In 2022-2023, SimScale has taken on board valuable feature requests and has been consistently conducting regular maintenance to make sure the product enables users to simulate better and innovate faster. Over the past few months, SimScale has released highly anticipated features and updates to the product, including the fascinating multiphase capabilities and joule heating application.
In this blog post, we want to get you up to date with all of the new key features released in Q1 2023. Let’s dive in!
- Improved Wind Data for PWC Analysis
- Humidity Modeling
- Realizable Turbulence Model
- Solids included in solar radiation
- Joule Heating
- Immersed Boundary Method (IBM) external flow domain flexibility
- Simplify/heal bodies with Surface Wrapping
- Multiphase
- Relative Velocity
- Boundary condition Visualization Inside 3D Viewer
- Export result statistics to CSV
- Teams and Permissions
- Bilinear elastoplastic material model
- “Max over Phase” von Mises stress result field for harmonic analysis
1. Improved Wind Data for PWC Analysis
Improved accuracy and global coverage with the new ERA5T dataset, which replaces the previous NEMS30 dataset. Also, the new modal is provided via our connected wind data service partner, meteoblue, and is the most accurate dataset available for wind data. Additionally, we now have the ability to derive seasonal wind roses from the new dataset, which will be coming in future months.
2. Humidity Modeling
Humidity plays a big part in thermal comfort analyses, and SimScale can now account for it.
Humidity modeling can be hugely important to internal thermal comfort studies for identifying where condensation might occur as well as for analyzing indoor environments where tightly controlled humidity levels are critical, such as concert halls, storage facilities, or indoor farming.
3. Realizable Turbulence Model
For urban wind applications, this turbulence model is declared as the preferred one by several best practice guidelines (COST Action 732) as well as wind engineering guidelines, such as the City of London (CoL) Wind Microclimate Guidelines (ref), if a steady-state CFD simulation is run.
The realizable k-epsilon model is now available for the Incompressible analysis type on SimScale within the top-level analysis type settings.
Use Case & Benefits
Urban pollutant dispersion analysis using the Incompressible analysis type on SimScale for enhanced result accuracy compared to the standard k-epsilon turbulence model.
4. Solids included in solar radiation
It is now possible to model solar loads in CHT analyses with models that have both fluids and solids included.
Use Case & Benefits
- Solar radiation can play a large factor in thermal comfort, and the ability to model it with solids included increases the overall simulation accuracy.
- Solid walls at the boundaries of the flow region don’t need to be modeled with specific boundary conditions defining the conductivity and material thickness but can instead be assigned the specific material, and their thermal properties will be correctly accounted for
- Solids inside the fluid domain simply need the correct material assigned.
The current limitation is that the solids in a CHT analysis with solar load can not be semi-transparent, so windows and facade glazings need to be modeled with an appropriate boundary condition.
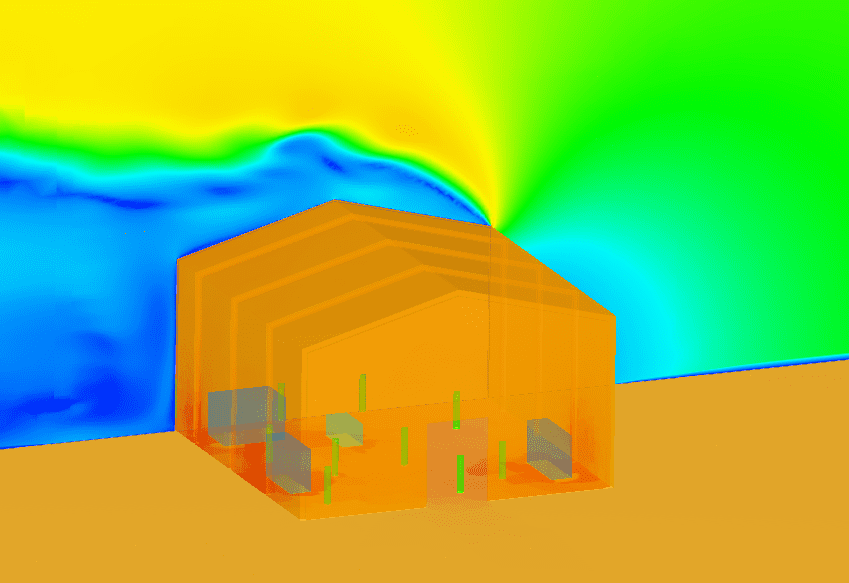
5. Joule Heating
Q1 sees the release of Joule heating. This works with Direct Current (DC) applications and is integrated into the CHT and IBM analysis types. Applying Joule Heating to a part, or parts will cause them to heat up realistically.
