Advanced modeling and simulation tools necessary for virtual prototyping have the reputation of being the exclusive domain of trained specialists in numerical analysis in big companies with even bigger budgets, working on highly sophisticated products, while for simpler projects it might seem like an overkill. If CFD or FEA simulation is something you’ve never used before for design validation, then integrating it into your product development process might seem too challenging to be worth it. Unfortunately, such perspective often leads to engineers ending up with tools that weren’t built for the complex calculations they have to perform in order to create efficient and reliable product designs.
What is Computer-Aided Engineering (CAE)?
Computer-aided engineering (CAE) is a term used to describe the use of computer software in the product engineering process, from design and virtual testing with sophisticated analytical algorithms to the planning of manufacturing. CAE solutions support the engineering process, allowing designers to perform tests and simulations of the product’s physical properties without needing a physical prototype. CAE or engineering simulation has become the go-to tool for engineers in many industries, replacing older design and validation practices.
Sounds intimidating? Let’s consider the alternatives.
Traditional Product Design Practices
Excel spreadsheets. Due to the predominance of the Microsoft Office environment, many designers still cling to Excel spreadsheets for engineering calculations. And while it might work well for the finance department, it often results in expensive errors in product development.

According to Ray Panko, a professor of IT management at the University of Hawaii, “spreadsheets, even after careful development, contain errors in 1% or more of all formula cells. In large spreadsheets with thousands of formulas, there will be dozens of undetected errors” [1].
Over the course of his research, he also found that:
- 30% of spreadsheets contain errors
- 90% of sheets with 150+ rows have errors
- 50% of spreadsheet models have material defects
Even for the simpler calculations, which Excel is capable of performing, several issues make it an unsuitable engineering tool—the biggest being the fact that it’s unreviewable. The more detailed and complex the spreadsheet is, the easier it is to get blinded by details and miss errors. It is a common tool that too frequently ends up being used in problems it is not suited for. And while the fact that it’s easily available and affordable makes it a tempting choice, the calculation errors and resulting design flaws tend to be far more costly than more reliable alternative engineering tools.
Physical prototypes. Producing multiple physical prototypes and testing them is one of the oldest product development practices. And while it has its benefits, there are many cases where rapid prototyping is impractical, impossible or inefficient.
For instance, for early concept models where changes are fast and frequent, simulation and virtual prototyping would be far more useful and cost-efficient. The same would be true for later product development stages, which involve reviewing and refining the designs of objects like planes and buildings. In those cases, creating physical prototypes of all necessary design components would be pushing the limits of both cost and time. Physical prototypes are also quite restrictive when it comes to analyzing complex physical phenomena, such as fluid flow.
It is important to note that physical and virtual prototyping are not two competing technologies; they are complementary. It is not recommended to try and entirely eliminate physical prototyping from the design process, but instead, integrate virtual prototyping and simulation at appropriate development stages to address its weaknesses and limitations.
Advantages of Virtual Prototyping and CAE
Engineering simulation has been steadily replacing traditional testing techniques across many industries. The shift makes sense when we consider the advantages offered by virtual prototyping:
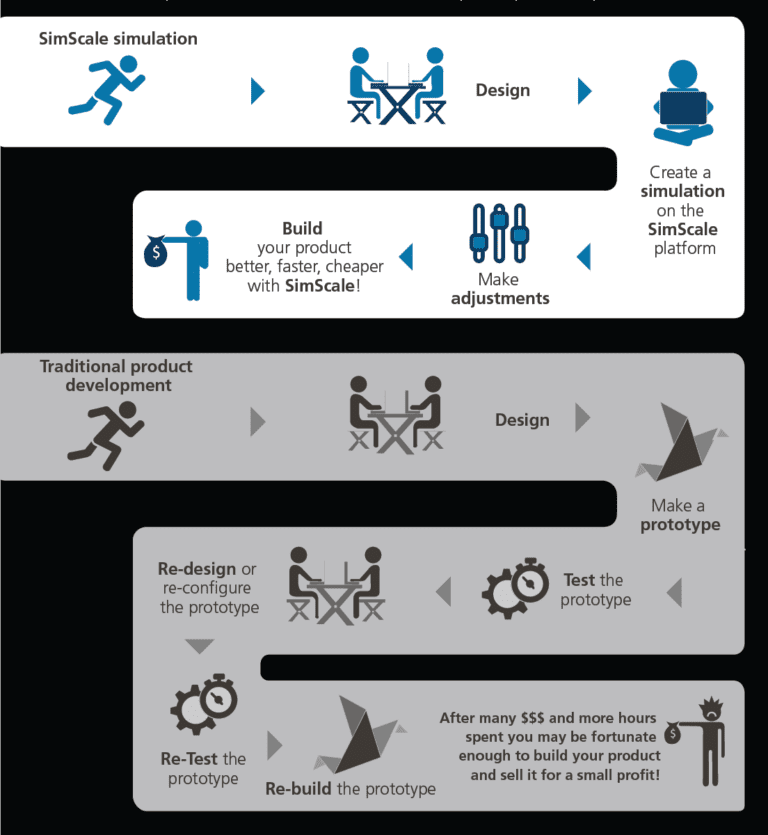
Shorter time to market. The traditional product development process typically involves building a physical prototype and taking it to the lab for testing. The testing will likely reveal several design flaws that require a re-design or re-configuration. This build–test–redesign–retest cycle can stretch the development schedule indefinitely. Virtual prototyping, on the other hand, eliminates the unnecessary loops from the design optimization process, by allowing virtual testing and design adjustments, cutting both time and costs of development as a result.
