The centrifugal pump stands as the workhorse of the industry, driving everything from water supply systems to complex industrial processes. The towering skyscrapers, the underground subways, and even the water fountains in the park – all owe a nod to centrifugal pumps.
But what makes them tick? How do they transform a simple rotation into the steady flow that powers humans’ daily lives? And how can one simulate and analyze their performance to achieve design excellence?
This is where SimScale Turbomachinery CFD steps in, your ultimate solution for simulating centrifugal pumps and calculating their operational efficiency.
What is a Centrifugal Pump?
A centrifugal pump is a hydraulic machine designed to transport fluids by converting rotational kinetic energy from an external source (e.g., an electric motor) into hydrodynamic energy. This transformation makes it possible for fluids to move from one place to another with impressive efficiency and scale.
Before engineering simulation tools like SimScale, engineers relied heavily on manual calculations and physical tests. Optimizing designs meant repeated physical testing, which was both time-consuming and tedious. Today, with cloud-native engineering simulation software, engineers can visualize flow patterns, pressure zones, and potential areas of cavitation within the digital environment. If inefficiencies are detected, modifications can be made instantly to the digital model and re-simulated.
How Does a Centrifugal Pump Work?
Key Components of a centrifugal pump
The main components of a centrifugal pump are:
- Impeller: The spinning part with curved blades. Fluid enters through its center, called the ‘eye,’ and exits by being pushed out through the blades.
- Casing: The housing that surrounds the impeller. Two main types of casings exist – volute and diffuser.
- Volute casings have a curved shape, helping increase fluid pressure as the fluid flows.
- Diffuser casings use stationary blades to increase fluid pressure.
- Shaft: Connects the impeller to the motor, allowing the impeller to spin.
In addition, centrifugal pumps also require shaft sealings (mechanical seals or packing rings) to prevent fluid leakage, a shaft sleeve to protect the shaft and position the impeller-shaft combo precisely, and bearings to minimize friction between the rotating shaft and the stator.
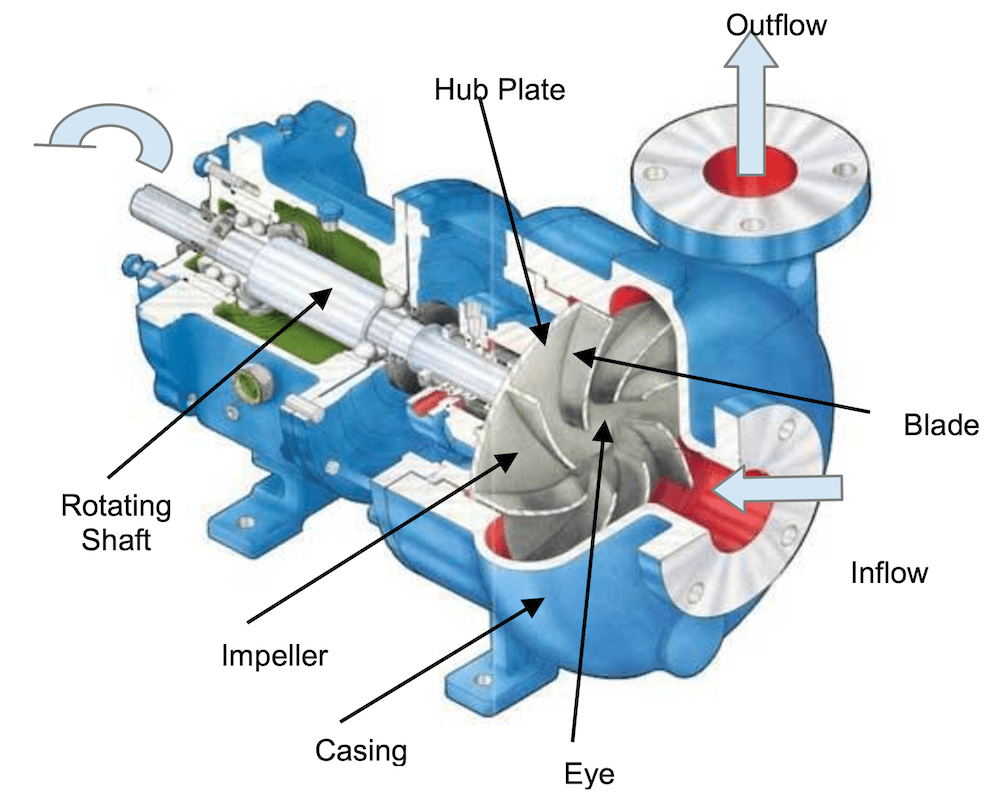
These parts can be divided into the pump’s wet end and mechanical end.
- The wet end components are responsible for the pump’s hydraulic performance; these are the impeller and the casing. In some designs, the first radial bearing can also belong to the wet end, where it is water-filled.
