Wind tunnel simulation is primarily used to test the aerodynamics of and visualize flows around an object. A wind tunnel simulator can help the engineering design process by optimizing lift and drag, increasing top speed, detecting and eliminating high wind speed zones, and reducing wind noise for automotive, aerospace, and building planning and construction operations. Yet with this type of experimentation comes increased prototyping, manufacturing lead times, and operational costs. Wind tunnel testing is often combined with computational fluid dynamics (CFD) simulations. This article will explore what applications wind tunnel experiments are used for, and how alternatives in the form of virtual wind tunnel testing can act as an additional cost-effective solution.
Wind Tunnel Experiments
Architects and aerodynamicists alike use wind tunnel experiments to test everything from buildings to aircraft designs. A few existing wind tunnel types that are used today are low subsonic, transonic, supersonic, and hypersonic. These types of tunnels are classified based on the amount of wind speed they can produce (i.e. the subsonic’s speed is lower than the speed of sound).
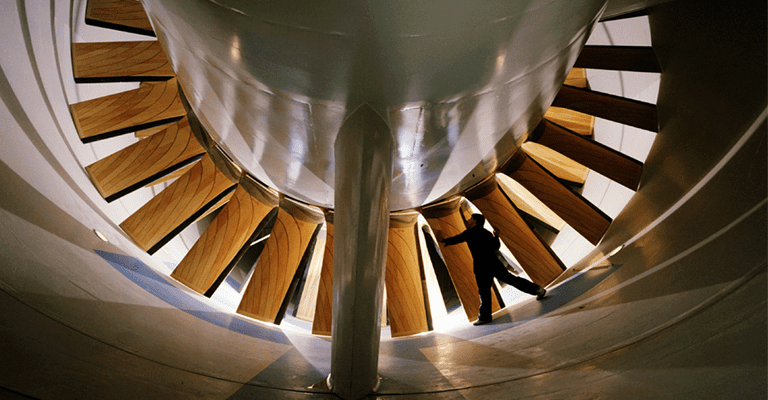
During a test, the wind tunnel model is placed in the test section of the tunnel, and fluid (in this case, air) is made to flow past the model. There are four main types of wind tunnel testing: aerodynamic forces upon the structure, the total pressure measurement of wind force on the object, the flow of air around the model, and, finally, flow visualization techniques to provide diagnostic information.
Wind Tunnel Testing for Aerospace
For aerospace engineers, wind tunnels are commonly used to test aircraft and engine aerodynamics. This type of evaluation began at the end of the 19th century, in the primitive days of aeronautic investigation. To date, there is no wind tunnel that can test the full size of a passenger air vessel, but tunnels do range in size and can test everything from large-scale models of airplanes and other aerospace vehicles to small-scale prototypes and replicas.
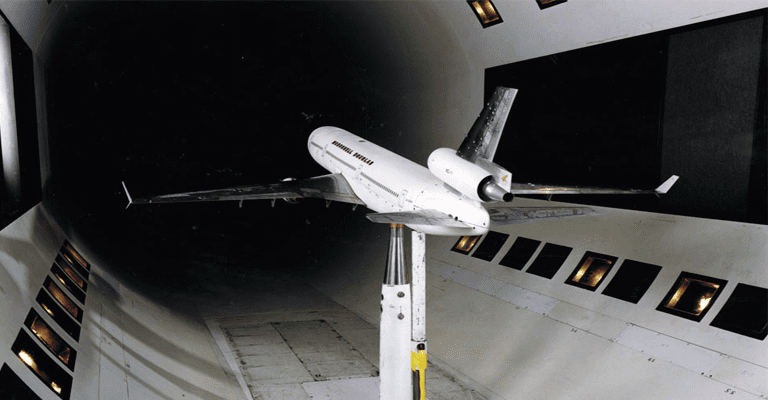
When testing aircraft, the lift and drag forces are measured through outputs received from force balance testing and resulting balance signals. Pressure forces are quite difficult to evaluate in a full-scale aircraft simulation due to the number of instrumental pressure taps required. Through wind tunnel experiments, a diagnostic test can not provide overall aircraft performance, but can help the engineer to better understand how the fluid moves around and through the model. This is because different types of instrumentation can be employed, from steady state or unsteady flow to time-varying or time-dependent, but not in parallel for a holistic understanding.
