SOLIDWORKS is renowned for its powerful 3D modeling and CAD capabilities. However, to truly validate and optimize designs, engineers often require complex engineering simulations like Finite Element Analysis (FEA) and Computational Fluid Dynamics (CFD), which, more often than not, require high computing power.
This is where SimScale steps in. SimScale is a cloud-native simulation platform that seamlessly integrates with SOLIDWORKS, offering a rich array of advanced engineering simulation capabilities and computational power in the cloud. Leveraging the advantages of cloud computing, SimScale not only ensures a seamless CAD-import workflow for SOLIDWORKS users but also enables access from anywhere directly in their web browsers and allows for parallel simulations, empowering users to run multiple simulations at the same time. But that’s not all. There is a secret sauce, a key advantage all engineers and designers on SOLIDWORKS would benefit from massively.
In this article, we will look through the SOLIDWORKS Simulation and Flow Simulation tools, and then we will explore the seamless and proven CAD-import workflow between SOLIDWORKS and SimScale, highlighting its secret sauce in how it allows users to easily simulate native SOLIDWORKS parts and assemblies.
SOLIDWORKS Simulation and Flow Simulation Tools
SOLIDWORKS provides two robust, in-house simulation tools, SOLIDWORKS Simulation for FEA and SOLIDWORKS Flow Simulation for CFD. These integrated tools help engineers perform structural, thermal, and fluid flow analyses in their familiar SOLIDWORKS environment.
SOLIDWORKS Simulation
Engineers and designers can make use of SOLIDWORKS Simulation to perform structural analysis and predict how a design would behave under particular conditions. Some of its highlights are:
- SOLIDWORKS FEA capabilities for structural analysis
- Linear, non-linear static, and non-linear dynamic capabilities
- Easy-to-use interface for setting up simulations
- Easy integration with CAD models
SOLIDWORKS Flow Simulation
SOLIDWORKS Flow Simulation extends the simulation capabilities into the realm of CFD. With this tool, engineers can analyze the behavior of fluids (liquids and gases) within or around their designs. Some of its highlights include:
- SOLIDWORKS CFD capabilities that utilize the Finite Volume Method (FVM)
- Simulation of fluid flow, heat transfer, and radiation
- Usability in application areas like HVAC and electronics cooling
- Parametric studies for design optimization
The Bridge to SimScale
While SOLIDWORKS offers useful simulation tools, there are scenarios where advanced analysis options, extensive computational resources, or specialized features are required. SimScale bridges this gap by providing access to a cloud-powered, comprehensive suite of simulation solutions that reinforces SOLIDWORKS’ CAD capabilities. In other words, designing in SOLIDWORKS has become significantly more powerful by leveraging the proven workflow with SimScale.
Key Benefits of Using SimScale for Simulating SOLIDWORKS Models
Here are some key reasons why engineers turn to SimScale in order to simulate their SOLIDWORKS CAD models:
- Cloud-Based Power: SimScale leverages cloud computing, eliminating the need for high-end hardware and reducing simulation time. Users can access SimScale instantly from anywhere, and collaboration becomes effortless, as team members can easily work together on the same simulation and design project directly in their web browsers without any special hardware and with unparalleled, real-time, in-app support from simulation experts.
- Advanced Solvers: SimScale offers highly reliable and advanced solvers for FEA, CFD, and thermal analysis, enabling engineers to tackle complex problems efficiently. These include non-linear analysis, modal analysis, multiphase flow, conjugate heat transfer, transient simulations, and more.
- Automation and Optimization: Parametric studies, optimization, and design exploration are simplified in SimScale. Engineers can explore multiple design variations by simulating them in parallel (multiple simulations at the same time) to achieve optimal results. There is no limit to the simulation size, number of parallel simulations, and storage.
- One Platform, Broad Physics: SimScale offers a single platform with broad physics capabilities for both early-stage and late-stage simulations.
- Cost-Effectiveness: Simulating in SimScale minimizes the total cost of ownership, making it economically viable for everyone from single users up to hundreds of seats.
