The efficient and accurate cooling of an electric vehicle battery cold plate is critical to ensure their optimum performance, battery reliability, and lifecycle return on investment. High development costs can be mitigated with access to fast and accurate simulation insights using engineering simulation in the cloud. For example, additional R&D, prototyping, and machining costs are reduced by arriving at an optimized and less complex design, earlier in the design cycle.
This article presents a design and simulation study of battery cold plate technology for electric vehicles. Engineering simulation is used to perform a fully-coupled conjugate heat transfer analysis of a cold plate for dynamic thermal management. Furthermore, using an advanced Multi-purpose CFD solver, a design study is performed for evaluating pressure-flow characteristics across the cold plate flow channel. Parallel simulations in the cloud are used for scenario analysis both for geometric variants and multiple coolant flow rates. In this sample case, our simulation workflows show users how to set up and run a complete heat transfer and flow analysis of a cold plate, including pressure drop and temperature at various coolant flow rates. Engineers can follow this example to learn how to quickly complete a parametric design study in SimScale and answer key design questions.
Reaching Optimum Battery Reliability with CFD and Heat Transfer
SimScale has many analysis types available depending on the application. In this example, two analysis types have been used to analyze battery cold plate optimization for electric vehicle batteries. The Multi-purpose analysis type in SimScale produces an automated and robust hexahedral cell mesh, using the body-fitted Cartesian meshing technique that significantly reduces mesh generation times by an order of magnitude. The highly parallelized meshing algorithm gives a higher quality mesh requiring much fewer cells to attain comparable accuracy to traditional discretization schemes. This leads to faster convergence and hence, faster simulations.
The Multi-purpose analysis type is used to simulate both incompressible and compressible flow, with turbulence modeled using the RANS equations and the k-epsilon turbulence model. A powerful feature of this analysis type is the built-in parametric capability for defining velocity inlet boundary conditions. At the simulation setup stage, users can define multiple inlet flow rates at once, that are then simulated simultaneously. The conjugate heat transfer (CHT) analysis type in SimScale enables heat transfer analysis between solid and fluid domains. Typical applications of CHT analysis type include analysis of heat exchangers, cooling of electronic equipment and electronics enclosures, and LED luminaire design. A fluid/solid mesh is required for a CHT simulation with clear definitions of the fluid and solid interfaces, also referred to as contacts. The mesh is automatically generated in SimScale, with local refinement available for advanced users. In the case of the battery cold plate, the Multi-purpose analysis is used to simulate coolant flow through the cold plate channel to ascertain optimal flow rates with regard to pressure drop. The CHT solver is used to demonstrate heat exchanger effectiveness and thermal performance.

Improving Battery Cold Plate Design
The purpose of this study is to maximize the dynamic thermal management of a new battery cold plate design, used to cool electric vehicle battery packs. We will consider two versions of a cold plate heat exchanger. The original design (V1) is a common component widely used in industry and has a single serpentine cooling channel. The design is known to cause hotspots that lead to battery longevity issues. A thermal engineer has come up with a new design (V2) that uses a labyrinth cooling channel with a much-increased surface area for thermal energy exchange. This is an early-stage proof of concept design that requires simulations to validate its predicted performance and compare it with the original version.
Using SimScale, an engineer can quickly and accurately assess both designs. Both battery cold plate designs have one inlet and one outlet. A velocity inlet is used to define the mass flow rate of the coolant (water) which is the primary heat removal mechanism for extracting heat from the batteries. The battery cold plate is assigned Aluminum from the SimScale materials library, water for the coolant, and a power source is applied to represent heat generated by the battery. When importing the V2 CAD file, associativity between cad files is applied automatically in SimScale, maintaining naming conventions for parts/faces from the V1 CAD model. This means that when swapping CAD files for comparative studies, users don’t have to reassign boundary conditions, mesh settings, or result control outputs, making comparing two or more CAD variants of a single product much faster.
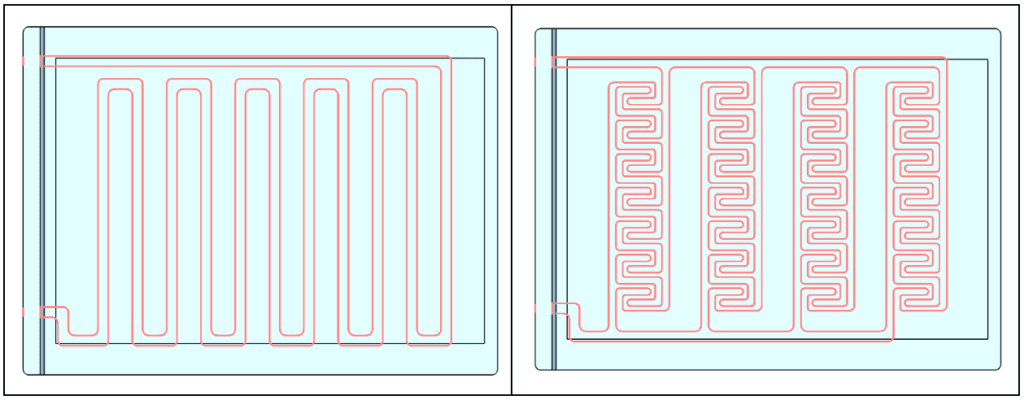
The heat transfer analysis shows that despite a larger contact surface area in V2, thermal results are much worse compared to the original V1 design, as V2 exhibits higher temperatures across the battery cold plate. The V2 design needs further simulation and optimization. To help resolve these counterintuitive results, the design engineer analyzes the flow in isolation.
