The industrial equipment industry is at a transformative crossroads. With a heightened focus on sustainability and the rapid shift to electrification and energy transition, companies face relentless pressure to innovate, cut costs, and improve efficiencies. And the stakes are high: they must deliver cutting-edge products faster, cheaper, and more sustainably without compromising quality or performance.
Traditionally, this sector has relied on robust yet often rigid and demanding processes. One primary challenge is the small-batch design process that is highly customer-specific, making it difficult to set up efficient, standardized operations. Similarly, the difficulty to prototype given the size of industrial equipment makes things more complicated, not to mention the often hazardous operating conditions and long life expectancies of such equipment. All these challenges render development cycles long and cumbersome. Evidently, creating and refining physical prototypes of industrial equipment consumes a significant amount of time, and any changes or iterations can further extend these timelines, delaying market entry and affecting competitiveness.
Therefore, leading companies have opted for simulation and virtual prototyping to meet market demands and improve their bottom-line savings. Yet, traditional simulation tools still fall short of what is expected in such a fast-paced industry, especially considering the ever-shorter project timelines versus the long simulation lead time needed to ensure high-quality results. That is why cloud-native simulation has become the clear choice for industrial equipment manufacturers, as it inherently resolves this bottleneck by enabling enterprise-wide simulation deployment at much earlier stages in the projects. Let’s take a closer look.
What’s Holding the Industry Back?
The industrial equipment sector is inherently complex, characterized by extensive customization and the need to adapt to varying field conditions. Companies producing HVAC systems, energy transmission equipment, and manufacturing machinery, to name a few, often find themselves grappling with the intricacies of tailoring products to specific requirements. This customization necessitates intricate design and manufacturing processes, which complicates efforts to standardize and streamline operations.
Also, traditional engineering processes can often be inefficient, relying on sequential design, prototyping, and testing stages. This sequential approach increases lead times and operational costs. In fact, the cost associated with physical testing and potential equipment failures can be daunting. Physical prototyping requires substantial investment in materials, labor, and manufacturing resources. Each iteration adds to these expenses, making the process a financial burden.
This high cost of prototyping and testing often means resources are diverted from other critical areas. Efficient resource allocation becomes challenging when so much of the budget is tied up in the development phase. Furthermore, when a prototype fails, especially late in the development process, the repercussions are not just financial but also temporal, delaying time-to-market and impacting profitability. In this high-stakes environment, the need for accurate, timely simulation becomes evident.
However, traditional simulation approaches come with their own set of challenges. While simulation can help achieve first-time-right (FTR) designs, the process is often prohibitively time-consuming. Waiting for weeks for simulation results can force companies into a difficult position: either over-engineer products to ensure reliability or release them with potential field risks. In fact, many product lines may end up not being simulated, which heightens the risks even more. This trade-off between quality and speed is a significant pain point for many engineering teams in the industry.
Further complicating matters is the reliance on centralized simulation teams or outsourcing simulation to external vendors. This model creates bottlenecks, making it challenging to achieve the rapid simulation lead times necessary for integrating simulation into more projects and tender bids. This is where cloud-native simulation, offered by SimScale, proves to be a game-changer.
Cloud-Native Simulation for Industrial Machinery Manufacturing
Our latest eBook explores how cloud-native simulation is transforming industrial machinery manufacturing challenges into opportunities. Download it for free by clicking the button below.
Accelerating Industrial Equipment Design with Cloud-Native Simulation
SimScale’s cloud-native simulation platform is an innovative solution for all companies seeking to speed up their prototyping and design cycles while minimizing their associated costs. It enables industrial equipment companies to leverage enterprise-wide simulation to accelerate innovation and increase efficiency.
By capitalizing on cloud computing, simulations that once took weeks can now be completed in mere hours. Such a dramatic reduction in simulation cycle time and simulation lead time enables project engineers to incorporate simulation results almost in real time, significantly accelerating the design process. This provides a significant advantage over traditional, locally deployed simulation tools that are almost exclusively used by centralized simulation teams or external providers.
A cloud-native simulation stack helps companies deploy simulation ‘into the loop,’ driven by project engineers. Engineers no longer need to rely solely on centralized teams or external providers; instead, they can run simulations independently, while simulation experts maintain oversight, method development, and quality control. This democratization of simulation capabilities means that more engineers can engage in the process, leading to more equipment getting simulated, thus increasing innovation and efficiency while reducing risk and cost. Here is what Aquabio, an advanced system provider for treating and reusing industrial wastewater, had to say about incorporating SimScale into their design workflows.
“Previously, we were outsourcing CFD simulations to consulting firms which was taking a lot of time and cost from our projects. With SimScale, we’ve brought simulation in-house and have been able to do this with the excellent support from SimScale. I can now use engineering simulation at a much earlier stage of the project, including bidding for tenders.”
Alex Meredith, Engineer at Aquabio

Accessibility, usability, and cost-effectiveness are not the only key advantages of cloud-native simulation. Faster simulation cycles enable engineers to explore multiple design iterations without excessive time or cost penalties. This fosters innovation and leads to better, more reliable products. The ability to rapidly prototype and test designs reduces the risk of field failures and over-engineering, enhancing product reliability and customer satisfaction.
Cloud-native simulation takes engineering simulation into its third generation, where simulation becomes a backbone for the business. In other words, with the shift from local, siloed workflows to collaborative and efficient workflows, engineering simulation transforms from a singular task into a strategic facilitator of innovation, efficiency, and competitiveness. It expands beyond the validation stage at the end of a design cycle to underpin the entire design process, especially in its early stages, where engineers can analyze and optimize their designs in real time. This simulation-driven design approach helps drive better-informed decision-making, accelerate innovation, and substantially enhance engineering efficiency.
