Keeping with the momentum of last year, 2019 will start with a major update to the overall meshing and simulation workflow.
Simulation allows users to gain valuable insights into the physical properties and behaviors of a design. It’s a means to an end, not an end to itself. Historically, professional-grade simulation, along with SimScale, was quite a complex undertaking with a high barrier to entry. With this month’s update, we’re taking one a step towards a more user-friendly interface, and a giant leap towards a holistically improved simulation experience.
Meshing Integrated into Simulation Tree
This update is all about making simulation more accessible while working to remove the complexity of meshing as a necessary step before the simulation setup—something that will particularly help novice users to successfully simulate faster and easier.
With the release of the new workbench in October 2018 we shipped a feature called “CAD-Based Simulation Setup”, which allows all simulation assignments to be made directly on the original CAD model instead of a mesh. The added benefit of this approach is that in the case there is a need to change or refine the mesh later, the mesh can be exchanged while all settings and assignments are kept.
Another benefit of this approach is that a simulation setup will no longer depend on a computed mesh. This led us to make a fundamental change to the default simulation workflow on the SimScale Platform. The following chart illustrates the changes:
Choosing the Right Meshing Algorithm
Meshing is a concept that has always eluded many of our users. And who can blame them? If you did not happen to have studied Computational Science or Engineering, how likely would it be that you are aware of the specifics of the mathematical models behind simulation or the requirement of a discretized simulation domain?
