Solid mechanics simulation has become an integral part of mechanics, especially in industrial design and manufacturing. It evolved with the development of numerical methods and the immense growth in computation power, enabling engineers to study mechanical phenomena by building accurate 3D models and simulating the behavior of solid materials.
But that’s not all. In this article, we will explore how simulation can not only help study mechanical phenomena but also enable better-informed decision-making early in the design process. In other words, we will see how engineers can benefit from one particular aspect of simulation that provides them with more accessibility, collaboration opportunities, and efficiency in both time and money.
What is Solid Mechanics?
Solid mechanics is a branch of physical science that focuses on studying the movement and deformation of solid materials under external loads such as forces, displacements, and accelerations. These loads can cause different effects on the materials, such as inertial forces, changes in temperature, chemical reactions, and electromagnetic forces. This field plays a critical role in various engineering disciplines, including aerospace, automotive, civil, mechanical, and materials engineering.
Solid mechanics focuses on understanding the mechanical properties of solid materials and their response to different types of loading. These materials include metals, alloys, composites, polymers, and others. By studying how materials behave under different conditions and in different environments, engineers can gain insights into designing and optimizing structures, components, and systems to ensure their safety, reliability, and performance.
In solid mechanics, there are two fundamental elements:
- The object’s internal resistance that acts to balance the external forces, represented by stress
- The object’s deformation and change in shape as a response to external forces, represented by strain
The relationship between stress and strain is described by Young’s Modulus, which states that strain occurring in a body is proportional to the applied stress as long as the deformation is relatively small – i.e., within the elastic limit of the solid body. This can be visualized in the stress-strain curve shown below.
What is Solid Mechanics Used for?
The importance of solid mechanics lies in its practical applications and contributions to engineering and the industry. The key reasons why solid mechanics is not only practical but crucial for engineers can be categorized as follows:
- Design analysis
- Failure analysis and prevention
- Material selection and optimization
- Structural safety and load-bearing capacity
- Performance optimization and efficiency
Design Analysis
Solid mechanics provides the foundation for designing and analyzing structures and components. By applying principles of solid mechanics, engineers can assess the structural integrity and performance of systems and ensure they meet design requirements and safety standards.
It enables them to predict and understand factors such as stresses, strains, and deformations, which are vital in designing structures that can withstand expected loading conditions and environmental factors.

Failure Analysis and Prevention
Solid mechanics helps engineers investigate and analyze failures in structures or components. By understanding the causes of failure, such as excessive stress, material fatigue, or deformation, engineers can improve design practices, materials selection, and manufacturing processes to prevent failures and enhance the reliability and durability of products.
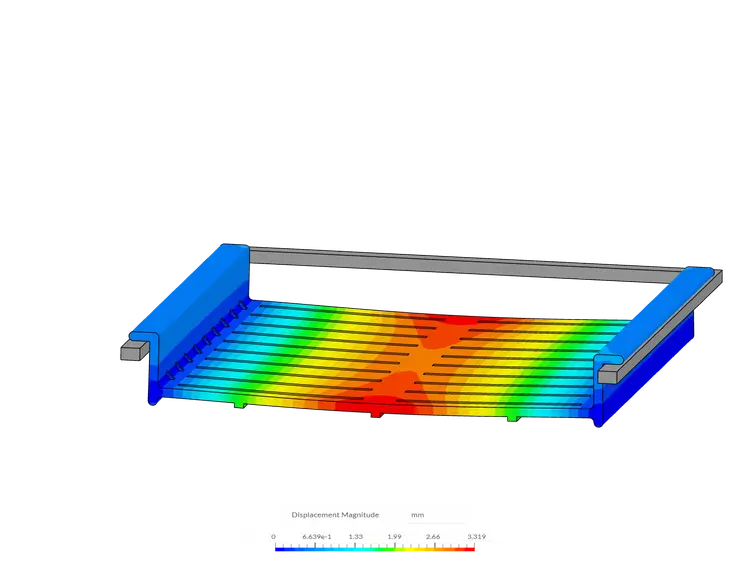
Material Selection and Optimization
Solid mechanics plays a significant role in material selection and optimization. Engineers need to evaluate the mechanical properties of different materials and assess their suitability for specific applications.
By considering factors such as strength, stiffness, toughness, and fatigue resistance, solid mechanics helps engineers choose the most appropriate materials to meet performance requirements while considering factors such as weight, cost, and manufacturability.
