Heating, Ventilation, and Air Conditioning (HVAC) equipment must be optimally designed to maximize the flow rate, whilst reducing pressure losses. This enables air to pass through the equipment with the least resistance and hence, less energy use. Finding a balance between fine-tuned airflow performance, manufacturing costs, durability, and weight is a complex task with many product variations in need of testing. This is where ventilation simulation and computational fluid dynamics (CFD) come into play. Engineers and designers can test different product design variations as a digital prototype using their preferred CAD models as the only input. SimScale is the first cloud-native engineering simulation software that gives users access to HPC through a simple web browser. For the first time, HVAC engineers are able to explore the full design space for HVAC product designs, not just at the component level but the spatial (room) level where the products are installed. This reduces cost and time by avoiding the trial-and-error characteristics typically seen in physical prototyping.
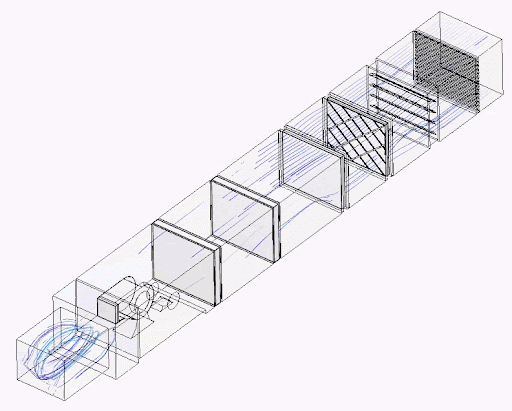
Common Problems in HVAC Design
The two most decisive factors in designing HVAC products (components) and systems (installed in buildings) that engineers struggle with are maintaining pressure drop at low levels across the systems and maintaining energy-efficient airflow. These two factors are critical in enhancing the overall performance of a well-performing system. Most commercial and industrial buildings as well as multi-family and large residential buildings have mechanical HVAC systems with air handling units (AHU), fans, louvres, dampers, air diffusers and filters, and other types of products integrated to give an overall system. These are all monitored and controlled with common building management systems (BMS). Each of these individual components would have been designed by engineers targeting a desired pressure-flow characteristic to achieve the required performance parameters.
Cloud-Native Simulation for Industrial Machinery Manufacturing
Our latest eBook explores how cloud-native simulation is transforming the challenges of industrial machinery manufacturing (including HVAC) into opportunities. Download it for free by clicking the button below.
Optimizing Air Handling Units Using CFD
Air handling units or air handlers work as a part of HVAC systems. They are used for circulating, purifying, conditioning, and renewing the indoor air in a building or premise. CFD simulation is used to design and verify the performance of AHUs.
Flow simulation
- Simulating the flow of air in an AHU, specifically through each individual component can give engineers an understanding as to the true installed performance of a system. The air will pass from a supply duct air intake, through various other components including control dampers, air filters, heating coils, mixing chamber, and others before it is distributed through the wider duct network. Running multiple simulations in parallel in the cloud for example, is a fast way to simulate swapping out alternative components to evaluate the performance of the system. It’s also a good way to study the impact of various environmental operating temperatures on airflow.
Pressure drop analysis
- Every component in an AHU acts as a resistor to the air that affects its pressure. This is most evident in the air passage through dampers, grills, louvres, but also the entire unit. Angle dependent pressure drops through dampers are very common and can be optimized through ideal fin angles or adding guiding vanes in the duct that cause the least amount of flow separation.
- Air filters act as porous media and their performance is directly linked to the pressure drop across them.
- CFD can calculate the pressure drop through each component as well as the entire system at various flow rates and temperatures.
Vibration and structural stress studies
- Blowers and fans can create substantial vibration and pass it on to other AHU components. Computing the minimum and maximum pressure values on the AHU frame and mapping them onto a structural analysis can give insights into the structural stresses and aero-acoustic interferences, both of which need to be minimized for safety reasons.
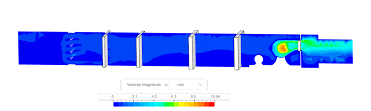
Ventilation Louvres
CFD is an invaluable resource for optimizing the pressure-flow characteristics of louvres. Common applications of CFD include:
- Determining the nominal discharge coefficient of louvres and grills to calculate the efficiency and its compliance with design standards.
