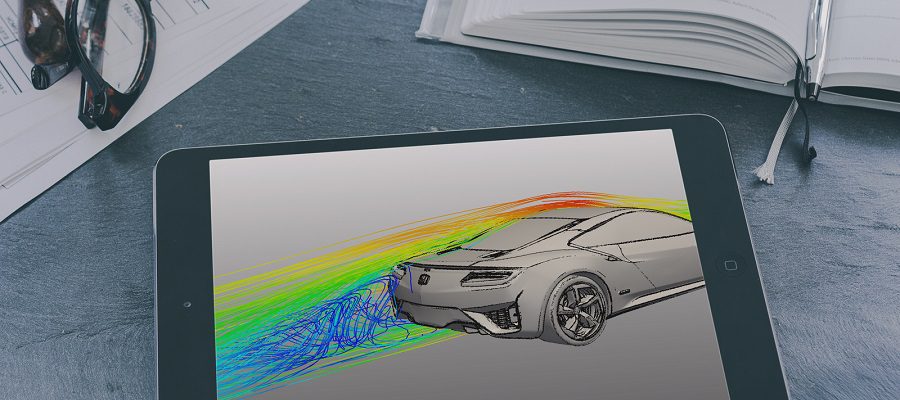
IoT, design thinking, Industry 4.0—with an ever-increasing vocabulary of buzzwords being thrown around and the meaning behind them becoming more and more diluted, it is often overlooked how those concepts should be applied when it comes to engineering and industrial design. At the same time, outdated practices and judgment errors persist. The reality is that, despite all recent technological advancements and improvements, very few of them actually make it into the manufacturing workflow.
Let’s take a look at industrial design beyond the popular concepts and consider what best practices can be derived from them.
The Evolution of Industrial Design Tools
Industrial design broadly refers to the creation of products intended for mass-consumption by millions of people. And today, more so than ever, companies are facing constant pressure to create new and innovative products. In this process, industrial design is the key component. It is estimated that approximately 70 percent of the life cycle costs of a product is determined during the design stage [1]. Elegant industrial design improves product quality, reduces manufacturing costs and time to market, and ensures the overall competitiveness of the product. Such design takes into account both form and function and views the product in the context of the intended user as well as the environment.
In the recent past, resources at the designer’s disposal were very limited and the common tools were the good old pen and paper. The robustness and reliability of the final design would depend on the number of prototypes the company could afford to test and thus limited by the budget allocated to the development of the product. The development cycle was consequently very long and expensive, and the new product launch was always to a certain extent a gamble, with many products revealing unforeseen flaws and delivering disappointing performance.
The emergence of computer-aided design and computer-aided engineering solutions has the potential to completely revolutionize the industrial design process, yet these solutions’ impact has been limited. Due to the extreme complexity of the multiphysics dynamics involved, as well as the high hardware and software costs, the adoption of these solutions has been slow, and many smaller companies still use the conventional “trial and error” method. While CAD solutions have been showing signs of democratization, CAE has remained the privilege of big corporations with massive budgets.
Despite the active discussion on ways to optimize industrial design processes, in both academic and corporate environments, little has challenged the status quo for small and medium manufacturers. So what are the do’s and don’ts of industrial design in light of these recent developments?
SimScale’s CEO David Heiny tests the capabilities of the platform to solve a real-life engineering problem. Fill in the form and watch this free webinar to learn more!
Abandon the “Move Fast and Break Things” Mantra

This has been the modus operandi for many modern startups, as well as some established companies. This view of design—getting a minimally viable product to market as fast as possible and following it up with continuous tinkering—may be sensible for software manufacturers, but it often fails when applied to industrial design. Unlike a smartphone app, a hardware product cannot be patched or updated, so it needs to be fool proof before being shipped to the consumer, to avoid mass recalls or (in extreme cases) even lawsuits. Bigger companies can fall prey to that mentality as well—the most recent and prominent example being the overheating and exploding batteries of Samsung Galaxy Note 7. The company was forced to make massive recalls and eventually stop the production of the phone, suffering considerable losses. Many public businesses, as well as airlines, banned the product, severely damaging Samsung’s reputation. That might have been avoided if the design validation and the testing process had been more vigorous.
Integrate Computer-Aided Solutions Early in the Design Process

Some design issues may be obvious. Others may be more elusive. Yet, as the case of Samsung demonstrates, design problems can affect product performance in a major way when tested in a real life environment. This is where design and simulation software comes into the industrial design process. Computer-aided design (CAD) and computer-aided engineering (CAE) have evolved into powerful tools that empower engineers to identify design flaws and deliver better, more reliable products more efficiently. CAD and CAE solutions help narrow design options, identify flaws and potential problems early on and validate the final design, consequently saving a considerable amount of time and money, as well as protecting the company’s reputation. It is not surprising that the new safety protocols adopted by Samsung to prevent the problem in the future involve performing simulations that imitate accelerated consumer use cases under a wide range of operating conditions [2].
Make the Shift to the Cloud
One of the main sources of trepidation and skepticism about adopting CAD or CAE solutions are the high software and hardware costs typically associated with traditional on-premises software. Many smaller companies that have never employed simulation in their industrial design process are naturally intimidated by such investment requirements with unclear returns. That dilemma can be avoided with the emergence of cloud-based solutions. Engineers have the option of accessing the required computing power remotely from a simple laptop and scaling the capacity as needed. Platforms like Onshape (CAD) and SimScale (CAE) are among the pioneers in the field of cloud-based solutions. To further lower the adoption barriers and make the transition easier, SimScale has introduced its Community Plan, granting access to the full functionalities of its platform to everyone, free of charge. Still, the traditional on-premises software has established itself as the industry standard in both universities and companies, thus the status quo is slow to be challenged.
Conclusion
Despite growing evidence supporting the benefits of integrating computer-aided solutions into the industrial design process, the awareness and adoption rates remain low. According to the Worldwide CAD (Computer Aided Design) Trends 2016 Survey, current usage of 3D Modelling, 2D Drafting, and Simulation CAE solutions is at 76%, 68%, and 34% respectively. The numbers are even lower for cloud-based solutions—partly caused by the status quo bias, but mainly due to a simple lack of awareness. Yet it is clear that as engineering simulation is becoming more and more democratized, a growing number of designers will benefit from it. SimScale aims to contribute to this democratization process by offering engineers an easy-to-use cloud-based platform accessible from any browser, rapidly create a free account, and test it by using one of the hundreds of simulation projects available in the SimScale Project Library.
This free infographic illustrates how architects and engineers can use CFD to virtually test and optimize building designs and HVAC systems. Download it for free.
References
- Improving Engineering Design: Designing for Competitive Advantage, National Academies Press
- This Is Samsung Plan To End its Exploding Smartphone Problem, Time.com