Virtual Testing for Aerospace Applications
For many aerospace applications, wind tunnel experiments are limited by not providing robust results in a timely manner or failing to simulate real-world forces accurately enough. Virtual simulation, or online CFD and FEA, can make this possible. For example, the behavior of aircraft landing gear in reaction to stresses as a result of the airflow against the motion of the airplane can be studied. This project along with the post-processing image below provides a great example of how the results of virtual wind simulation can help engineers compare different designs as well as various materials to be used for the multiple components that go into the simple-looking but complicated structure.
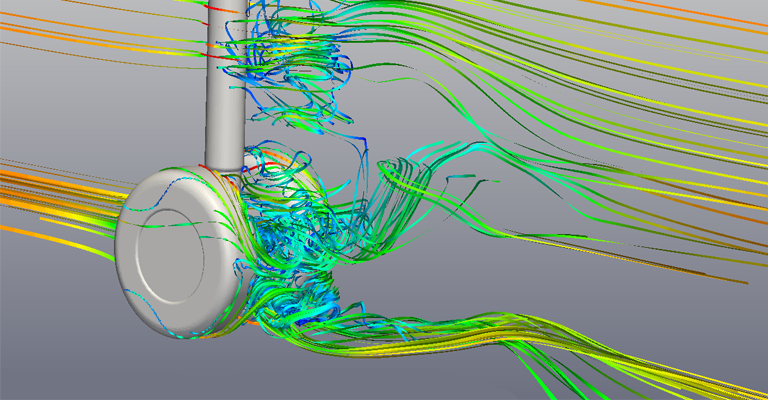
Download our ‘Wind Engineering’ white paper to learn about building design, wind loading implications, pedestrian wind comfort, natural and mechanical ventilation, pollution mitigation, and more!
Wind Tunnel Testing for Automotive
Compared to the aerospace industry, automotive wind tunnel testing didn’t become a mainstream evaluation route until the late 1920’s when speed became an important design factor. One of the first aerodynamic cars that were manufactured after the automotive wind tunnel revolution was the 1934 Edsel Ford Speedster, marking history as a radical departure from traditional car design at the time.
Engineers soon found that wind tunnel experiments allowed them to acquire data on the aerodynamic forces, drag, lift, side force and moments; pitch, yaw, and roll; variation of aerodynamic forces and moments with yaw; surface pressure distribution; the influence of different vehicle details; vehicle cooling drag; assessment of brake cooling flows; and more to optimize their designs. While small-scale and full-testing exists in the automotive industry, it is becoming increasingly popular to replace the cheaper model-scale evaluation stage with CFD and instead go directly to full-scale aerodynamic testing. This trend has emerged recently as online CFD simulation has increasingly been used in tangent with vehicle development to virtually test and make predictions for different aspects of a car’s design.
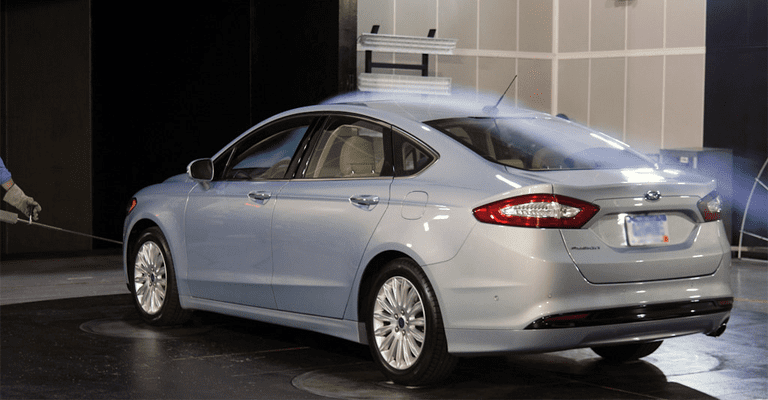
Virtual Testing for Automotive Applications
As aerodynamics plays a significant role in the performance of automobiles, good aerodynamic planning helps augment the down-force and hence, the traction of the vehicle on the road, mitigating risk of lift-off, skidding, and potential accidents. Along with this, reducing drag force decreases fuel consumption, which in turn saves money for the consumer and reduces the carbon footprint of the product. When designing a car, engineers are increasingly relying on CFD simulation before the initial model is created in order to evaluate the predicted airflow around the vehicle, computing the regions of high pressure, wind velocity, and wake regions. This project, and image below, provides a great example of how employing a virtual wind tunnel online via steady state turbulent flow analysis with the K-Omega SST turbulence model can give valuable insights and save time and money compared to stand alone wind tunnel testing.