- Investigating the airflow around the louvres to understand aerodynamics. This usually involves stagnation points, high velocity zones, flow separation, and the wake development and propagation. The results obtained can be critical in assessing where pressure loss occurs.
- Determining porosity factors, for example darcy and forchheimer coefficients, through porous modeling to develop pressure loss curves that can be used for comparative analyses and sizing.
This is where Smartlouvre Technology Ltd. took advantage of the CFD capabilities within SimScale by modeling and simulating their metal fabric product MicroLouvreTM. It is commonly attached to external windows and acts as natural ventilation and solar shading device.
With SimScale, Smartlouvre was able to evaluate the pressure-flow characteristics to determine a discharge coefficient (Cd). By setting up a digital wind tunnel at various wind speeds and angles the Cd value was found to be 0.39. This value can be used in building simulation and thermal modeling tools for simulating airflow in/out of buildings by architects and engineers who integrate MicroLouvre into their designs.
HVAC Units and Diffusers
The emergence of COVID-19 has increased the need for improved air quality and ventilation of indoor spaces. The demand for air mixing and air exchange rates in closed spaces like classrooms and office buildings, as per the design standards, has become more prominent with many building regulation authorities now asking for more quantitative evidence of good design. This is where SimScale can be used to design entire HVAC units and specialist diffuser grills. Engineers can finalize the best sizing, design, and placement of the diffusers depending on the functionality of the room and occupancy.
Below, a radial swirl diffuser is simulated using SimScale to show the efficacy of air mixing with this particular diffuser type:
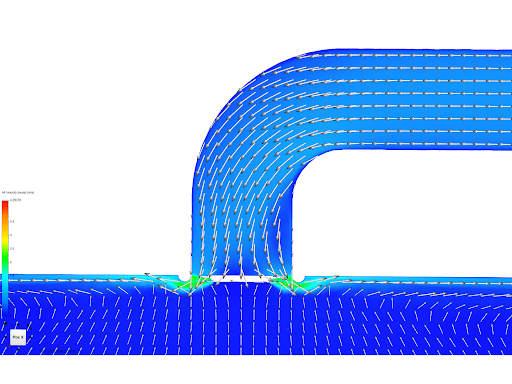
In another example, we can see a new generation of hybrid ventilation systems called the HVR Zero produced by Monodraught. This compact HVAC unit is capable of providing low-energy hybrid ventilation and cooling. Extensive CFD analysis with SimScale was used to design the unit, reduce pressure losses, and enhance airflow.
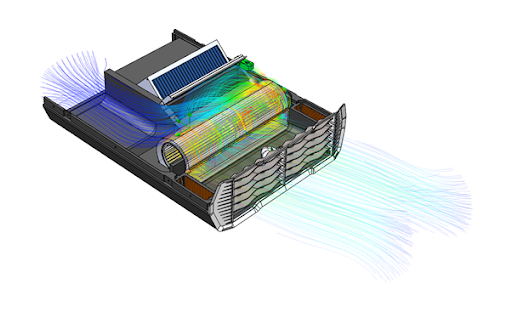
Using parallel simulation studies, Monodraught was able to reduce the fan power consumption by 50% by optimizing the air path inside the unit to reduce pressure drop and circulation regions. This can have a huge impact on the life of the unit when deployed in buildings.
Cloud-Native Ventilation Simulation
SimScale gives engineers and designers access to high-speed parallel computing empowering them to iterate faster in the design phase and tackle common problems in HVAC systems like AHUs, ventilation louvres, and diffusers. Engineers can harvest the parametric modeling capabilities in SimScale to use more ventilation simulation at the early design stages giving them the opportunity to fully explore the design space and focus on rapidly converging on a final design. This was previously done using costly physical prototypes that required testing with expensive test rigs; now, it can be done from a web browser with accuracy and speed.
Watch our on-demand demo to see how quickly users can set up a simulation to optimize the aerodynamic and pressure-flow characteristics of ventilation equipment and enhance overall product performance: