The electronics sector includes general electronics, electric utilities, and consumer electronics, with the latter category driving most of the growth. Characterized by constant innovations and a need to accelerate time to market, the global electronics industry generated US$997 billion in revenues worldwide in 2018 [1] and is predicted to grow at a compound annual growth rate (CAGR) of 5.6% until 2024 [2].
New models of smartphones, computers, laptops, tablets, wearables, game consoles, VR & AR devices, speakers and headphones, and TV sets are released at full speed, stiff competition putting high pressure on manufacturers. And it’s not giving any signs of slowing down; the rising demand for smartphones, artificial intelligence, and voice recognition technology will perpetuate and enhance this growth, demanding, at the same time, lower prices and shorter time to market for electronics companies to stay competitive.
While consumer electronics might take the lion’s share, general electronics, telecommunications, and electric systems are also experiencing significant growth, partly supported by the emergence of the Internet of Things (IoT), cloud computing, data mining, and smart cities.
All of this growth in the electronics industry requires performant R&D departments, efficient design processes, and large budgets to develop competitive products, at competitive prices, in a highly competitive industry. And still, none of that matters if it doesn’t also include a competitive time to market (TTM).
So what do electronics companies need to know about optimizing their development process in such a dynamic market? Here are 7 ways to accelerate time to market and boost efficiency.
1. Identify the Top Features for Product Differentiation Within the Electronics Industry
You might be keen on accelerating time to market as much as possible, but the first step in your product planning stage is determining the five core features of your product that will differentiate it from the competition but also your previously released products. This should be done based on research studies that analyze consumers’ needs and preferences. If you think you have your product’s highest added-value features that will revolutionize the electronics industry, organize focus groups and validate your design.
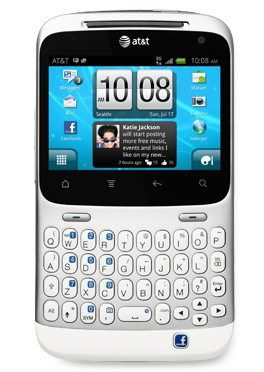
The history of the electronics industry is full of fails; remember HTC’s ChaCha and Salsa phones that had a Facebook button integrated? In hindsight, it could have come in handy, but the world was simply not ready for it.
2. Document the Product Development Process
Having a documented product development process for electronic components or products is essential in ensuring that your team works as efficiently as possible and is informed at all times about the project’s status.
Moreover, without thoroughly defined steps, any estimation of the time for project completion will be highly inaccurate. Process mapping enables electronics companies to allocate resources properly, set deadlines, and have time management in check through schedules.
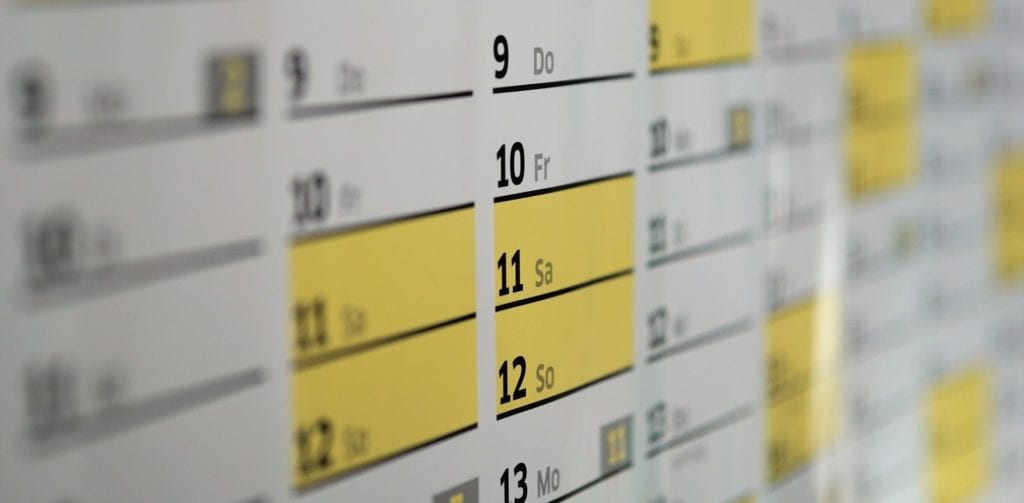
Using dedicated project management software will enable team leaders to assign tasks and keep track of progress. This will prevent inefficiencies caused by miscommunication, delays in knowledge sharing, lack of ownership, or making uninformed decisions. While having a thought-through plan is crucial, documenting the changes, feedback, and extra steps that emerge is also important, as the process evolves with each product development cycle and learning might be derived each time.
3. Clearly Define Roles in the Team
Firstly, in business, democracies don’t work. Each project needs a responsible person for leading it, from beginning to end. Sharing ideas and know-how within the team is essential, but in the end, you’ll need one person to take the final decisions and ensure project delivery.