6. Immersed Boundary Method (IBM) external flow domain flexibility
IBM (Immersed Boundary Method) now allows for different external flow domain positions. This means that we can position the test unit on the floor, wall, ceiling, or suspended in the middle.
Use Case & Benefits
Useful for:
- Lighting, as it can be positioned anywhere
- All electronic assemblies as they are often designed with multiple orientations and installation positions in mind
7. Simplify/heal bodies with Surface Wrapping
Parts are sometimes too complex to work with and so can be simplified with Simscale’s CAD tools. This can currently be found under ‘surface wrap’.
- Faulty models can cause meshing problems, and fixing/simplifying parts in advance should avoid this
- Sheet bodies can be difficult to mesh – wrapping them and forming a solid can solve this too

8. Multiphase
One of our highest-requested features is now in production!
This feature introduces a proprietary multiphase capability within SimScale, with industry-validated methods for high accuracy and fast simulation turnaround for rotating equipment, hydraulics, and industrial equipment simulations.
Benefits
- Volume-of-Fluid algorithm with proprietary high-order reconstruction scheme that captures sharp interfaces well
- Comprehensive physics, including heat transfer and surface tension
- Handling of realistic fluid and material properties
- Binary tree-based meshing and automatic local time stepping for proven stability for complicated geometries
Use-Cases
- All types of turbomachinery, rotating equipment & flow control simulations
- Hydraulic engineering / AEC applications (reservoir, dam gate, etc.)
- Industrial mixers, aeration tanks, tank filling simulations
- Marine applications (static ship hydrodynamics, propulsion systems)
9. Relative Velocity
For correct visualization of rotating equipment flow simulations, it is important to show velocity relative to the rotating blades.
Visualizing the relative velocity field in a turbomachine is crucial as it gives designers insight into the nature of flow within the machine. It is used for creating velocity triangles, which help designers estimate the early-stage performance of the rotating geometry.
Highly demanded by our turbomachinery customers, SimScale will now compute and render relative velocity fields through the rotating regions. This field can be visualized as streamlines, vectors, contours, iso-surfaces, or iso-volumes, and will provide our users greater insight into the flow around rotating components.
10. Boundary condition Visualization Inside 3D Viewer
Boundary conditions are now shown inside SimScale! This has been a long time coming, with (believe it or not) years of effort to prepare everything in the background. Now that it is live, we will continue to iterate on it. If you are actively using SimScale, you will see this evolve over the next quarters.
11. Export result statistics to CSV
The ‘Statistics’ panel can now export all of the data points into a CSV file for external processing. This can be hugely useful with models that contain multiple fluid channels like the one shown below.
Use Cases
- Large organizations that need to control access to content internally
- Small organizations that need to organize content more efficiently
Benefits
- Granular access control
- Intuitive data segregation
- Control of sharing of Team content
- All self-managed

12. Teams and Permissions
Members of teams can now have varying levels of access to content contained within a team, and administrators can manage these settings in their dashboard.
Each member can have view, copy, or edit permissions of the teams they belong to. Each team also includes a setting to control with whom content can be shared (to/from a team):
- No sharing
- Share within the Team
- Share with the organization
- Share with anyone
13. Bilinear elastoplastic material model
Users can now apply bi-linear material behavior via a dedicated interface. Young’s Modulus, Yield stress, Ultimate stress, and strain are simple to define. This change improves non-linear simulation robustness.
14. “Max over Phase” von Mises stress result field for harmonic analysis
Von Mises stress is now available for each frequency in harmonic analyses. This means that as well as identifying resonant frequencies, engineers can also ensure that the structure remains within maximum stress safety limits.
Take These New Features for a Spin Yourself
All of these new features are now live on SimScale. They are really just one browser window away from you! If you wish to try out these new features for yourself and don’t already have a SimScale account then you can easily sign up here for a trial. Please stay tuned for our next quarterly product update.