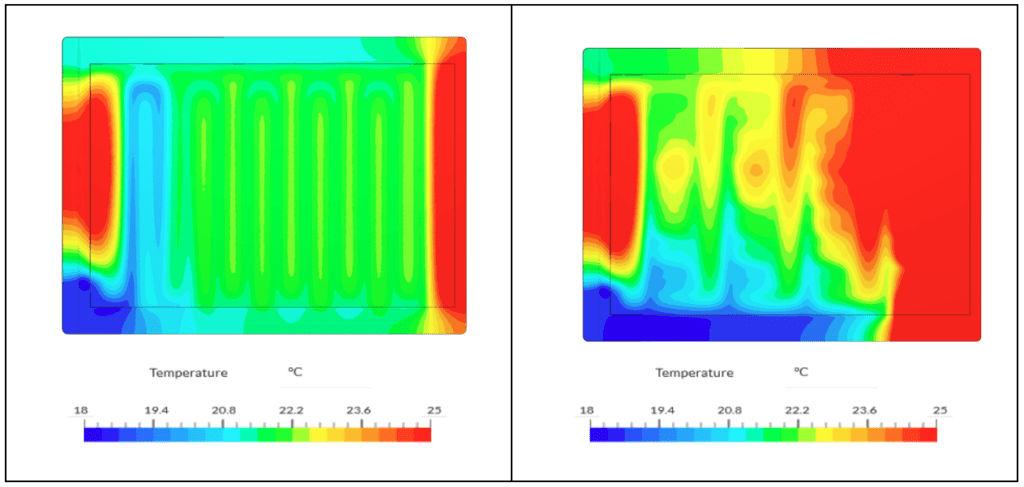
Results of the subsonic fluid flow analysis, which takes just four minutes to solve, yield further insight. The flow in V1 maintains a steady flow of 3.5 m/s throughout the single channel. In the V2 design, highly varied coolant velocity is seen throughout the labyrinth channels. In many areas, almost stagnant flow is observed in the areas of peak temperature, hence the cooling channels are not effectively removing heat from those areas which leads to poorer thermal performance. We can use the fluid flow analysis to look purely at flow velocity to better understand pressure drop across the cold plate. The converged pressure drop across any two points can be extracted from SimScale using the results control menu. In this case, for a constant coolant flow rate of 0.13 kg/s, V1 has a 292 KPa pressure drop between inlet and outlet and, V2 is ten times less at 22.7 KPa. This might have some advantages if the thermal performance of V2 was comparable to V1, such as less pump power and hence energy needed to operate the pump. First, we need to try and increase its thermal performance, however. Since we have enough pressure drop to play with, we might try and increase the coolant flow through V2.
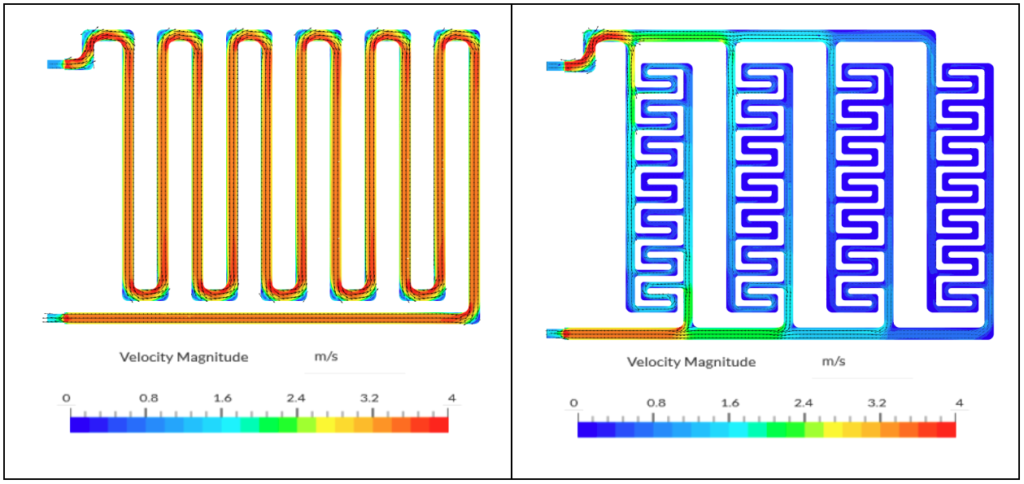
Using the parametric inputs in the Multi-purpose analysis type, we can specify multiple flow rates in the inlet boundary condition to run in parallel. Simscale will recognize that we have a parameterized study setup and all runs (all flow rates) are simulated in parallel in the cloud on SimScale servers. This frees up your local PC/laptop and does not consume machine resources. SimScale will send users an email notification when all the runs have been completed successfully.
A higher mass flow rate of 0.3 kg/s gives increased flow velocities in V2 and improved thermal performance. The pressure drop across the cooling plate has increased considerably but is still 60% lower than the original V1 design. The new V2 cooling plate design has achieved a lower average temperature, although less uniform, with a higher flow rate but a much lower pressure drop than V1. Additional design iterations would be necessary to improve the temperature distribution and battery reliability further in V2. Engineers looking to optimize this battery cooling plate can parametrize the CAD model, coolant flow rate, and inlet temperatures for more detailed design studies. Swapping materials is also simple by using the extensive SimScale materials library.
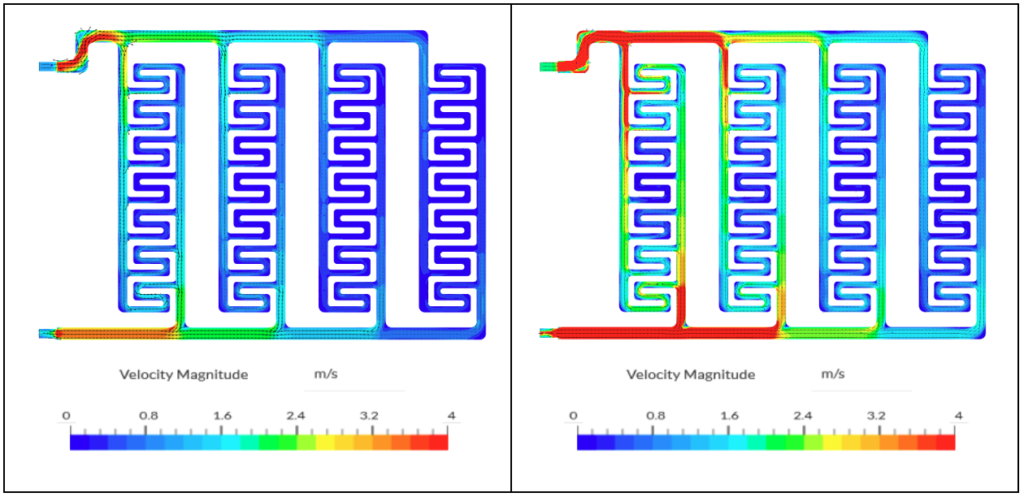
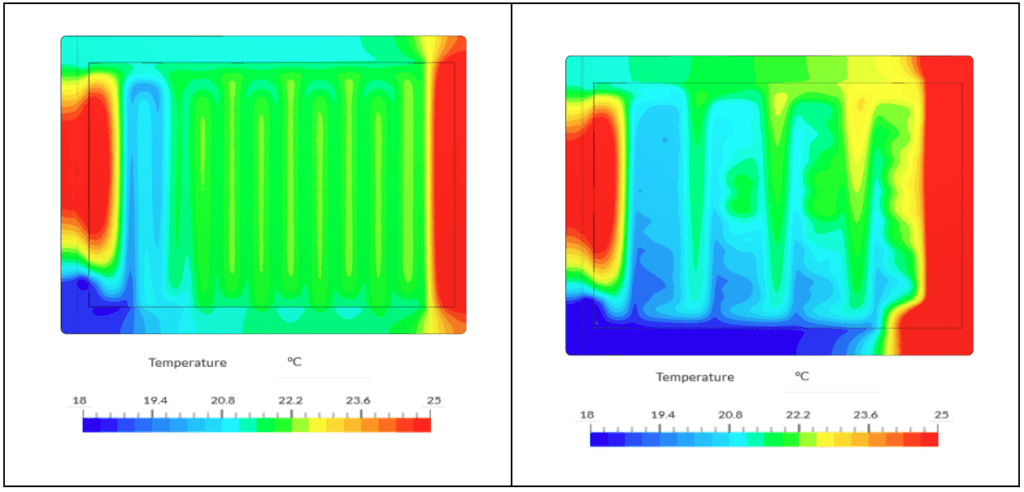
Heat Transfer Simulation in the Cloud
Access to simulation in the early product design stages is essential to achieving the required thermal performance of battery cold plate designs, all while reducing physical prototyping costs. With the cloud-native SimScale platform engineers and designers can harness advanced solvers that account for coupled analyses of conduction, convection, and radiation to deliver accurate results across a variety of problem domains and scales.
Watch our on-demand demo, Cooling Performance Optimization of Electric Vehicle Batteries, to see how you can quickly complete a parametric design study and run a complete thermal analysis of a cooling plate including pressure drop and temperature at various coolant flow rates: