Vibration in rotating machinery refers to the oscillation of components like shafts, bearings, and rotors caused by mechanical forces, imbalances, or other dynamic factors. If unmanaged, excessive vibration can reduce efficiency, cause premature wear, or lead to catastrophic failures.
Rotating machinery is essential to power generation, automotive, and aerospace industries, where reliability and performance are crucial. That is why minimizing vibration in such machinery is critical. For instance, in power plants, turbine vibrations can affect output, while in aerospace, vibrations can compromise the safety and performance of jet engines. In the automotive sector, vibrations in engines and drivetrains can cause inefficiencies, leading to increased fuel consumption or damage over time.
Unmanaged vibration introduces risks like mechanical wear, increased maintenance costs, and safety hazards for operators. Over time, this can result in machine downtime, loss of productivity, and higher operational costs. Addressing vibration early in the design phase or through continuous monitoring and vibration simulation helps maintain the reliability and performance of rotating machinery.
Causes of Vibration in Rotating Machinery
Vibration in rotating machinery can stem from several factors contributing to imbalanced forces and mechanical stress. The most common causes include misalignment, uneven loading, mechanical wear, and resonance. These factors often interact, complicating both the diagnosis and mitigation of vibration-related issues in rotating machinery.
Misalignment
Misalignment in rotating machinery occurs when shafts deviate from their intended axis due to installation errors, thermal expansion, or operational shifts. This generates reaction forces, increasing vibration amplitudes and stressing critical components like bearings and shafts. Misalignment often causes vibration frequencies at twice the shaft speed, becoming more pronounced as it worsens [1].
Uneven Loading
Uneven loading, often referred to as unbalance, occurs when the distribution of mass around the center of rotation is unequal. This imbalance results in significant vibrations, making it one of the most common causes of excessive vibration in rotating machinery. Unbalance can lead to increased mechanical stress, energy losses, and higher levels of noise and heat, all of which degrade machine performance over time [2].
Mechanical Wear
Mechanical wear, particularly in components like bearings, gears, and rotors, is a major source of vibration. The degradation caused by high-speed rotations, heavy loads, and harsh conditions increases vibration, often resulting in misalignment or imbalance. By detecting wear early through vibration analysis, engineers can prevent performance degradation and costly breakdowns, ensuring the longevity of machinery components [3].
Resonance
Resonance occurs when a component’s natural frequency matches external forces, amplifying vibrations. This can turn minor imbalances into major issues, causing wear and risking failure, particularly in supporting structures. Vibration analysis is essential to detect resonance and prevent catastrophic damage.
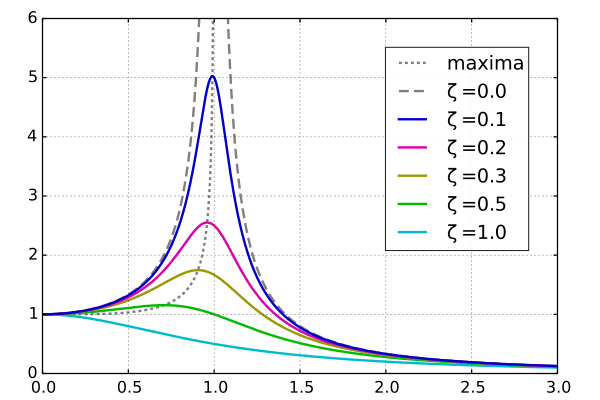
Solutions for Reducing Vibration in Rotating Machinery
Addressing vibration in rotating machinery requires a combination of best practices, including proper alignment and balancing, structural modifications, vibration isolation techniques, and regular maintenance. By proactively managing these factors, engineers can significantly reduce the risk of vibration-related issues, ensuring smoother operation, improving performance, and extending the lifespan of machinery.
Alignment and Balancing
Proper alignment and balancing are crucial to minimizing vibration in rotating machinery. Alignment tools such as laser alignment systems help ensure components are properly aligned. On the other hand, the balancing process involves calculating the force vector generated by the unbalanced mass, which can be done using accelerometer sensors and tachometers to acquire the vibration levels and phase angles. A test mass is added temporarily to evaluate the system’s response, and the correction mass is determined based on the disturbance caused by the test mass. This process is repeated until the system reaches an optimal balance, minimizing vibrations and ensuring smooth operation [4].
Simulation is another way to visualize and analyze alignment and balancing issues. SimScale’s simulation capabilities allow engineers to simulate different alignment and balancing scenarios, making it easier to fine-tune the balancing process virtually before applying corrective measures in real-world applications.
Structural Modifications
Structural modifications are essential for reducing vibrations in high-speed systems, such as those in aviation, automotive, and power generation. Techniques like adding dampers, reinforcing supports, or altering structural design enhance stability and minimize vibrations.
