The electronics industry is one of the most rapidly growing industries in the world, but it is faced with increasingly stringent thermal design requirements, creating a demand for innovative and sustainable electronics cooling solutions. The growing popularity of high-powered electronics imposes various constraints on designers, particularly in relation to temperature, size, weight, widely varying operating conditions, and the multiple design scenarios that they must address within their tight schedules.
Thermal integrity is one of the most important considerations for electronic packaging that affects its product lifecycle. The thermal impact on the enclosure is a key factor for material selection, as well as informing cooling and form factor decisions that eventually determine the weight, size, and cost of the final design. Therefore, it is vital that designers determine the heat signatures of their systems.
Download our ‘Electronics Cooling Guide’ now for a complete overview!
Why is Simulation Important?
The stage when you begin to explore the design space and define your product concept is when the most impactful design decisions are made. Simulation is one of the tools that play a fundamental role in those early product development stages—for the final product, this can mean lower production costs, more efficient energy consumption, lower failure risk, and more.
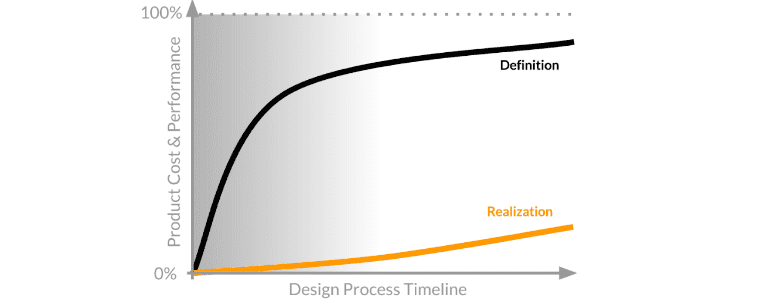
So why aren’t all designers using simulation yet?
-
Accessibility: Traditional software needs to be installed locally on expensive high-performing computers, the majority of which remain idle most of the time. With SimScale, all computations are cloud-based—all that is needed is a web browser.
-
Operating costs: Standard commercial simulation software packages are notoriously expensive. With SimScale, there is an option to start simulating right away with a free Community Plan.
-
Know-how: Most modern tools are designed for experts and experienced simulation engineers. To bridge that knowledge gap, SimScale offers a large public projects library, free training, and live support chat.
Sign up & check out our SimScale blog for much more!
The Engineering Problem: Sustainable Electronics Cooling Solution
Developing sustainable thermal management solutions is one of the main challenges faces by electronics designers. Overreliance on experience or intuition and physical trial-and-error testing to predict the cooling of complex electronic systems is expensive, time-consuming, and highly unreliable. While physical prototyping cannot (and should not) be eliminated entirely, simulation can be an effective tool to validate your design while saving time and money in the process.
Computational fluid dynamics (CFD) simulation, in particular, has become a routine design tool for accurately predicting thermal performance in electronics cooling cases. It can, for example, be used to map temperature distribution on a mounting surface of a printed circuit board with heat-generating components and highlight areas where the junction temperature of the semiconductor components could be above the maximum safe temperature specified by the manufacturer.
Project Overview
For the purpose of this study, we used the following simulation project from the SimScale library: Electronics Optimization with CFD.
The aim of this project is to investigate the performance of air-cooling performance of an electronic cabinet, including a heat source by forced convection. The steady-state 3D viscous flow problem involving coupled heat transfer between the solid-fluid medium is solved with the help of the conjugate heat transfer solver in SimScale.
This enclosure has the following overall dimensions: W x L x H = 1.5m by 2m by 0.5m.
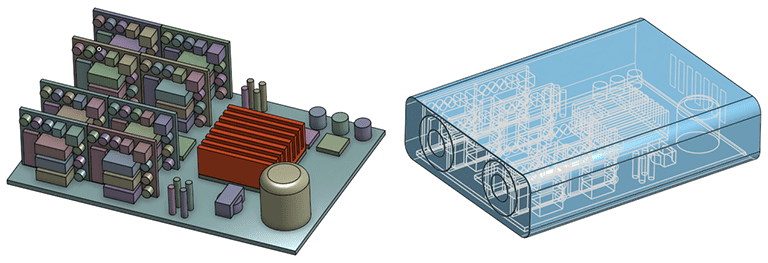
Mesh
To solve this problem, a hex-dominant parametric mesh was created. A mesh for a conjugate heat transfer simulation requires all the solids to be meshed as separate regions. Thus, a multi-region mesh is created with interfaces automatically detected between the different regions.
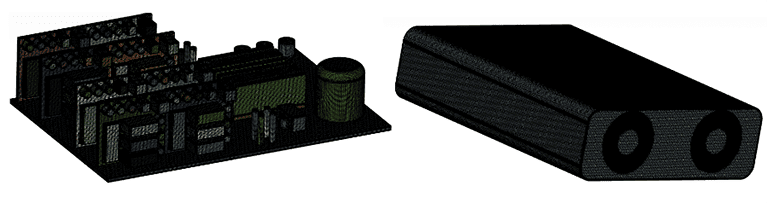
Simulation: Thermal Design Validation
The CFD simulations presented here have utilized 3D conjugate heat transfer with forced external air convection and solid conduction. The following parameters were used in the simulation setup:

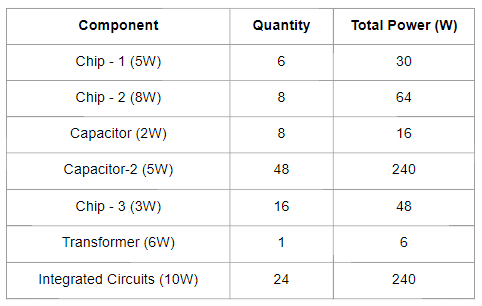
Simulation Results
The results for temperature distribution, flow vectors, and streamlines in our simulations are illustrated below.
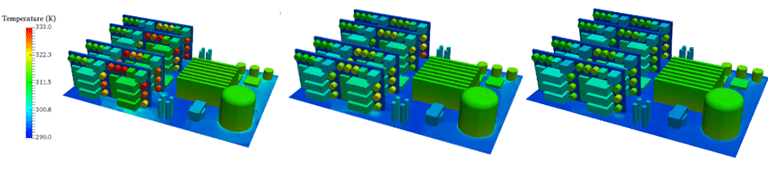



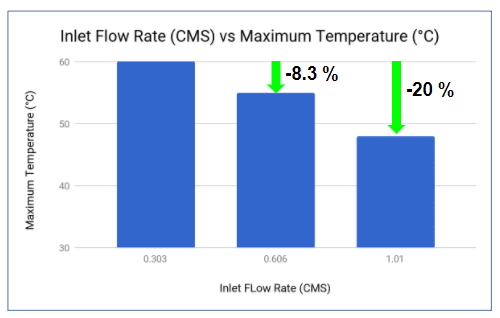
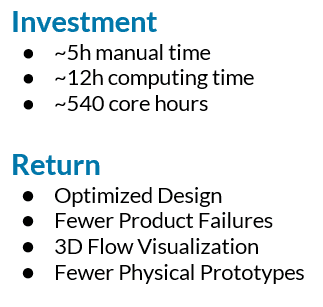
This project demonstrates how, in a matter of hours, we can optimize the fan inlet flow rate for an electronics package, resulting in reduced maximum temperature inside the cabinet.
Since the expected life of any component is affected by the temperature at which they operate (in fact, reducing the temperature by 10 degrees can double its expected life!), managing heat becomes a critical factor in the design of high-power electronics.
Conclusion
This is just one example of how CFD tools can help engineers predict the performance of their thermal design and optimize it accordingly. The SimScale Public Projects Library has a wide selection of free simulation templates covering various aspects of thermal design, electronics cooling, heatsink design, and more.
If you want to learn about all of our thermal modeling software solutions, check out our thermal analysis hub.
And don’t forget to watch the webinar to learn more about the application of engineering simulation for electronics cooling and see a live demonstration of the platform by SimScale’s CEO David Heiny! Just click on the button below, fill in the form, and enjoy!
References
- https://www.electronics-cooling.com/category/cfd-software/
- https://www.researchgate.net/publication/317131278_Numerical_investigation_for_heat_transfer_enhancement_using_nanofluids_over_ribbed_confined_one-end_closed_flat-plate
- https://www.researchgate.net/publication/267647723_Analysis_of_Liquid-Cooled_Heat_Sink_Used_for_Power_Electronics_Cooling