbine Blade Design with a Wind Turbine Simulator Tool
So how can you optimize a wind turbine blade design? What shape will help you yield the greatest amount of net energy? In order to determine the type, shape, size, etc. of your wind turbine design, engineers need to test different environmental factors that will fluctuate in the real-world such as air velocity and temperature. This can be done through online computational fluid dynamic (CFD) simulation through online platforms like SimScale. Evaluating this generally focuses on the wind turbine blade design and the testing of different design iterations. For example, flat blades are the oldest wind turbine blade designs that are still utilized today, however, they are becoming less popular due to their lessened rotational abilities due to the wind pushing back against the blade itself during the up-stroke. This is because the blades are acting like huge paddles moving in the wrong direction, pushing against the wind giving them the name of drag-based rotor blades.
Yet, flat blades are easier to design compared to other wind turbine blade designs. They are cheaper to produce, easier to duplicate for blade shape and size consistency, and require less expert-level knowledge to implement. With a flat wind turbine blade design, there is still room to optimize through online simulation and evaluation of design iterations; from testing different materials (through FEA simulation), to length and width various, all pitted against a range of seasonal or applicable environments. Using SimScale, many of our users simulate their wind turbine designs in different air velocities to optimize their designs.
Wind Turbine Simulator: SimScale
With SimScale’s wind turbine simulator using computational fluid dynamics, users can optimize their wind turbine blade designs by copying this public project and using it as a template, or even starting from scratch with their own turbine design.

In this example project, the airflow around a horizontal axis wind turbine (HAWT) and the resulting forces on the rotor are simulated. With some instructions on how to run the simulation coupled with the achieved results, this project demonstrates how SimScale can be used to evaluate wind turbine designs of any size or shape.

This project is just one of many that demonstrates how SimScale can be used to assess the performance of a wind turbine, as well as many other applications. Explore SimScale’s public project library now!
For more wind turbine resources from SimScale, check out these blogs:
- Optimizing a Micro Wind Turbine with CFD | American Wind
- Wind Farm Optimization with Turbine Placement Using CFD Simulations
- Working in Wind Engineering? Here’s Why You Need SimScale