Squeeze film dampers (SFDs), which use a thin fluid layer to absorb vibration and dissipate energy, are commonly used in industries like aircraft engines and centrifugal compressors to improve efficiency and reduce vibration risks [5].
Through simulation, SimScale enables engineers to test the effects of structural modifications on machine performance, allowing them to analyze the impact of dampers and supports on vibration reduction before implementing physical changes.
Vibrational Isolation
Vibration isolation techniques help reduce vibration transmission between machinery components, ensuring smoother operation and less wear on sensitive parts. Passive methods, like spring-damper systems, are simple and effective at absorbing energy. Active isolation uses sensors and actuators for precise vibration control, though it’s more costly and complex.
Semi-active isolation adjusts system properties, like stiffness, in real time for better control with lower energy use. Hybrid systems combine these approaches, making them ideal for high-precision machinery like spacecraft [6]. SimScale’s vibration analysis tools can help simulate different isolation techniques and assess their effectiveness in various operational environments, optimizing vibration isolation strategies for specific machinery.
Regular Maintenance
Regular maintenance is critical for preventing vibration-related issues in rotating machinery. Worn-out components, loose parts, and improper lubrication can all contribute to excessive vibration. By performing routine inspections and replacing worn components, engineers can prevent the onset of mechanical issues that lead to vibration. Keeping components properly lubricated also ensures smooth operation, reducing friction and the likelihood of vibration. With SimScale, engineers can predict when maintenance is needed by analyzing wear patterns and identifying components at risk of failure.
Vibration Analysis Using Simulation Tools
Vibration analysis is essential for diagnosing and mitigating issues in rotating machinery. By leveraging vibration simulation tools, engineers can model and understand the root causes of vibration, such as misalignment, unbalance, and resonance. These tools, including Finite Element Analysis (FEA), allow for accurate predictions of how machinery components will respond under real-world conditions, helping to identify stress points, potential failure modes, and areas of high displacement.
Simulations provide the advantage of visualizing vibration patterns, making it easier to adjust designs early in the development process. Whether it’s modal analysis to identify natural frequencies or harmonic analysis to simulate response to periodic loads, engineers can evaluate machinery performance before physical testing. By combining simulation results with physical testing, engineers can validate designs early, minimizing the time and cost of modifications during later stages of development. SimScale offers a cloud-native platform that enables engineers to easily conduct these simulations, including advanced vibration analyses such as diagnosing root causes and optimizing machinery designs, all in a single online workbench.
Cloud-Native Simulation for Industrial Machinery Manufacturing
Our latest eBook explores how cloud-native simulation is transforming challenges of industrial machinery manufacturing (including rotating machinery) into opportunities. Download it for free by clicking the button below.
Advantages of SimScale for Analyzing Vibration in Rotating Machinery
SimScale offers an advanced cloud-native simulation platform that empowers engineers to identify, analyze, and mitigate vibration-related challenges with high efficiency and precision. Its broad range of capabilities, including modal, harmonic, and transient dynamic analysis, ensures that vibration issues are addressed comprehensively from the design phase through to optimization.
- Cloud-Native Simulation and Scalability: SimScale’s cloud-native architecture eliminates the need for costly, on-premise hardware, enabling engineers to access simulation tools anytime, anywhere, through a web browser. Its scalability allows multiple simulations to run in parallel, significantly reducing analysis time and accelerating the evaluation of design modifications and operating conditions. This flexibility enhances collaboration in real time and removes the overhead costs of hardware upgrades, maintenance, and software installation.
- Simulating a Wide Range of Scenarios and Parametrizing Designs: Engineers can use SimScale to simulate various vibration scenarios under real-world conditions, such as alignment changes, structural reinforcements, or vibration isolation techniques. SimScale’s FEA modal analysis, powered by the Code Aster solver, computes natural frequencies and oscillation modes, helping to prevent resonance and assess stress points. This allows engineers to predict how different design modifications influence system behavior, minimizing the risk of costly redesigns or failures during physical testing.
- Early Detection and Prevention of Vibration Issues: SimScale’s powerful simulation tools enable engineers to visualize vibration patterns and detect potential issues before they manifest in real-world operations. By running detailed simulations such as transient dynamic analysis, engineers can predict how machinery will perform under various conditions, including shocks or load changes, helping to identify weak points that may lead to failure. SimScale’s frequency analysis offers insights into how structures respond to specific vibration frequencies, ensuring that designs can be optimized for smooth operation while avoiding resonance. This proactive approach reduces the risk of physical test failure and speeds up the time to market by minimizing reliance on costly physical prototypes.