Boosting Top-Line Growth and Bottom-Line Savings
For industry-leading companies, getting new products to market quickly is crucial. Cloud-native simulation from SimScale compresses development timelines, allowing these companies to introduce innovative products faster than their competitors. This speed-to-market can significantly boost top-line growth by capturing market share and meeting customer demands promptly.
Similarly, operational efficiency, a critical driver of profitability in the manufacturing sector, is greatly enhanced by cloud-native simulation. By integrating these capabilities into their processes, companies can streamline workflows, reduce waste, and optimize resource utilization. Virtual testing of various scenarios and conditions leads to better decision-making and operational strategies.
This is what the engineering team at Bühler Group achieved. By rapidly deploying early-stage design simulation to over 100 engineers across 25 departments, they enabled their engineers to use simulation online, on demand, and without any capacity limitations. This allowed for straightforward scalability of simulation use when required, leading to faster build-up of skills, faster design convergence, and reduced physical prototyping costs. This not only helped accelerate innovation but also boosted bottom-line savings by switching to a cloud-native simulation stack and avoiding the high hardware costs and licensing fees associated with traditional simulation tools.
“SimScale is easy to use with great support, such that a simulation newbie was able to study 60 different design variants in only 2 weeks, which eventually allowed to gain confidence for the scale-up.”
Folke Schmidt, R&D Team Manager in Grain Quality at Bühler
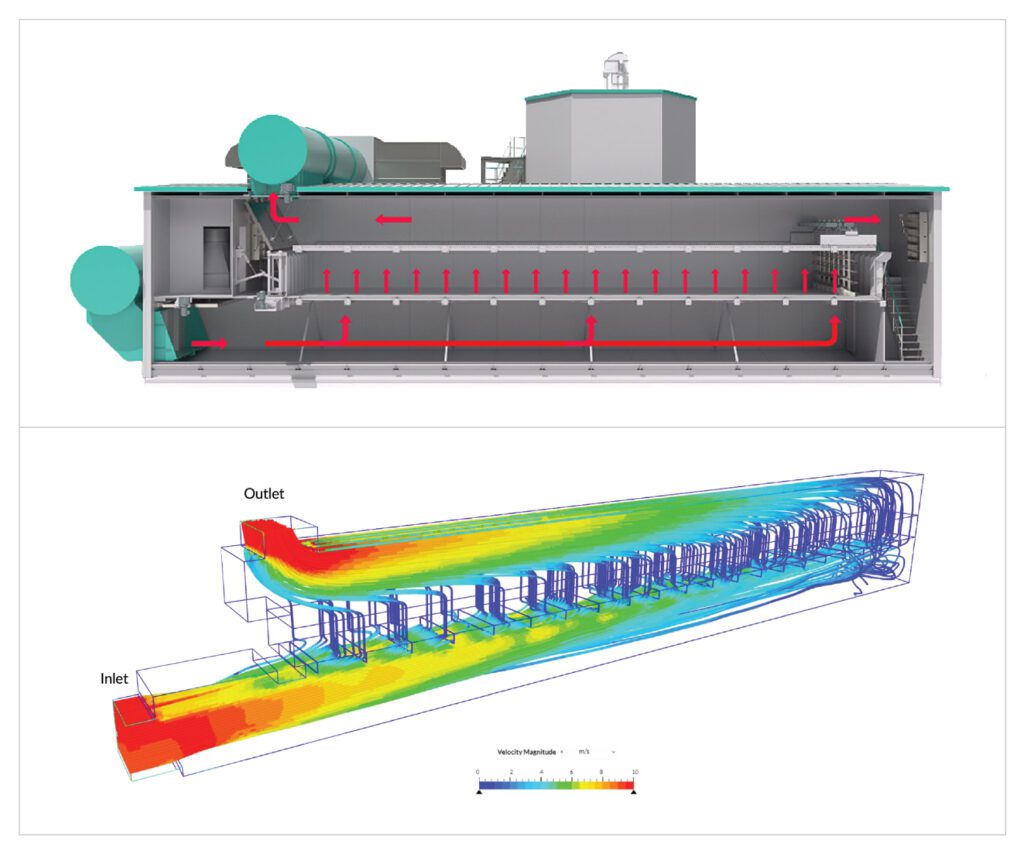
Simulating early and broad during the design process is widely recognized as a way forward. However, implementing this with legacy, desktop-based simulation setups is quite challenging. The difficulties arise from the complexity of globally distributed teams, the use of different hardware levels, multiple CAD systems, and the need to account for a wide range of physics and processes, especially in industrial equipment. A cloud-native simulation platform like SimScale resolves these issues, making it practical for engineering teams to conduct early and broad simulations.
Furthermore, in today’s environmentally conscious market, sustainable manufacturing practices are not just desirable but necessary. Cloud-native simulation enables companies to optimize designs for energy efficiency and material usage, contributing to greener manufacturing processes. This commitment to sustainability can enhance brand reputation and appeal to environmentally conscious consumers.
Conclusion
Delivering high-quality, reliable products is paramount for industrial equipment manufacturers. By minimizing the risk of field failures and ensuring optimal performance through scalable, fast, and easy-to-use simulation, companies can enhance customer satisfaction and loyalty, driving long-term business growth.
While the industrial equipment industry today faces significant challenges in time, cost, and efficiency, the advent of cloud-native simulation from SimScale offers a powerful solution to these problems. Companies can streamline their development processes, reduce costs, and improve overall efficiency by embracing cloud-native simulation, positioning themselves for greater competitiveness and success in a fast-paced market of rapidly evolving and ever-growing demand.