- The mechanical end components support the impeller within the casing; these are the shaft, shaft sleeve, sealing, and bearings.
Working Principle of Centrifugal Pump
When the electric motor turns the shaft, the impeller starts spinning (typically rotating at speeds ranging from 500-5000 rpm). This draws fluid into the pump. The spinning impeller pushes the fluid outwards.
The design of the casing then guides this fluid (either volute or diffuser), increasing its speed and pressure. The fluid exits the pump, typically from an outlet at the top of the casing.
Pump Comparison: Centrifugal vs Positive Displacement
Pumps are used to move fluids in different settings. Generally, the two main types of pumps are positive displacement pumps and centrifugal pumps. Positive displacement pumps keep a constant flow rate, whereas centrifugal pumps’ flow rate varies based on the fluid pressure. The choice of pump largely depends on the pump’s working principle, fluid viscosity, and application.
Positive displacement pumps are suitable for high-viscosity fluids and are used in food processing, oil refining, and pharmaceuticals. Centrifugal pumps, on the other hand, are suitable for low-viscosity fluids and are used in water treatment, irrigation, and heating/cooling systems.
The following table provides a direct comparison between centrifugal pumps and positive displacement pumps in terms of their operating principle, fluid type, flow rate, and more.
Characteristic | Centrifugal Pump | Positive Displacement Pump |
---|---|---|
Operating principle | Transfers fluid using centrifugal force | Traps and displaces fluid |
Fluid type | Best for low-viscosity fluids | Can handle high-viscosity fluids |
Flow rate | Variable | Constant |
Pressure | Variable | Constant |
Efficiency | Best at optimal operating point | Less affected by changes in pressure |
Cost | Lower | Higher |
Maintenance | Lower | Higher |
Applications | Water supply, irrigation, industrial processes | Chemical processing, oil and gas, food and beverage |
Types of Centrifugal Pump
Centrifugal pumps are a subset of dynamic axisymmetric turbomachinery. There are different types of centrifugal pumps that can be categorized based on specific criteria, such as impeller types, design codes, and applications. Here is a brief overview of the three main types of centrifugal pumps: radial pumps, axial pumps, and mixed pumps.
1. Radial Pumps
In radial pumps, fluid flows radially outward from the impeller’s center, perpendicular to the main axis. This type of centrifugal pump is used in cases where flow is restricted, and the goal is to increase the discharge pressure. Therefore, radial pump design is ideal for applications that require a high-pressure and low-flow rate pump, such as water supply, irrigation, and industrial processes.
2. Axial Pumps
Axial pumps work by moving the fluid in a parallel direction to the axis of the impeller. The operation of axial pumps is akin to that of propellers. Their most notable usage comes into play when there is a large flow rate and relatively low-pressure head required, such as fire pumps and large-scale irrigation systems.
3. Mixed Pumps
Mixed pumps combine the features of radial and axial pumps. They are capable of delivering high flow rates and pressures, making them ideal for applications such as sewage treatment and power generation.
Radial Pump vs Axial Pump vs Mixed Pump
Here is a table that summarizes the key differences between the three types of centrifugal pumps.
Characteristic | Radial Pump | Axial Pump | Mixed Pump |
---|---|---|---|
Impeller | Closed | Propeller | Hybrid |
Flow direction | Perpendicular to axis | Parallel to axis | Angled to axis |
Head | Medium to high | Low to medium | Medium to high |
Flow rate | Medium to high | High | Medium to high |
Efficiency | High | Medium to high | Medium to high |
Applications | Water supply, irrigation, industrial processes | Fire pumps, large-scale irrigation systems | Sewage treatment, power generation |
Single-Stage, Two-Stage, or Multi-Stage Centrifugal Pumps
Another way of classifying centrifugal pumps is by the number of impellers they have (or the number of stages), and they can be referred to as single-stage, two-stage, and multi-stage centrifugal pumps. A single-stage pump has one impeller, a two-stage pump has two impellers, and a multi-stage pump has three or more impellers.
- Single-stage pumps are the simplest and most common type of centrifugal pump. They are well-suited for applications where medium flow rates and pressures are required.
- Two-stage pumps are more efficient than single-stage pumps at delivering high pressures. They are often used in applications such as firefighting and industrial processes.
- Multi-stage pumps are the most efficient type of centrifugal pump, but they are also the most expensive. They are used in applications where very high pressures are required, such as oil and gas production and chemical processing.
Applications of Centrifugal Pump
Centrifugal pumps are used in a wide range of applications that involve turbomachinery, including:
- Water Supply: Whether it’s pumping water to homes, industrial plants, or agricultural fields, centrifugal pumps ensure a steady water flow.
- General Industrial Processes: Since many manufacturing processes rely on the consistent movement of fluids, centrifugal pumps help in transferring chemicals. For example, in a petrochemical plant or circulating coolant in machinery.