- Lower Testing Costs and Greater Confidence in Physical Testing: With SimScale’s vibration analysis tools, engineers can lower testing costs by iterating virtually to uncover design weak points before physical testing begins. Unlike traditional pass-or-fail physical tests, simulation provides deeper insights into the root causes of potential failures. Using frequency analysis to define a safe test range, engineers can approach physical tests more confidently, avoiding expensive failures due to resonance or other vibrational issues.
Case Study: Mitigating Vibration in Rotating Machinery with SimScale
One of the most significant challenges in rotating machinery is controlling vibration to prevent damage and maintain performance. A compelling example of how simulation can help solve such challenges is Hazleton Pumps’ use of SimScale to mitigate vibration issues in large pumps.
Hazleton Pumps, a manufacturer of heavy-duty pumps and pump systems, faced vibrational problems with one of their large, installed pumps weighing approximately 9 tons and operating at 800 RPM. Despite attempts to manually stabilize the pump with clamps, the vibration persisted, prompting the company to hire independent engineers. The engineers recommended significant modifications, including adding 500 kg of steel reinforcements, adjusting the subframe, and redesigning the bearing-to-shaft assembly, with an estimated cost of $40,000 per pump.
Instead, Hazleton turned to SimScale’s structural analysis tools to conduct a detailed multi-body modal analysis on the entire pump assembly. The simulation revealed that the eigenfrequency of the structure was around 780 RPM, meaning the pump was operating dangerously close to this resonance frequency. Equipped with this insight, Hazleton modified their operational procedures to avoid running the pump below 950 RPM, thus avoiding resonance-induced vibrations. They also implemented more cost-effective solutions, such as adding square tubing to the subframe, dramatically reducing costs compared to the original recommendations.
This case highlights how leveraging multidisciplinary simulation can help companies like Hazleton Pumps identify the root cause of vibration issues, optimize design modifications, and save time and money. Using SimScale’s cloud-based platform, Hazleton could perform rapid structural analyses and find effective solutions, replacing costly physical prototyping and trial-and-error methods with simulation-driven insights.
Read more about Hazleton Pumps’ use of SimScale.
Conclusion
Managing vibration in rotating machinery ensures optimal performance, prolongs machinery lifespan, and prevents costly breakdowns. By addressing common causes such as misalignment, uneven loading, mechanical wear, and resonance, engineers can mitigate the risks associated with excessive vibration. Failure to control vibration can result in reduced efficiency, increased maintenance costs, and even catastrophic failures that halt operations.
Vibration simulation technologies like those offered by SimScale play a pivotal role in diagnosing and solving vibration-related issues early in the design phase of rotating machinery. Through advanced capabilities such as modal, harmonic, and transient dynamic analysis, SimScale enables engineers to detect the root causes of vibration, predict operational performance, and optimize designs before real-world implementation. The cloud-native platform allows for scalability and collaboration, making it easier for teams to run multiple simulations in parallel, test design modifications, and find effective solutions to vibration challenges.
References
- Sekhar, A. S., & Prabhu, B. S. (1995). Effects of coupling misalignment on vibrations of rotating machinery. Journal of Sound and Vibration, 185(4), 655-671. https://doi.org/10.1006/jsvi.1995.0407
- Elkihel, A., Abouelanouar, B., & Gziri, H. (2020). Rotating machines energy loss due to unbalance. In A. El Moussati, K. Kpalma, M. G. Belkasmi, M. Saber, & S. Guégan (Eds.), Advances in smart technologies applications and case studies (pp. 300–308). Springer. https://doi.org/10.1007/978-3-030-53187-4_34
- Zhou, P., Chen, S., He, Q., Wang, D., & Peng, Z. (2023). Rotating machinery fault-induced vibration signal modulation effects: A review with mechanisms, extraction methods and applications for diagnosis. Mechanical Systems and Signal Processing, 200, 110489. https://doi.org/10.1016/j.ymssp.2023.110489
- Ponci, L. P., Creci, G., & Menezes, J. C. (2021). Simplified procedure for vibration analysis and dynamic balancing in mechanical systems with beats frequency. Measurement, 174, 109056. https://doi.org/10.1016/j.measurement.2021.109056
- Gupta, R. K., & Singh, R. C. (2024). Optimizing high-speed rotating shaft vibration control: Experimental investigation of squeeze film dampers and a comparative analysis using Artificial Neural Networks (ANN) and Response Surface Methodology (RSM). Expert Systems with Applications, 249, 123800. https://doi.org/10.1016/j.eswa.2024.123800
- Shi, H. T., Abubakar, M., Bai, X. T., & Luo, Z. (2024). Vibration isolation methods in spacecraft: A review of current techniques. Advances in Space Research, 73(8), 3993-4023. https://doi.org/10.1016/j.asr.2024.01.020