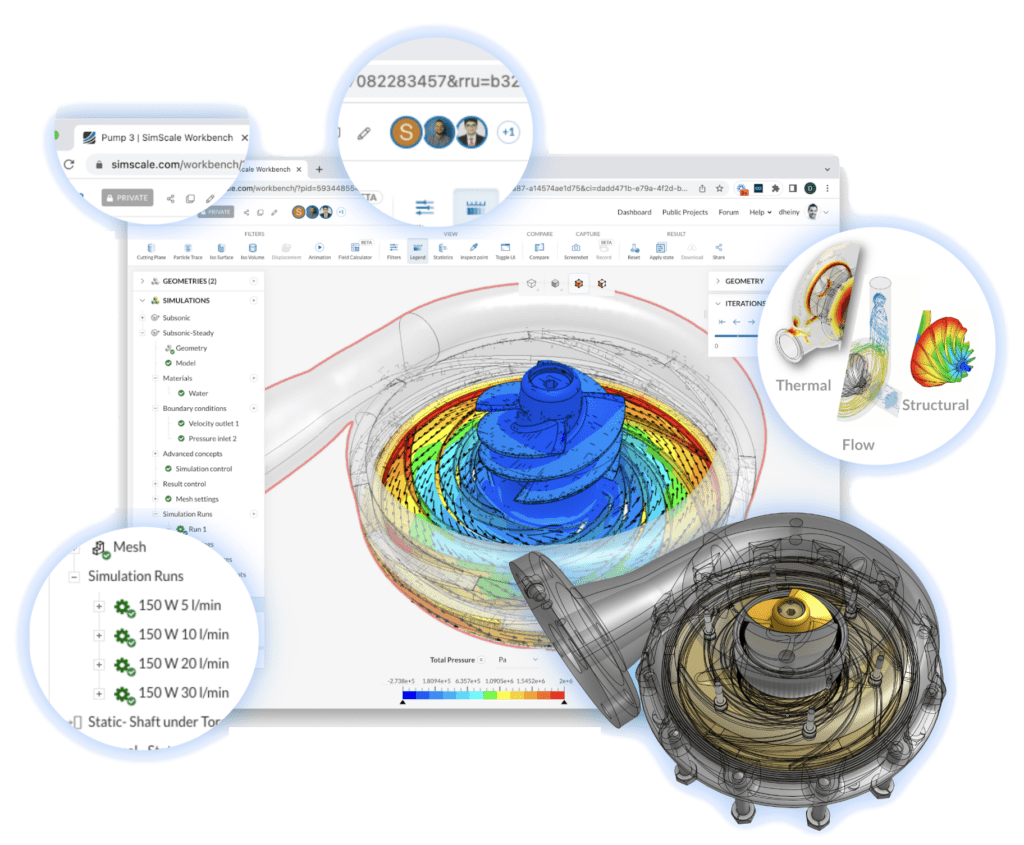
SOLIDWORKS and SimScale Associativity: The Key to a Seamless Workflow
The workflow between SOLIDWORKS and SimScale is designed to be seamless and user-friendly. The standout feature of this workflow is CAD associativity. This means that changes made to the original SOLIDWORKS CAD model automatically propagate to the SimScale simulation setup, eliminating the need for manual updates and ensuring that the simulation always reflects the latest design iteration.
When you design a product in SOLIDWORKS, every modification, no matter how minor, triggers an update in the associated SimScale simulation. This dynamic link ensures that engineers can make design improvements iteratively based on simulation results, leading to a more streamlined and efficient design validation process.
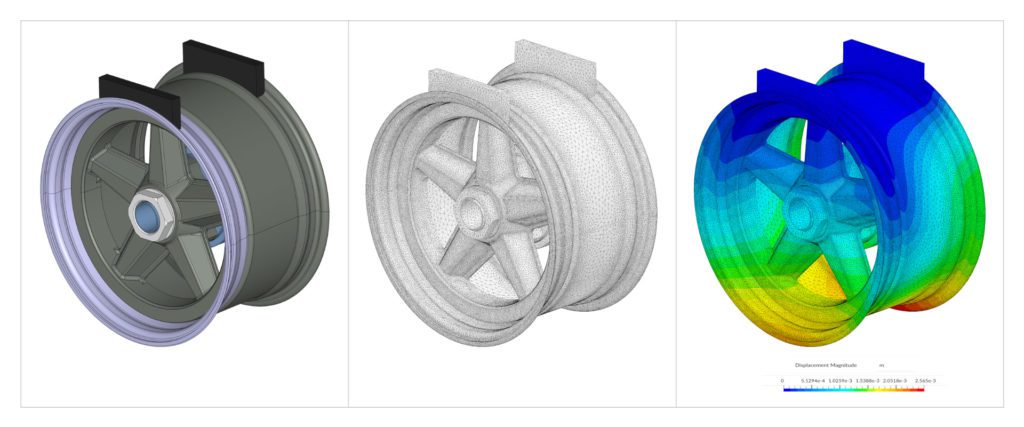
How It Works: Extending Your Design Capabilities with Simulation
The powerful synergy between SOLIDWORKS and SimScale unlocks a world of possibilities for engineers, making it possible to harness the full potential of their designs. With SOLIDWORKS providing high-quality 3D modeling capabilities and SimScale extending these capabilities with robust and comprehensive simulations in the cloud, users can achieve a higher level of design validation, optimization, and collaboration.
Simply, here is how the SOLIDWORKS-SimScale workflow works:
- Native format support: You can save SOLIDWORKS parts and assemblies in their native file formats and directly upload them to SimScale with no translation losses.
- Cloud-native simulation setup: You can set up sophisticated multiphysics simulations in SimScale by leveraging its broad-physics capabilities all on one cloud-based platform.
- Continue to design: You can continue to freely use your local computer for design work while the simulations are running in the cloud.
- Seamless design update: New design versions are associatively imported into SOLIDWORKS, retaining simulation settings for a fast iterative design process.
By seamlessly transitioning between these tools, engineers can bring innovative products to market faster and with greater confidence, all while continuing to design in SOLIDWORKS on their local computers and simulating in SimScale in the cloud. This integrated workflow truly showcases the simulation capabilities of SimScale and enhances the SOLIDWORKS experience for engineers across various industries.
Explore the SOLIDWORKS-SimScale proven workflow and sign up to SimScale to simulate your SOLIDWORKS CAD parts in the cloud.