Have you ever seen footage of a bridge swaying dangerously in the wind or felt a building vibrating unexpectedly during an earthquake? These are classic examples of structural resonance. If not properly addressed, this phenomenon can cause severe damage to structures, resulting in catastrophic failures and significant financial losses.
Structural resonance occurs when a structure’s natural frequency aligns with external vibration forces, leading to potentially dangerous oscillations. To prevent such occurrences, resonance mitigation is essential. This involves designing and implementing strategies to minimize the impact of resonant frequencies on structures. One of the most effective ways to achieve resonance mitigation is through simulation and analysis early in the design process.
By using advanced cloud-native simulation tools like SimScale, engineers can identify potential resonance issues during the design phase and make necessary adjustments before physical testing. In this article, we will delve into the causes of structural resonance, its effects on various structures, and how engineering simulation can be utilized to mitigate these risks, ensuring safer and more reliable designs.
What Is Structural Resonance?
Resonance takes place when an object or system is subjected to oscillations at its natural frequency, causing it to vibrate with a larger amplitude. In design terms, structural resonance occurs when the frequency of external forces (like wind, machinery, or seismic activity) aligns with the structure’s natural frequency, resulting in amplified oscillations and vibrations.
Every structure has a natural frequency—a frequency at which it naturally vibrates. When external forces match this frequency, resonance occurs. This can lead to significant amplification of the vibrations, potentially causing damage or failure.
For a detailed description of natural frequency, check out our dedicated article: What is Natural Frequency?
Case Study: Electric Vehicle (EV) Battery Module
Consider an electric vehicle (EV) battery module. Essential yet classified as “dangerous goods,” batteries are highly sensitive to conditions such as shocks and vibrations. Nearly all lithium batteries must comply with the UN 38.3 international transportation standard, which includes rigorous vibration tests to ensure safety during transportation.
Using SimScale, engineers can simulate these conditions and perform structural analyses to predict how their battery designs will respond. By identifying potential resonance frequencies and evaluating stresses and deformations, designers can make necessary adjustments to improve the battery’s performance and safety before physical testing.
Mathematical Formulation of Structural Resonance
Structural resonance can be described using the principles of dynamics and vibrations. The equation of motion for a damped harmonic oscillator is:
Where:
is the mass of the structure, is the damping coefficient, is the stiffness of the structure, is the displacement, is the velocity, is the acceleration, is the external force as a function of time.
Natural Frequency and Damping
The natural frequency (
The damping ratio (
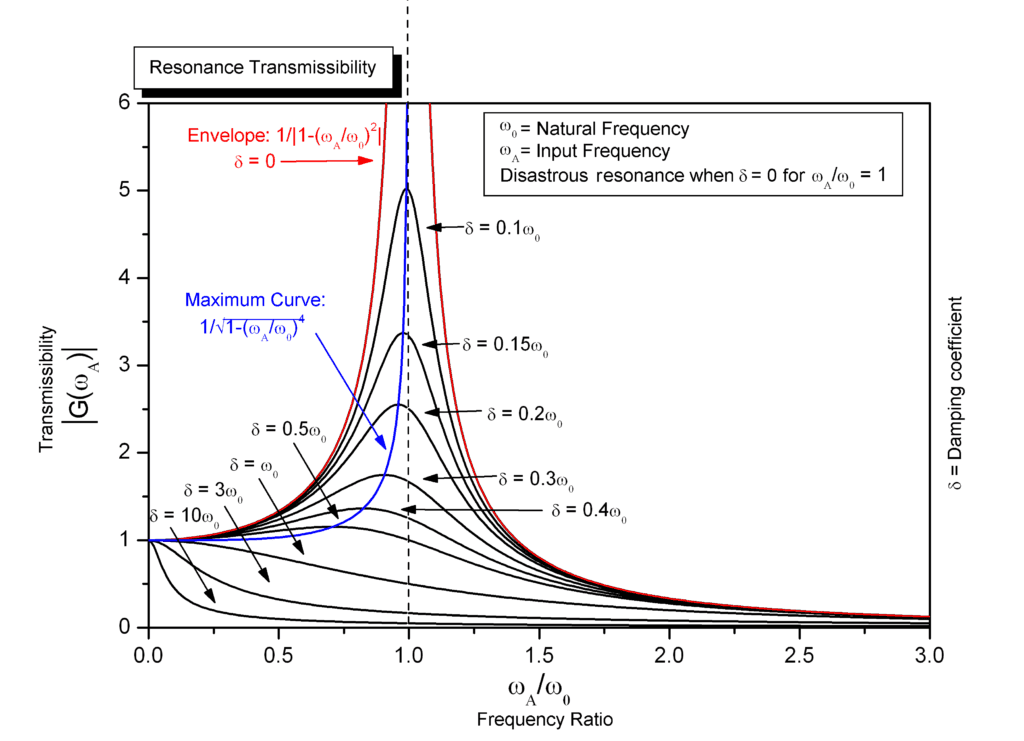
Response to External Forces
When an external periodic force (
Understanding these mathematical formulations helps engineers predict how structures will respond to different forces and design them to avoid resonant frequencies.