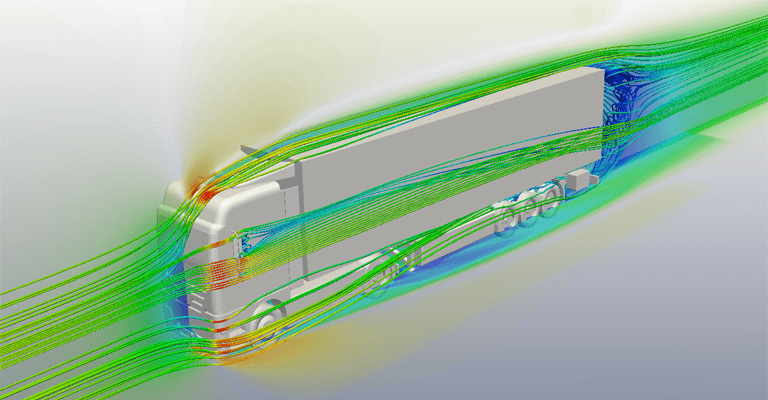
Wind Tunnel Testing for Buildings
With the influx of development in the construction industry, and the social demand for increased residential, commercial, and industrial buildings, the built environment is expanding like never before. With this comes an urban density increase paired with a skyline extension horizontally and vertically; sometimes the only space to build is up! With new, taller structures becoming the norm, the structural safety of these buildings must be evaluated. Structural integrity is often determined by its structural design to withstand wind loads, whereas the habitability of the buildings for living or working is often hindered with wind-induced vibration. In order to properly evaluate both structural integrity of wind-loading and habitability from the effect of across-wind vibration, wind tunnel testing of small-scale models is a method predominately used.
In order for architects and civil engineers to approve a design, Standard ASCE/SEI 49-12 provides minimum requirements for evaluating wind tunnel experiments in order to determine acceptable wind loading on built structures. This guideline takes into consideration wind loads, structural response to wind conditions, as well as cladding for a variety of wind-related weather conditions. Additionally, due to the crowding of structures in urban locations and the trend of atypical design of structures, the effect of wind is becoming harder to anticipate as it is constantly changing, and as a result, the pedestrian-level wind environment is becoming more and more affected.
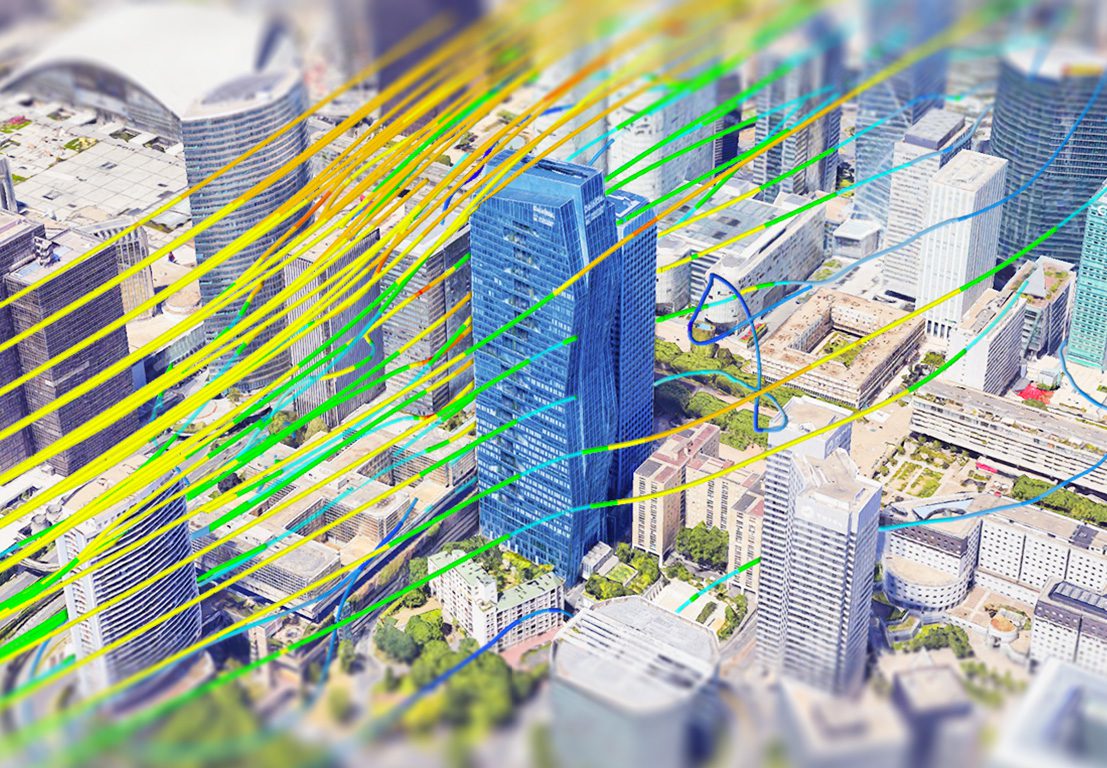
Explore CFD in SimScale
Virtual Testing for Buildings and Pedestrian Wind Comfort
To comply with all ASCE guidelines, FEA to determine structural integrity along with CFD to evaluate other aspects of wind loading and vortex shedding must be applied. This project and accompanying image provide a perfect example of both investigations being made possible through online simulation, as another way to verify and validate designs before constructing.
In addition to the effects of wind on buildings, the pedestrian-level wind environment must also be taken into consideration. While wind tunnel testing fails to focus on this level of intricate analysis, CFD can be employed to pinpoint areas of harsh winds, recirculation, and general pedestrian-level discomfort, as shown in this project from SimScale.
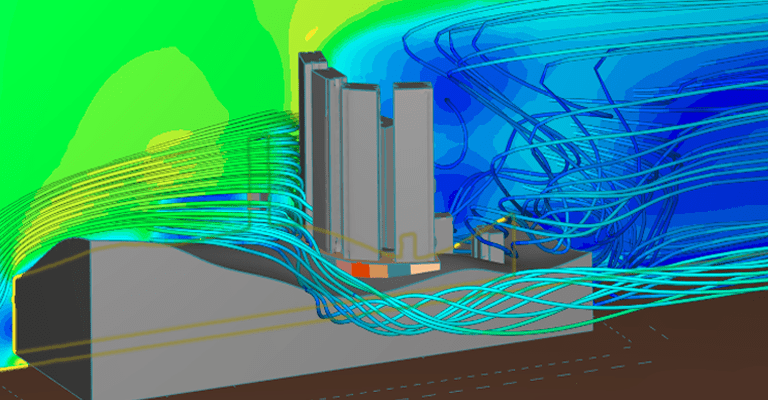
Limitations of Wind Tunnel Experimentation
Despite its widespread use across many industries and for an even wider range of applications, there are some prevailing limitations of solely using wind tunnel testing that have many engineers looking for alternative solutions to further verify and validate their designs. The most obvious limitation is size, as almost all simulated designs must be scaled down to fit inside the wind tunnel simulator. This can have negative impacts and change aerodynamic characteristics such as Reynold’s number. The size also constrains any sort of motion, which is crucial for evaluating aerospace or even automotive designs.
Along with the size of the tunnel, the walls acting as a boundary layer can influence the flow and create some clogging as they constrain and limit the size of the domain. Although this can be mitigated by more sophisticated wind tunnel components, it still exists as a variable. Wind tunnel experiments also incur large costs, from running the simulations to creating countless prototypes, and results cannot be captured instantaneously. Virtual wind tunnel testing through online CFD and FEA bypasses these real-world issues, and provides an easy, fast, and cost-effective solution.
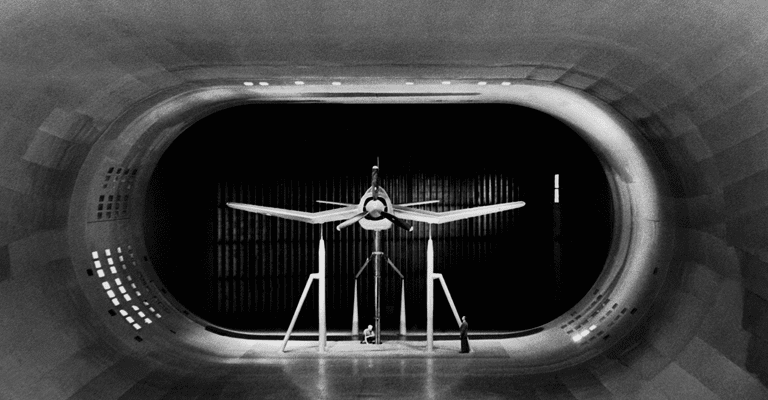
Virtual Wind Tunnel Online: Cloud-Based Simulation
With CFD and FEA from platforms like SimScale, engineers can easily access, evaluate, and get results from a virtual wind tunnel online. Using cloud-based simulation, you can even run simulations in parallel to test multiple design iterations at the same time, or investigate different aspects of a design in tangent, like vortex shedding and wind loading as shown in the aforementioned project. Virtually evaluating designs not only saves operational costs and time, but saves resources by eliminating the need for physical prototyping.
To get inspired about what you could test in a virtual wind tunnel online, check out SimScale’s public project library.