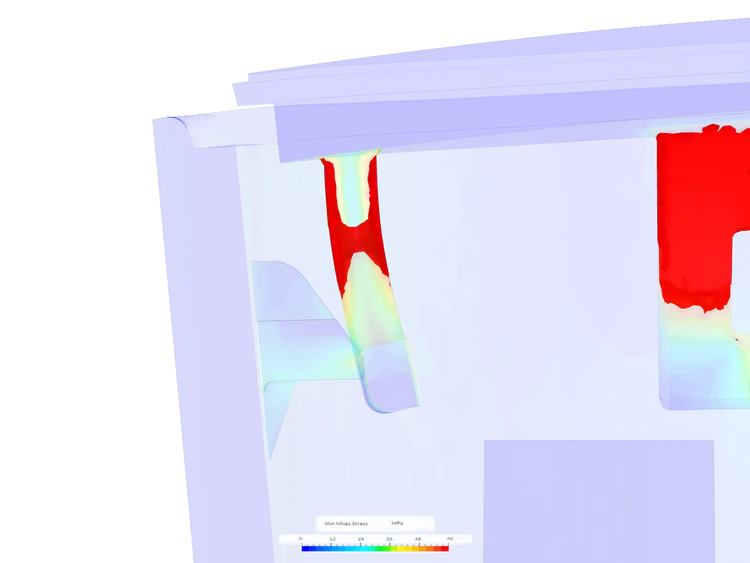
Structural Safety and Load-bearing Capacity
Solid mechanics allows engineers to assess the safety and load-bearing capacity of structures and objects. Through analysis and simulations, engineers can determine the structural stability, response to external forces, and ability to withstand static and dynamic loads.
This knowledge is essential in ensuring the integrity of critical structures, such as bridges, buildings, and aircraft, where failure could have severe consequences.
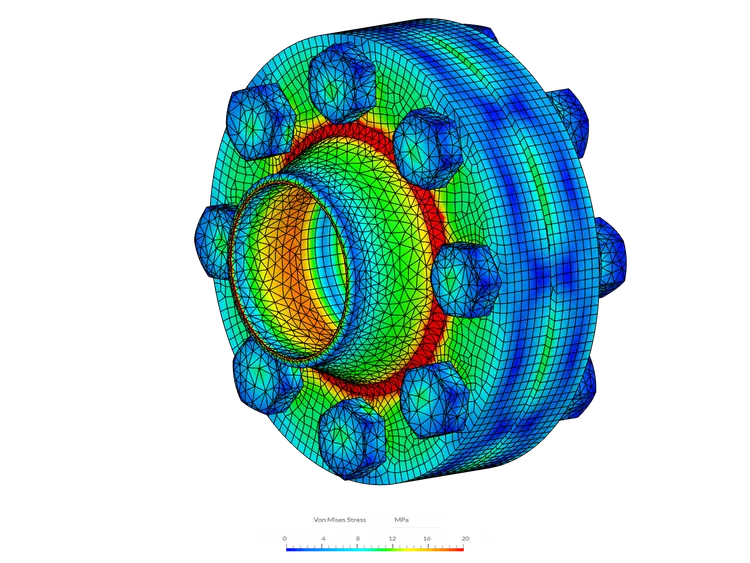
Performance Optimization and Efficiency
Solid mechanics helps engineers optimize designs to improve performance and efficiency. By analyzing stress distributions, material usage, and structural behavior, engineers can identify areas for improvement, reduce unnecessary material and weight, and optimize designs for enhanced strength, rigidity, or energy efficiency. This optimization process leads to cost savings, improved product performance, and reduced environmental impact.
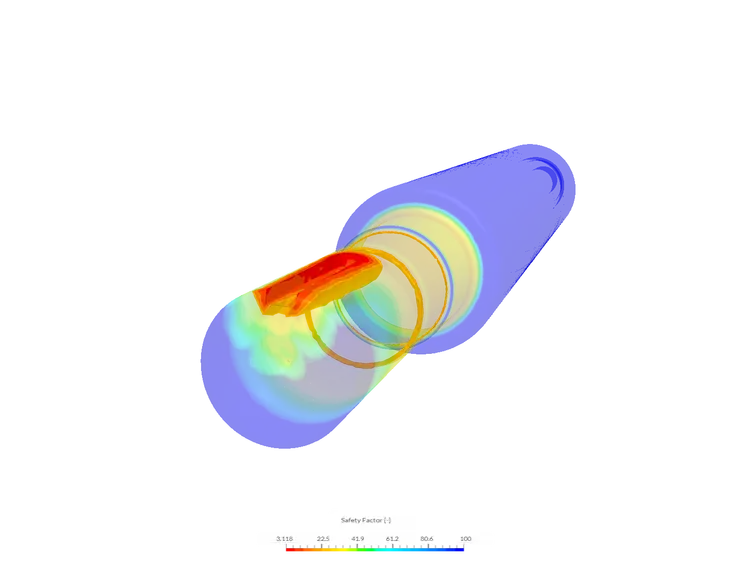
Using Simulation in Solid Mechanics
Understanding how solid materials behave under different conditions is crucial for a wide range of engineering and design applications. By simulating the behavior of solid materials, engineers and designers can optimize their designs and reduce the need for costly physical prototyping.
Using simulation software, engineers and designers can create virtual models of their designs and analyze their performance under various conditions. They can simulate stresses, strains, and deformations in solid materials.
The example below is a structural analysis of a wheel loader arm. This simulation project enabled the design engineer to study the relative movement between the components and assess the stress performance simultaneously. This assessment was done by calculating the Von Mises stress distribution within the arm. Such an approach almost eliminates the need for physical prototyping in the early stages of the design process.
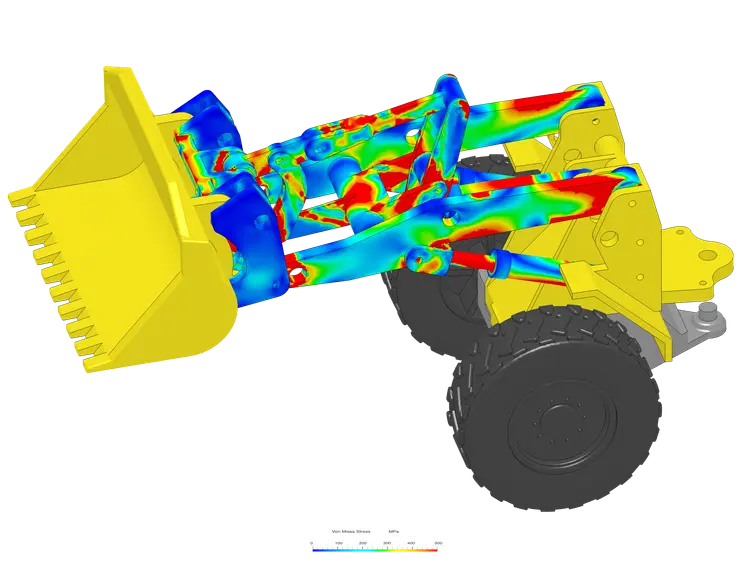
Finite Element Modeling in Solid Mechanics
Knowing that most engineering cases of solid mechanics are nonlinear by nature, analyzing them with analytical solutions may not be feasible. That’s where numerical modeling comes into play.
To simulate solid mechanics cases and assess the material behavior, engineers use finite element modeling (FEM), a numerical method upon which a simulation technique called Finite Element Analysis (FEA) is based.
FEA involves dividing a complex solid model into a finite number of smaller, interconnected elements to approximate the behavior of the structure. By applying appropriate boundary conditions and material properties, FEA can simulate the response of the structure to different loads, allowing engineers to assess stress, strain, displacement, and deformation patterns.
To further understand the details of FEA, check out our dedicated guide to Finite Element Analysis (FEA).
The FEA software in SimScale, for instance, helps engineers and designers virtually test and predict the behavior of solid bodies. This enables them to solve complex structural engineering problems under static or dynamic loading conditions.
Yet, with all this, you might still be wondering what exactly the single aspect of simulation benefiting engineers today is. Well, it goes beyond the mathematical side of simulation and capitalizes on the integration of another technology: the cloud.
Simulating Faster with SimScale
SimScale combines the capabilities of simulation with the benefits of cloud computing to enable engineers to analyze accurately, collaborate better, and innovate faster.
Using SimScale’s cloud simulation, you can access your simulation projects anytime, anywhere. All you need is a web browser. You simply sign up to SimScale, import your 3D design, and start simulating.
Furthermore, not only are your projects accessible to you, but you can also very easily share them with your colleagues and teams to collaborate on them, improve your designs quickly, and shorten your workflow significantly.
For example, the global engineering and manufacturing company Bühler uses SimScale to enable the collaboration between 15% of its mechanical and process engineers spread across 25 departments in ten business units on four continents.