Never before has a 1-kilowatt generator been squeezed into a device just 3 inches in diameter. That is until American Wind developed its innovative micro wind turbine, which is integrated with a small, yet very powerful, generator. Still, a powerful generator doesn’t mean much in a wind turbine if it’s not able to capture the energy from the wind. This is why the company developed a new blade design to replace the simple airfoil-based ones.
For this, American Wind’s founder Robert Yost used his experience in designing jet engine turbines to develop a blade that used both airfoil technology and jet turbine technology. This allowed American Wind’s turbines to start functioning at a much lower wind speed than any other turbine on the market, which meant the micro wind turbine can create power through a larger range of wind speeds.

Challenge: Testing American Wind’s MicroCube
With the design ready, Robert wanted to investigate the performance of the MicroCube wind turbine in the operational conditions. The verification of the experimental results would be the first step before using the analysis for further development. It was clear that experimental tests provided the most accurate data. At the same time, they give a limited overview of the micro turbine’s performance. With computer-aided engineering, it was possible to visualize all the features of the wind flow at any given point. Having such data provided a significant advantage for optimizing the product’s design.
This free infographic illustrates how architects and engineers can use CFD to virtually test and optimize building designs and HVAC systems. Download it for free.
Solution: Simulating the Micro Wind Turbine with CFD
Using the SimScale cloud-based CAE platform, the engineers at American Wind meshed the MicroCube’s CAD model in a way that resembled the live wind tunnel at which it was tested. A square channel was placed before and after the compact MicroCube. The expected air flow was turbulent, though the range of operational wind speeds indicated that an incompressible model would be sufficient. To incorporate the motion of the fan blades, a multi-reference-frame (MRF) rotation model was used. Although the MRF model simplifies the simulation by “freezing” the rotor, it allows a fast and accurate evaluation of the steady state conditions of the case.
The obtained mesh consisted of over 7 mln volumes. It included local area refinements, surface refinements, and turbulent boundary layer mesh.
During the analysis, it was assumed that the blades were rotating at a fixed speed dependent on the inflow air velocity, based on experimental data. This is a common approach when testing turbines, which allows the investigation of actual wind flow patterns.
The captured data involved all flow field data (pressure, velocity) and extra forces and moments acting on the whole MicroCube, as well as the forces and moments acting on the blades. During post-processing, the difference in flow rotation before and after the micro wind turbine was calculated.
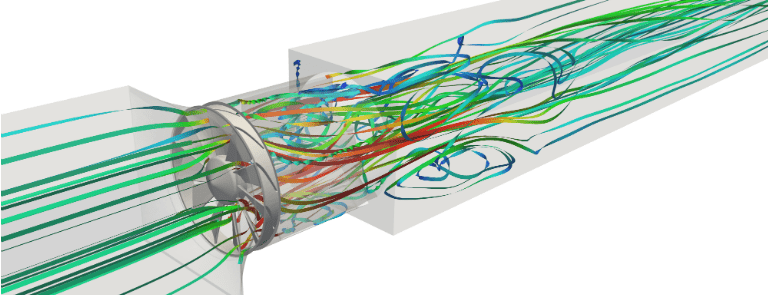
The two main challenges in the analysis were the preparation of the mesh and obtaining reliable, converged solutions. It took several attempts to obtain a mesh that would be accurate enough and at the same time reasonably big to facilitate the calculation. Fortunately, thanks to the semi-automated manual meshing, the creation of mesh variations was not too challenging.
The second main issue was evaluating the results’ accuracy. In most cases, it was impossible to tell if the results were good or not until the simulation finished. On the other hand, SimScale allows the calculation of multiple simulations at the same time, which helped the engineers complete the whole analysis 20 times faster than they would have on a single computing unit.
Simulation Results
In total, 26 operation conditions were analyzed, ranging from extremely low wind speeds up to expected limit conditions.
On average, each simulation required 10h of computation time.
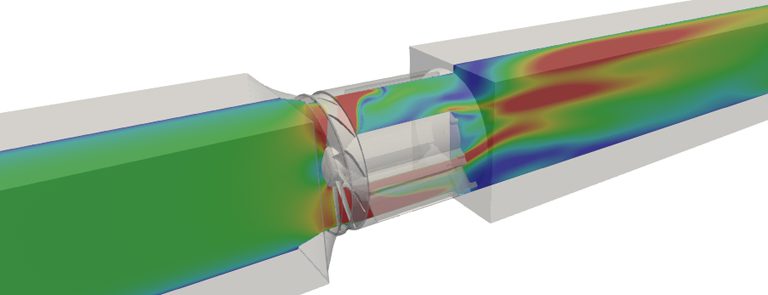
Four of these simulation runs needed to be repeated with modified numerical conditions and extended convergence times to obtain correct results.
Although the residual plots in many cases did not present perfect convergence, this could be attributed to the mesh quality and development of flow features behind the blades.
Extending the simulations would most likely not improve the quality of the data since it was most probably limited by the mesh.
An additional interesting result found during the analysis was the occurrence of a wind recirculation region that was discovered attached to the stator arms of the MicroCube.
Awareness of the presence of this flow feature opens up the possibility of optimization of the shape of the stator (generator mount) in a way that will reduce energy losses due to recirculation.
We hope you enjoyed American Wind’s story of optimizing its micro wind turbine design. You can find the original success story on the SimScale website. If you’d like to learn more about SimScale’s customers, check out our dedicated page.
Discover all the simulation features provided by SimScale. Download the document below.