Higher design quality. Performing engineering calculations using a spreadsheet and then building and testing a prototype can miss some fundamental errors. These errors might result in design flaws that will not become apparent before the product gets manufactured and distributed, resulting in warranty costs and even recalls. And while CAE does not automatically guarantee a flawless design, using fluid flow or structural simulation tools allows engineers to test their products under a much larger variety of conditions and considerably improve their reliability and durability.
More competitive product. Overly relying on physical experimentation limits the number of creative ideas the designer can test. Virtual prototyping, on the other hand, is far less costly and time-consuming and allows engineers to freely experiment with innovative designs and scenarios, developing a highly competitive product in terms of functionality, performance and exterior design.
Success Stories
Since the launch of the SimScale cloud-based CAE platform, we have collected numerous user success stories of companies who leveraged our virtual prototyping and simulation functionalities to build their products better, faster and more cost-efficiently.

Johnson Screens, Aqseptence Group. Johnson Screens used SimScale CFD to verify the airflow through their architectural radiator grille that would be used in a high-profile skyscraper in New York. By running a virtual test which took only 18 minutes, the team was able to find an accurate measure of the pressure drop and provide professional flow contour visualizations to their customer. The company estimated that in order to conduct the same analysis with a physical experiment, it would need approximately $7,000-$15,000 and a few months of time.
L&T Construction. L&T Construction, part of the Larsen & Toubro multinational company, used virtual prototyping to optimize the structures in the sump cum pump house to ensure that the flow reaching the pumps is free from any vortices. With SimScale, the L&T team reduced the time to solve the problems in the sump geometry by approximately 15 days. Moreover, almost $38,000 in costs were saved.
…And many more! Read more success stories with SimScale on this page.
CAE Starter Kit
Ready to add your success story to the ones above? Here’s everything you need to get started.
Software. Don’t be intimidated by the 5-digit prices charged by many traditional CAE software providers. SimScale grants you access to the full scope of the simulation capabilities of its platform. Simply create a free Community Account. If you’d like to learn more about the SimScale cloud-based platform and its capabilities, download this features overview.
Hardware. Don’t have access to a supercomputer? With the emergence of cloud-based CAD and CAE tools, this is no longer a barrier—platforms like Onshape and SimScale grant you access to their full design and simulation functionalities directly from a web browser. SimScale is being constantly maintained and upgraded, so all users share the same experience without any additional maintenance costs. Your CAD and simulation data is protected by one of the world’s strictest data protection and privacy standards to give you peace of mind.
Expertise. Traditional on-premises software is made for experts in numerical analysis, rather than product designers and engineers. While running complex simulations and getting accurate reliable results is by no means easy, the expertise gap can be minimized with:
- Intuitive UI
- Large simulation template library
- Live support via chat or forum
- Free training materials
Any of the public projects in the SimScale Library can be imported into your workspace, so you can simply exchange the CAD model, reassign the boundary conditions and run it without having to know too much about simulation upfront.
Conclusion
Having the right tools alone is not enough to extract real value from them. For firms that have no experience using simulation in their product development process, integrating CAE into their workflow can be a challenge. The company has to fully commit to a new methodology.
In order to truly shorten your design cycle times and get a better product to market faster, it is important to make virtual prototyping and simulation tools an integral component of your product development process. Using CAE tools from design conception to manufacturing delivery and not an afterthought will enable you to reap all their benefits.
It is important to understand here that committing to this change would mean it might take longer before you have the first piece of hardware in your hands. Your main goal, however, is to cut the total design process time and lower the costs, while ensuring the best possible quality of your final product—and engineering simulation can make that possible.
References
- Raymond R. Panko, University of Hawaii, What We Know About Spreadsheet Errors