Truck design is an area where engineering simulation can be used extensively. Performed for virtually testing different vehicle components, as well as the entire truck aerodynamics, FEA and CFD simulations are essential in this industry.
Engineering Simulation in Automotive
The largest automotive manufacturers use engineering simulation software as a mandatory tool in their design processes. The designs of vehicles and their components are verified through engineering simulation and are optimized based on the results. This way, the number of physical prototypes required in the manufacturing workflow can be significantly reduced. The performance, efficiency, and cost reduction are among the benefits of using this powerful technology.
Whether talking about F1 cars, airplanes, family automobiles, buses, or trucks, their aerodynamics are always tested, as it can influence many different crucial aspects related to the vehicle. Computational fluid dynamics (CFD) play an important role in truck aerodynamics, allowing engineers to investigate the airflow and better understand how air moves around the vehicle. Creating an aerodynamic vehicle is essential to ensure enhanced performance, increased speed, noise reduction, and fuel consumption.
CFD for Truck Design
Each component of the truck design process offers opportunities to reduce aerodynamic drag. Any supplementary component added or modified has an impact on the performance of other components.
There are different ways to optimize a truck design. Some experts suggest that the greatest aerodynamic drag reduction comes from using devices in three main areas: gap, underbody, and rear. Improving truck aerodynamics in these three points can generate the greatest fuel savings for a large majority of fleets [1].
A better cabin design or simple accessories like trailer fairings can improve a truck’s performance by:
- Improving truck stability and rollover
- Reducing splash and spray
- Better weight distribution on the truck chassis
- Reducing fuel consumption
- Improving long-distance behavior
- Reducing driver fatigue
Why is Optimization in Truck Aerodynamics So Important?
17 North American truck fleets, operating more than 62,000 tractors and 217,000 trailers, saw a 3% increase in fuel economy in 2015. This represents a cumulative saving of $501 million on fuel when compared to the 2015 national average fuel spend of 1.7 million over-the-road class 8 trucks.
According to the Annual Fleet Fuel Study released by the North American Council for Freight Efficiency (NACFE), they eliminated operational deficiencies by purchasing a variety of fuel efficiency technologies. As a result, fleet-wide fuel consumption in miles per gallon increased from 6.87 mpg to 7.06 mpg in 2015, the largest margin of improvement since 2012 [2].
In truck design, the testing process can go through several of these methods:
- Engineering simulation, especially computational fluid dynamics and finite element analysis
- Wind tunnel testing – for tractor/trailer vehicles in a wind tunnel, where environmental conditions can be controlled
- Track testing – a large variety of test protocols are used on a test track
- On-road testing – involve physical testing with special devices installed on a truck, for long-distance driving in different roads conditions
- Fleet Composite Evaluation – based on different fleet recording for total miles driven, freight carried, and fuel purchased
Engineering simulation is usually used in combination with physical testing, but the main benefit is that it allows the engineers to test their design early, and make several iterations until an optimized CAD design is created. Once they have a final design, moving towards physical prototyping, with a significant amount of cost-saving, is the next step.
Still, until recently engineering simulation was not an easy approach to testing either. On-premises traditional simulation software starts from $40k, lacking flexibility or collaboration options. They also require advanced technical expertise to be efficiently used. Four years ago, however, the world’s first 100% cloud-based simulation platform—SimScale—was launched, breaking these barriers.
Completely web-based, SimScale doesn’t need investment in hardware and works from any PC or laptop. And with hundreds of learning resources available, becoming an expert in engineering simulation is much easier.
SimScale’s CEO David Heiny tests the capabilities of the platform to solve a real-life engineering problem. Fill in the form and watch this free webinar to learn more!
Ready-to-Use Truck Design Simulation Templates
The SimScale Public Projects library is a place where you can find thousands of simulations performed by SimScale engineers or community users. These projects can be copied and modified to help you set up your own CFD, FEA, or thermal analysis in only a few minutes. Here is a selection of three truck aerodynamics simulations:
Simple Truck Aerodynamics Analysis
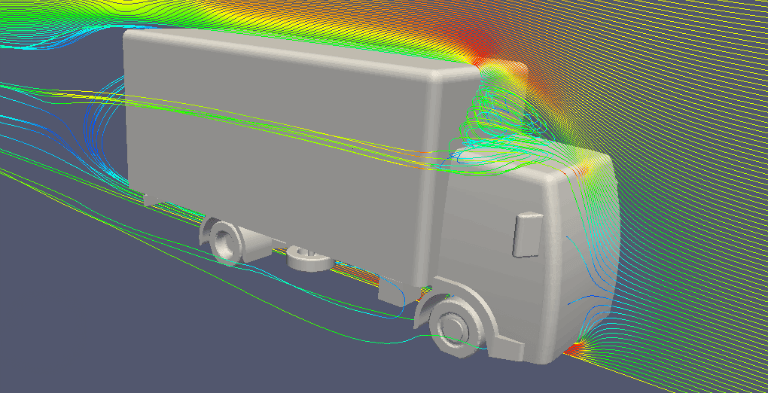
This project is a CFD simulation of airflow around a truck moving at 10m/s & 20m/s.
The k-omega SST model was used for this analysis, and the values of “k” and “omega” were calculated using the standard approach based on the velocity and turbulent intensity.
The simulation results include a different screenshot with the stream tracer around the truck for different speeds.
Aerodynamics Simulation of a Semi-Trailer Truck
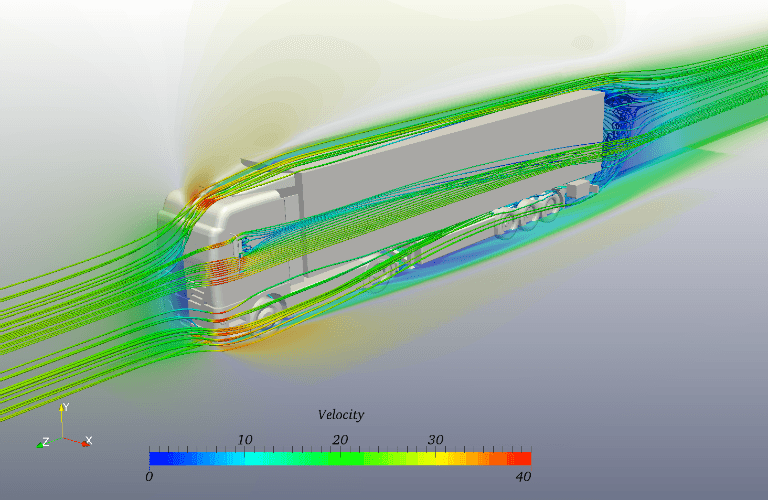
This project simulates the external aerodynamics of a semi-trailer truck. A steady state turbulent flow analysis with the k-omega SST model was used for the study of turbulence distribution.
To reduce computational efforts, we could also take symmetry conditions along the directional flow. The inlet velocity is 28 m/s with a pressure boundary condition at the outlet.
The simulation investigates the mean flow field around the vehicle. The results processed with ParaView provide insights into how the flow behaves around the vehicle body. The figures also show a high-pressure distribution on the front face and a large flow recirculation region behind the trailer.
Aerodynamics Simulation of a Moving Truck
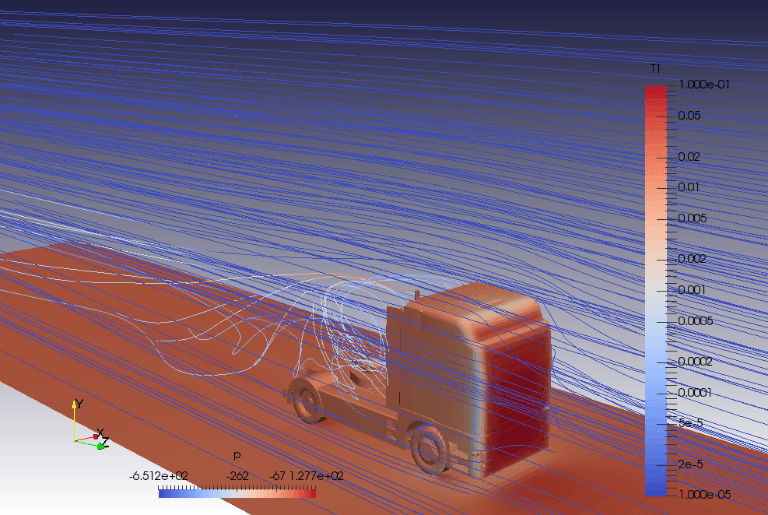
The project represents a mix between a CFD and scalar moving simulation for a driving truck with the exhaust gases coming out its exhaust pipe.
Due to the asymmetry created, the user considered two scenarios for the geometry adoption: (1) no trailer (2) asymmetric model for the exhaust pipe positioning.
Hence the simulation conditions adopted are 15 m/s speed for the truck moving and 3 m/s for the exhaust gases coming out the pipe.
If you’d like to learn more about the SimScale cloud-based simulation platform and its features, download this overview.
References
- Trailer Aerodynamics, Truckingefficiency.org
- 2016 Annual Fleet Fuel Study, Report of a study conducted by the North American Council for Freight Efficiency (NACFE), IoT Now.com, August 2016