Cause of Structural Resonance
Structural resonance results in damage because it amplifies oscillations when the structure’s natural frequency matches the frequency of external vibrations. This can be caused by various external forces, including:
- Machinery: Equipment and machinery operating at specific frequencies can transfer vibrations to surrounding structures.
- Wind: Strong winds can induce vibrations in tall structures like skyscrapers and bridges.
- Seismic Activity: Earthquakes can cause ground movements that match the natural frequencies of buildings and other structures.
When a structure enters resonance, the energy from the external vibrations is absorbed and accumulated by the structure, causing it to oscillate with increasing amplitude. This amplification happens because the input energy from the external force continually adds to the structure’s vibration energy at its natural frequency. As the amplitude of the oscillations increases, so do the stresses and strains within the structural components.
This happens due to the structure’s inability to effectively dissipate or dampen the absorbed energy. Often, this is due to insufficient analysis or simulation of resonance during the design phase, leading to a lack of certainty in ensuring a robust design. Proper damping mechanisms must be incorporated into the design to mitigate these effects based on simulation results.
Effects of Structural Resonance
Structural resonance can have several detrimental effects on structures, such as:
Reduced Performance
When a structure experiences resonance, its performance can be significantly compromised. For example, machinery or equipment operating at resonant frequencies may not function as intended, leading to inefficiencies. In the case of rotating machinery, resonance can cause imbalances and misalignments, reducing the precision and effectiveness of the machine.
Increased Vibrations
Resonance leads to amplified oscillations, causing the structure to vibrate more intensely than under normal conditions. These increased vibrations can be felt throughout the structure, affecting the primary components and any connected systems. In machinery, excessive vibrations can cause premature wear and tear on components, leading to a shorter lifespan and increased downtime.
This phenomenon is part of what engineers refer to as Noise, Vibration, and Harshness (NVH) analysis. NVH analysis is the study of how noise and vibrations affect the comfort, performance, and durability of mechanical systems and structures. It involves measuring and analyzing the levels of sound and vibration produced by various components to identify sources of unwanted noise and vibrations. By addressing NVH issues, engineers can improve the overall quality and reliability of their designs, ensuring a quieter, smoother, and more durable performance.
Noise
Resonance in structural dynamics often results in increased noise levels. The vibrations can cause various parts of the structure to emit sound, leading to a noisy environment. This is not only a nuisance but can also pose health risks to individuals exposed to high noise levels over extended periods. In industrial settings, noise from resonance can interfere with communication and increase the risk of accidents.
Structural Fatigue
Constant exposure to resonant vibrations can lead to structural fatigue. This occurs when repeated cyclic loading causes the material to weaken over time. Even if the vibrations are not severe enough to cause immediate damage, the cumulative effect can lead to the development of microcracks and eventual failure.
Component Failure
Amplified vibrations from resonance can cause individual components within a structure to fail. Fasteners may loosen, welds may crack, and joints may weaken. In electrical systems, connectors and circuits can become damaged due to the mechanical stresses induced by vibrations. Component failure can lead to system-wide breakdowns, requiring significant repairs and replacements.
Higher Maintenance Costs
All the issues caused by structural resonance—reduced performance, increased vibrations, noise structural fatigue, and component failure—translate into higher maintenance costs. Frequent repairs and replacements are necessary to address the damage caused by resonance. Regular inspections and monitoring are also required to identify and mitigate resonance issues before they lead to significant failures. These maintenance activities can be costly and time-consuming, affecting the overall cost-effectiveness of the structure.
Vibration Analysis for Structural Resonance
Vibration analysis is a critical process for detecting, monitoring, and preventing structural resonance in machinery and structures. Vibration analysis examines how structures respond to dynamic forces. By analyzing vibration signal patterns, engineers can identify irregularities that may indicate resonance.
Here’s how vibration analysis helps detect structural resonance:
- Identifying Natural Frequencies: Every structure has natural frequencies at which it tends to vibrate. Vibration analysis helps pinpoint these frequencies, allowing engineers to predict and avoid resonance conditions.
- Understanding Mode Shapes: Mode shapes describe how a structure deforms at specific frequencies. Analyzing mode shapes helps identify areas that are prone to resonance.
- Evaluating Damping Characteristics: Effective damping dissipates vibration energy. Vibration analysis assesses how well a structure can dampen vibrations, which is crucial for mitigating resonance.
- Assessing Stress and Displacement: This analysis calculates stress and displacement under dynamic loads, revealing potential structural weaknesses and failure points.
- Visualizing Eigenmodes: Eigenmodes represent natural vibration modes. By visualizing them, engineers can understand how a structure behaves under dynamic conditions.
Vibration analysis simulation differs from static analysis by focusing on the structure’s response to dynamic and varying forces. In contrast, static analysis evaluates the structure under constant, steady loads and does not account for dynamic effects, making it less effective for identifying potential resonance issues.
Using Engineering Simulation to Mitigate Structural Resonance
SimScale is a powerful tool for engineers, reinforcing structural mechanics simulation capabilities with cloud computing. It enables running parallel simulations, which significantly reduces analysis time. Engineers can access FEA simulations anytime, anywhere through a web browser, avoiding manual upgrades, installations, and associated fees.
SimScale allows for detailed analysis of vibration patterns to identify irregularities in mechanical systems. With its FEA modal analysis powered by the Code_Aster solver, SimScale computes a structure’s natural frequencies and corresponding oscillation mode shapes.
Case Study: TechSAT Aerospace Engineering
TechSAT, an aerospace engineering firm, used SimScale’s simulation tools to evaluate an airborne electronics housing unit’s response to vibrations, which is crucial for compliance with RTCA DO-160G standards.
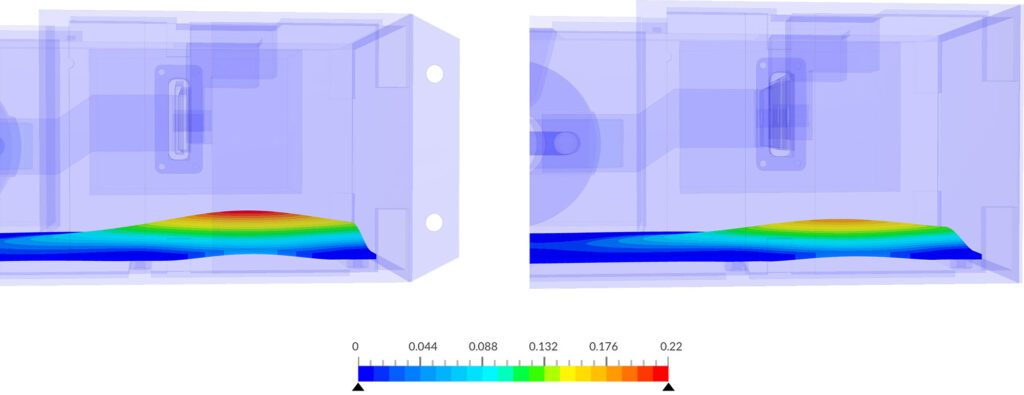
They identified natural frequencies and mode shapes by performing frequency and harmonic analyses, optimizing the design to minimize PCB deflection and ensure structural integrity.
Comparing bolted flanges and full rack support, they found that the latter reduced deflection by 18%. These simulations allowed TechSAT to refine its design early, reduce physical prototyping, and expedite product development, leading to safer, more reliable components.
“After evaluating several tools, we found SimScale to be fast and easy to use as well as being cheaper compared to others with the same capabilities. We saved over €15K in licensing and hardware costs by opting for the fully cloud-native solution by SimScale.”
Mar Sanchez, Mechanical Engineer at TechSAT
Use SimScale for Resonance Mitigation
Ready to make your designs safer and more reliable? With SimScale, you can easily perform advanced vibration analyses right in your web browser.
Save time, reduce costs, and improve your designs with our powerful cloud-based simulation tools.
Main Contributor: Muhammad Faizan Khan