The goal of SimScale is to make simulation accessible to everyone, independent of skill level. By integrating the mesh setup into the simulation tree, we can make sure to prevent the common pitfall of choosing the wrong mesh for the intended analysis type. Knowing the analysis type before the mesh is created allows us to create a compatible mesh setup by default. This prevents the user from creating an incompatible mesh.
In turn, this change reinforces the intended new workflow of defining all assignments directly on the CAD model instead of the mesh, and highlights that meshes can easily be exchanged if required. The entire navigation tree now looks as follows:
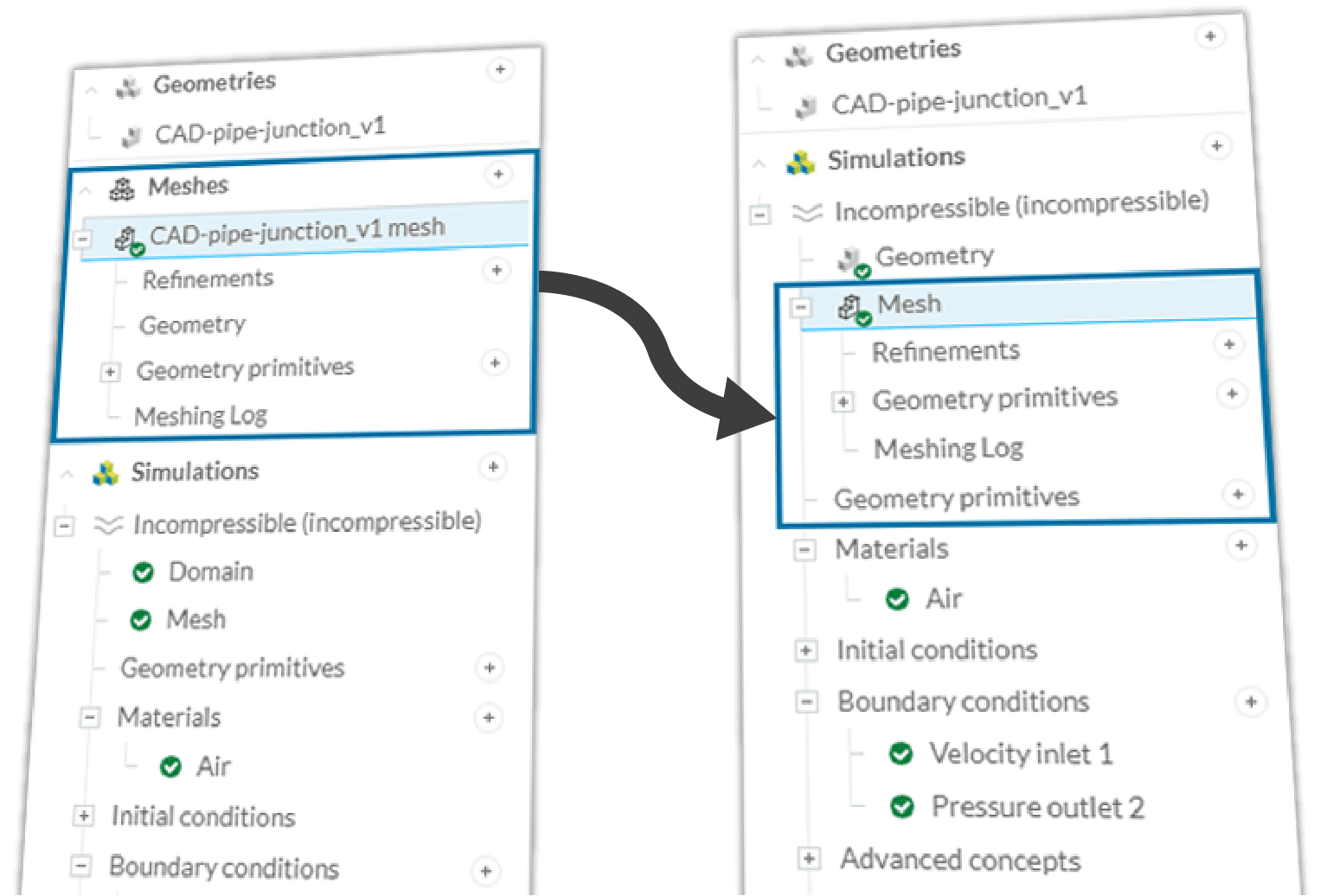
Where Did My Meshes Go?
Not to worry! All your meshes are still there, but are now hidden inside of your simulations. Just open the mesh panel in any of your simulation trees and you’ll find a list of all meshes based on the simulation geometry, which are compatible with the analysis type of your simulation.
By default, whenever you create a new simulation or assign another geometry to an existing simulation, a new mesh setup that is compatible with the chosen analysis type is created in case none yet exists.
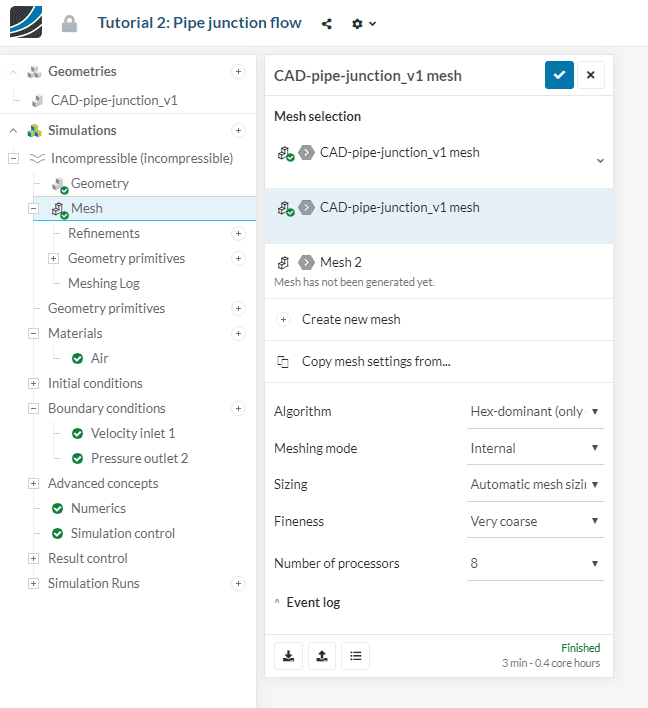
Importing Mesh Settings
Another common use case, simulating multiple iterations of a design, now also becomes easier than ever before. Simply upload the modified CAD model, duplicate your simulation, import mesh settings from another mesh, and start your runs. For the time being, it will still be required to start your meshing and simulation runs independently. Once we’re confident in the automatic meshing capabilities of SimScale, the goal is to link the meshing and simulation runs together, streamlining the entire simulation workflow even more.
With this update, we ultimately hope to reduce the complexity and difficulty of running a professional-grade simulation with SimScale.
We’re also planning further improvements to this workflow in the near future. So stay tuned for more updates coming soon!