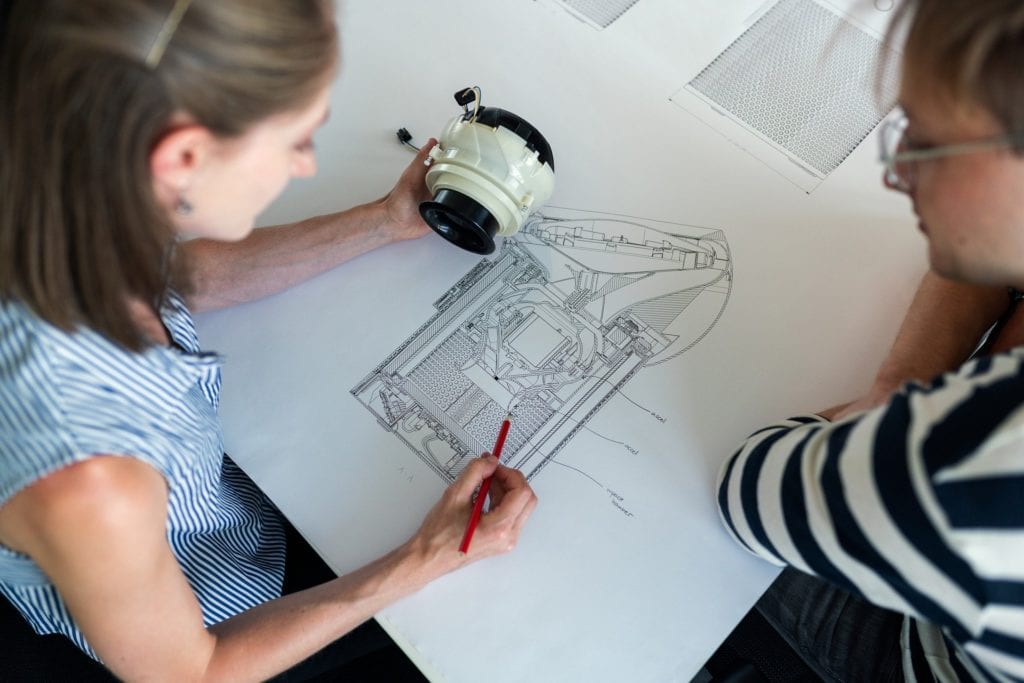
Secondly, each team member needs a defined role in the organizational structure. When work ownership is ambiguous and responsibilities are unclear within a team, issues can remain unsolved and mistakes are more prone to occur, causing delays on rework later in the product development process.
4. Institutionalize Project-Related Learning
Once you document your product development process, engineers involved will identify many learnings, product knowledge, and improvement opportunities, especially in the virtual testing and physical prototyping phases.
In the electronics industry, with teams dedicated to meeting aggressive deadlines, documenting and distributing such lessons is considered a low priority when in fact, it is one of the most essential steps in reducing time to market at an organizational level. Maybe the singular project will lose some time creating a repository, but documenting project-related learning will prevent future mistakes in dozens of other projects, avoiding the situation of different teams reaching the same conclusions over and over again, trapped in a loop of lessons never communicated across the company.
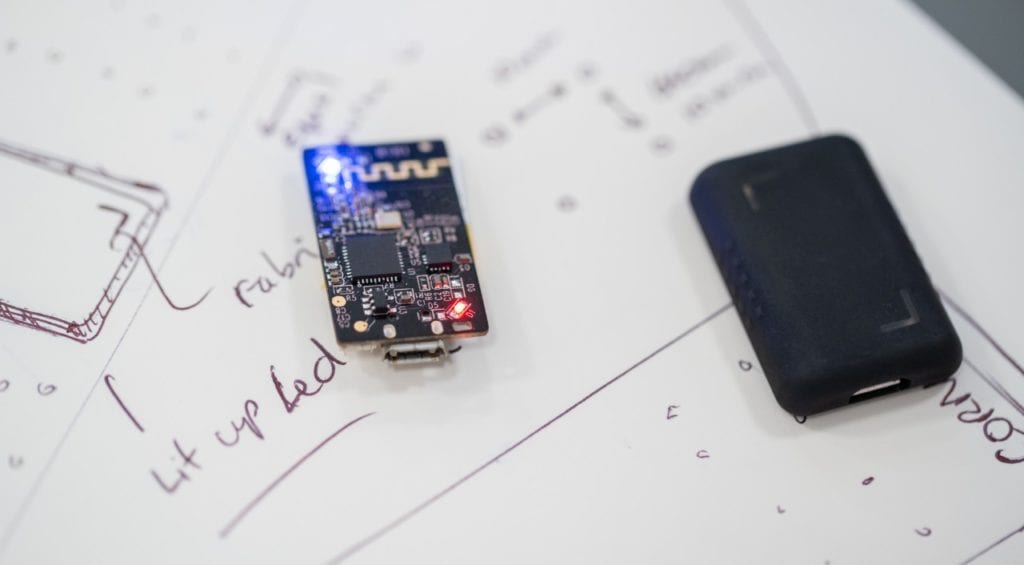
Yet, not only documenting is important, but also having a centralized database for files and materials that all team members involved can access. Storing anything relevant on local computers should be discouraged.
5. Avoid Design Rework
In the race of bringing a product to market, the planning of a project can have unrealistic deadlines, putting a lot of pressure on the team members. This often results in shortening the testing phase, with engineers creating too few (or sometimes only one) physical prototypes and neglecting to apply improvement changes or even failing to predict problems under different scenarios. Often this leads to design rework once the issues are uncovered, creating overload for the engineer closer to the launch date.
Other times, companies in the electronics industry send the design to manufacturing and release it even though it is not as mature as it should be or didn’t undergo enough testing. And that is a mistake that even the big players know well; I’m sure that Samsung knows a thing or two about this; we all remember the long thread of pictures in 2016 with Galaxy Note 7 catching fire or even exploding that forced airlines to ban the devices on their planes.
Actually, what happened with the tablet was that the battery was overheating in some circumstances with not enough room in its casing to expand. This immense business failure and brand reputation damage could have been avoided with a more thorough testing process, thermal management studies in particular.
Failure to adhere to operational temperature limits can result in component overheating, system failure, and—by far the worst of all—life-threatening risks. I still remember meeting a joyful boy in a children’s hospital 10 years ago who had burn scars all over his hands. When I asked him what happened to him, he replied “I was watching TV at home one day and well… it exploded”.
It is not to say that these electronics companies didn’t perform testing. But analyzing hundreds or thousands of scenarios for multiple design versions with physical prototyping is simply not feasible. This is why engineering simulation (CAE) software is used in most electronics design processes, to complement physical testing with virtual analysis. CAE is meant to be employed early in the design process, in order to predict potential failures and make improvements from the start based on the results of the numerical analyses. With cloud-based CAE in particular, all of these scenarios and multiple design versions can be investigated in parallel, supporting a high-paced, iterative design process.
Case Study: Preventing Thermal Damage in Electronics
Let’s take the example of this engineering project directed by David McCall, Senior Mechanical Engineer at QRC Technologies, whose goal was to design enclosures for RF testing equipment that measure cellular band signals and optimize heat dissipation.
When relying on passive cooling, RF testing tools overheat—reaching up to 50 °C (122 °F). This became a problem to address for QRC’s engineers when they relied on rule-of-thumb engineering to cool hard drives. While the CPU was operating within limits, using only thermal pads between the hard drives and the boards proved to be insufficient. The controller chip was hitting the physical limit and was shutting down as a defensive strategy to prevent damage. In the pursuit of finding a cooling system suitable for these specific conditions, tested four design iterations with computational fluid dynamics (CFD) analysis, reaching a final version within a week.
For the casing, the engineers used heat sinks with copper slugs and graphite to give hard drives a heat path out to the enclosure. The materials were chosen due to their high thermal conductivity, especially for thinner pieces, enabling radiation. The aim was to ensure heat could travel to the outer casing easier than it could travel through the air, and the enclosure would release heat outside of the device.

The final task was to ensure that the casing had sufficient surface area and an extra fan blowing onto it or get a case to radiate the heat out into the environment. Before creating any physical prototypes, thermal simulations were performed to see if the chip would overheat or even break. The results helped optimize heat dissipation and reach a final design.
QRC’s engineers went with the SimScale cloud-based CAE platform because it did not lock up resources locally. Another reason was cost; as a SaaS solution, the platform only has a yearly subscription fee and does not require any special hardware or software licenses.
“It was also a lot more cost-effective as opposed to getting a seat and having it sit there for three to four months. We are a small company and might use a simulation for two solid weeks every six months—you can’t borrow that from a friend”, said David McCall.
In the end, QRC Technologies saved 4-6 additional weeks by integrating cloud-based simulation in their design process, which contributed as well to a shorter time to market. This project was discussed in more detail in this article by Engineering.com.
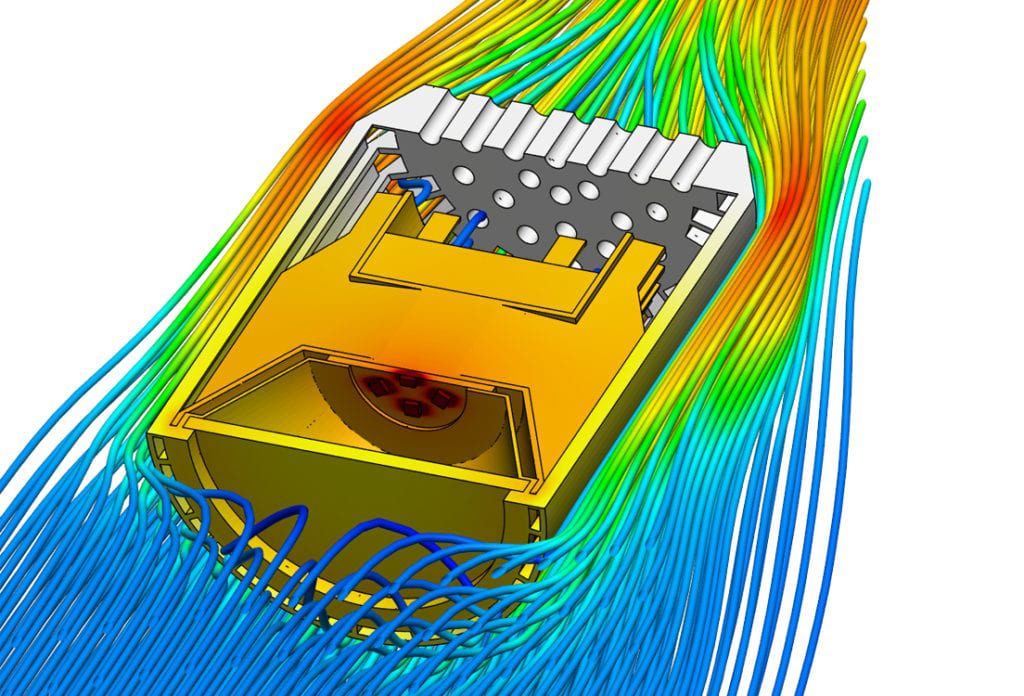
To learn more about how to tackle overheating in electronics and test products early in the development process with thermal simulation, refer to the article Electronics Cooling Project: LED Spotlight.
6. Onboard New Engineers Before Assigning Them a Project
In most companies that employ engineers—and electronics is no exception—new employees receive little onboarding. They are rather involved in a project from week one, leaving virtually no time to go through training material, understand the organization, and get familiarized with the project’s wider context. No matter how much experience one has in their field, in order to make the best use of their skills, employees need to first understand the company, industry, and organizational know-how (including the lessons learned from previous projects mentioned earlier).

7. Enable Collaboration to Accelerate Time to Market
In any product development process, leadership, design engineers, project managers, contractors, and manufacturing responsibles need to communicate on an ongoing basis. As obvious as the need is, however, in practice it is a serious challenge; especially with globally dispersed development teams. And this is often the case for large electronics companies that have the design team in one country and manufacturing possibly across an ocean. Furthermore, in a world that becomes more digitized by the day and remote workplaces are emerging, collaboration becomes top priority. Any failure in ensuring it can hinder progress and prolong time to market.
In the product development process, it is important to encourage collaboration within the design team as well as among teams to enable wide information dissemination. Constant communication is key, don’t wait for meetings, keep the ball rolling. Here are a few things to consider:
- Adopt an efficient communication model with tools that promote collaboration. Your task management systems (e.g., Asana, Jira, Trello, Todoist, Samepage, etc. need to be integrated). You will also need to make use of communication platforms (e.g., Slack, email).
- Consider cloud-based solutions for engineering software, as they offer collaboration features that allow team members to work together on the same projects. Onshape, for example, allows users to create computer-aided design (CAD) models online, end-to-end. The same benefits are granted for engineering simulation technology (CAE) through SimScale. Actually, SimScale has recently released enhanced collaboration features and a multi-user licensing package to support design and engineering teams with multiple people who use simulation. With these features made possible through cloud computing, teams can save time, organize tasks, scale their simulation expertise, and have broader visibility and control within their projects. You can read more in this article: SimScale Announces Cloud-Based Collaboration Features.
- Keep track of the steps and involve the team in giving status updates on a regular basis.
- Ensure that feedback loops take place often, not only from the project manager but also among peers.
- Remember that collaboration and teamwork are essential to accelerate time to market, but you can’t decide as a team; you’ll still need a single, empowered decision-maker with ownership over key aspects of the project.
Conclusion
Getting to market faster than the competition enables electronics companies to capture market share. Shorter time to market should not mean, however, quality compromise; there are no shortcuts, just better process optimization. Each of the tips described in this article should prove to be helpful in keeping this balance between accelerating time to market and delivering high quality, innovative electronics products.
Keep in mind that every time waste will cause a delay and each improvement will be a gain. In the end, when time wastes are reduced to a minimum and all steps for higher efficiency are taken, electronics companies will be able to accelerate time to market and get the desired results.