- Cooling Systems: In HVAC (Heating, Ventilation, and Air Conditioning) systems, centrifugal pumps circulate coolant to maintain temperature balance.
- Sewerage: Centrifugal pumps remove unwanted water, especially in areas prone to flooding or in construction sites.
- Oil and Energy Sector: In oil refineries and power plants, centrifugal pumps transport crude oil and hot liquids.
- Food & Beverage Industry: Safe and consistent transfer of liquids, like juices, syrups, and dairy products, is crucial. Centrifugal pumps offer a contamination-free and efficient solution.
- Wastewater Treatment: For processing and recycling wastewater, these pumps facilitate the movement of water through various stages of treatment.
Advantages of Centrifugal Pump
Centrifugal pumps offer advantages that can be quite useful in a variety of settings and applications:
1. Corrosion Resistance
Many fluids can rapidly corrode pumps, but corrosion-resistant centrifugal pumps can manage different fluids without deteriorating, thanks to the corrosion-resistant properties of their materials. Businesses see an increased return on investment (ROI) as the pumps last longer and require fewer replacements, maintenance, or repairs.
2. High Energy- and Cost-Efficiency
Centrifugal pumps use less power to move liquids, making them cost-effective. Any mechanical engineer would appreciate the savings they offer in terms of energy costs and efficiency gains.
3. Straightforward Design
When you look at a centrifugal pump, you see simplicity in action. These pumps don’t have countless parts, making them easier to produce, set up, and look after. In the long run, their design can lead to fewer repairs and a longer life.
Given their design simplicity and established principles of operation, engineers can use computational fluid dynamics (CFD) and other simulation tools to model their behavior under different conditions.
4. Stable Flow
For processes that need a steady liquid supply, centrifugal pumps are the go-to. They deliver a continuous flow, making sure everything runs as it should. This predictability can be crucial, especially when consistency is key to quality control in production lines.
5. Compact Design
Centrifugal pumps, with their compact form, are a perfect solution. They can fit adequately into tight spots, making them a smart choice for workshops and factories where every inch counts.
Disadvantages of Centrifugal Pump
While their advantages can prove effective in industrial applications, centrifugal pumps also have some drawbacks:
1. Inefficiency with High-Viscosity Feeds
Centrifugal pumps are best suited for liquids that have a viscosity range between 0.1 and 200 cP. With high-viscosity fluids like mud or slurry, their performance drops because they need to overcome greater resistance, and maintaining the desired flow rate demands higher pressure.
2. Priming Required Before Use
Centrifugal pumps can’t just start up on their own when they’re dry; they need to be primed or filled with the liquid first. This limitation means they might not be ideal for applications with intermittent liquid supply.
3. Susceptibility to Cavitation and Vibrations
Cavitation occurs when vapor bubbles form in the liquid being pumped due to sudden pressure changes, and then collapse when they reach areas of higher pressure. This phenomenon can lead to intense shock waves that damage the pump’s impeller and casing. The aftermath of cavitation is often visible as pitting or erosion on the impeller and the casing.
Cloud-Native Simulation for Industrial Machinery Manufacturing
Our latest eBook explores how cloud-native simulation is transforming industrial machinery manufacturing challenges into opportunities. Download it for free by clicking the button below.
Centrifugal Pump Simulation With SimScale
By utilizing Turbomachinery CFD in SimScale, engineers can analyze their centrifugal pump’s performance and efficiency and identify areas of improvement in the design to ensure optimal operation. This analysis and design optimization can be further accelerated thanks to SimScale’s cloud-native nature, which enables engineers to run multiple simulations in parallel directly on their web browser without having to worry about any hardware limitations or installation complexities. They can also collaborate with team members and customer support in real time by simply sharing the link to their simulation project. As a result, engineers are empowered to innovate faster and optimize their pump designs more efficiently using SimScale’s powerful CFD solvers.
Here’s how SimScale helps the mechanical industry in centrifugal pump simulation:
1. Robust Meshing
SimScale’s Multi-purpose CFD solver provides a robust meshing strategy, generating an automated body-fitted mesh which is crucial for capturing the fluid flow accurately within and around the pump geometry.
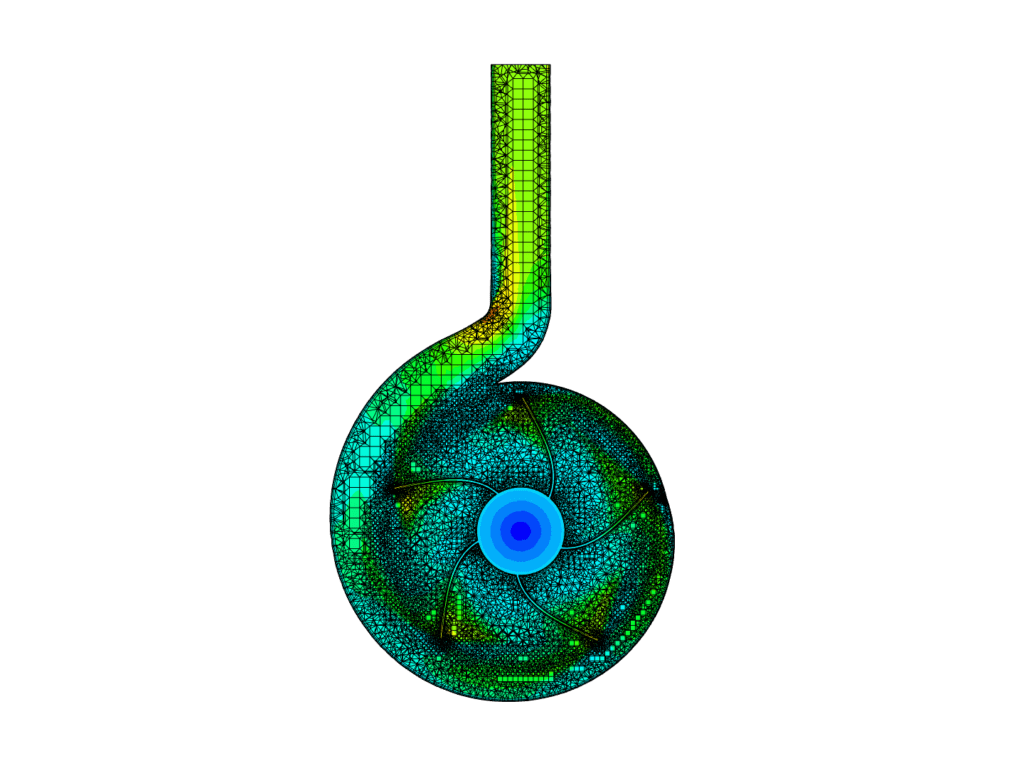
2. Flow Analysis
SimScale allows for the analysis of various flow regimes including incompressible, compressible, laminar, and turbulent flows. This is essential in understanding how the fluid will behave under different operating conditions.
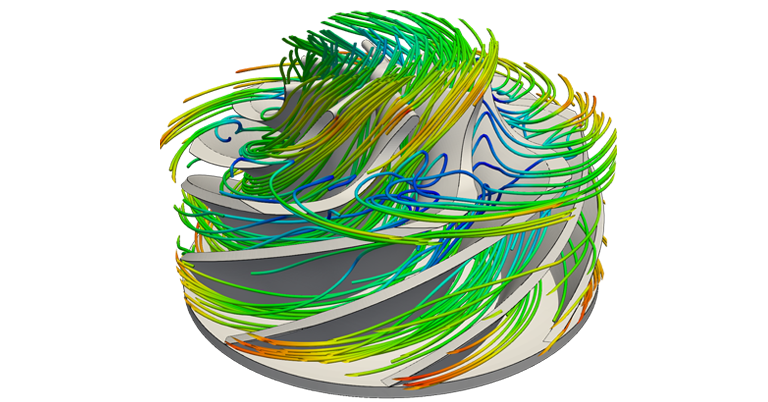
3. Cavitation Simulation
Cavitation, a common challenge in centrifugal pumps, can be simulated to understand its impact on pump performance. SimScale’s Multi-purpose multiphase CFD solver computes the space occupied by each phase, providing insights into cavitation effects in pumps.
4. Pump Curve Generation
SimScale enables engineers to generate pump curves within a few hours, whereas other simulation tools can take up to a few days. This is crucial for ensuring the pump meets the desired performance criteria across a range of operating conditions.
5. Transient Analysis
The platform supports full transient analysis, modeling fluid flow in a time-accurate manner, which is vital for capturing the dynamic behavior of the pump under various operational scenarios.
Simulate Your Centrifugal Pump Design in SimScale
Centrifugal pumps have revolutionized industries with their efficiency, compact design, and ability to move fluids at varying rates and pressures. While centrifugal pumps come with their set of challenges, advancements in engineering simulation and CFD tools like SimScale have enabled engineers to optimize designs and predict performance.
Sign up below and start simulating now, or request a demo from one of our experts. You may also follow one of our step-by-step tutorials, such as the advanced tutorial on Fluid Flow Simulation Through a Centrifugal Pump, or check out the following on-demand webinars:
- Get Ahead of the Pump Curve: Simulation-driven KSB Circulator Pump Optimization using CAESES (On-demand webinar)
- Parametric Studies for Rotating Machinery: Hands-On Workshop with SimScale (On-demand webinar)
References
- WANG Xiu-yong,WANG Can-xing. “Performance Prediction of Centrifugal Pump Based on the Method of Numerical Simulation.” Journal of Fluid Machinery (2007)