Gap fillers can outperform thermal pads in battery pack applications in terms of lower thermal impedance, as gap fillers conform to surface roughness before curing. What’s more, different materials can result in different mechanical performances. With simulation, engineers can investigate and post-process many aspects of thermomechanical design from casing stresses to pouch cell swelling and the impact on performance caused by drastic temperature gradients inside of the cells.
Case Study: Electric Vehicle Battery
In this case study, battery design is investigated both in terms of thermal management and mechanical performance. This project requires that we assess a battery pack assembly, which contains a couple of cooling plates, pouch cells, insulator pads, and gap filler material.
Geometry & Problem
For this project, we used a 3D solid body geometry. Any tool can be used to generate such a solid body model and then can be uploaded to SimScale.
Simulation Model
After CAD import, simulations require meshing. In this case study, we used automatic meshing.
Physics
In this case study, we conducted a thermomechanical analysis, which allows us to bring thermal stresses into a conduction-based simulation.
Solve
Our cloud-native solution gives us the ability to identify the temperature hot spots as well as the peak mechanical stresses and deformations to understand how our module is performing both thermally, as well as mechanically.
EV Battery Pack Gap Fillers: Project Scope
The model is a lithium-ion battery pack for electric vehicles that consists of four modules. We have two water cooling plates on the top and bottom of the battery module with the gap filler material separating the cooling plates from the pouch cells and the casing itself.
Gap fillers are critical for thermal management for a number of reasons:
- They provide electric insulation
- They provide vibration damping
- They have the ability to conduct the heat across the interface between the battery packs and the cooling plates
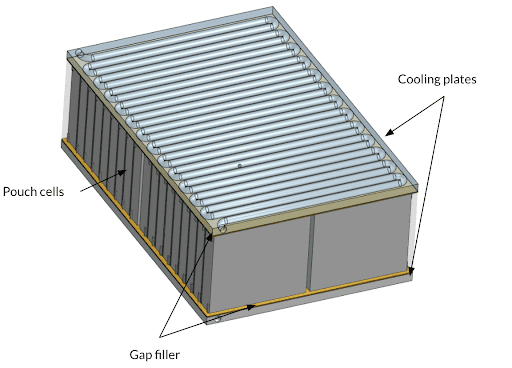
We want to make sure we utilize the maximum cooling capacity of our cooling plates by selecting the most efficient gap filler material for the model. Additionally, we want to focus not only on optimizing the gap filler selection but also on determining the best thickness of the gap filler.
Gap Filler Materials
The first step of the study is to simulations with three different gap filler materials, each with the same thickness. Each material has a different conductivity value. We want to investigate the effect of using different gap-filling materials, in terms of the maximum cell temperatures that are observed inside the pouch cells. Additionally, we want to detect the amount of mechanical swelling that can take place due to the temperature in the pouch cells. Increased conductivity results in reduced maximum cell temperature, however, change in conductivity had a minor effect on our study, since the dominant impact on reducing temperature was provided by the water cooling plates. Even these minor effects are valuable to note in the early-design stage, however, as the material selection impacts cost in manufacturing.
If we have the optimal selection of gap filler material, we can select the most efficient or least energy-intensive cooling apparatus on the cooling side of the battery cells. Also, the pouch cell principal strain decreases, which is an indication of the actual volumetric swelling of those cells. We can see that we have a higher peak temperature on the left-hand side where we have the gap filler material with low conductivity; when we go over to a high conductivity material, we have both lower temperatures and more uniform temperature distribution as well, critical for battery design. We want to make sure that our cooling capacity is being utilized across the whole module uniformly to avoid cold spots and hot spots. In another cutting plane on the gap filler materials, we see the same trend.
Gap Filler Thickness
We can use SimScale to optimize the thickness of the battery pack gap filler material, as well. Simulation can help us understand the bearing that gap filler thickness has on the actual temperature distributions and thus predict and manage the mechanical thermal strains within the system. As we increase the thickness of the gap filler material, we see the reverse effect. With a thicker gap filler material, we have a higher pouch cell temperature. That is because we are reducing the effectiveness of the water cooling plates. We are trying to keep the gap filler material as thin as possible, but while still allowing the gap filler material to serve for vibration damping and insulation, as well. Simulation gives engineers the ability to navigate this balancing act. With thermomechanical analysis, we can investigate these physical behaviors and understand what is causing the hot spots, swelling, etc. and test the best way to mitigate them.
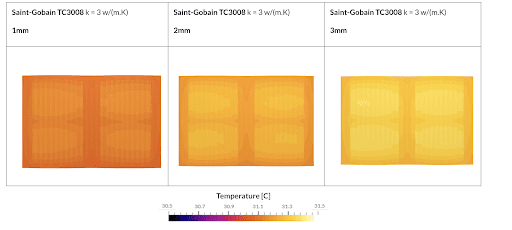
Mechanical Performance
Finally, we can assess the mechanical performance from the same simulation. Looking at the lowest conductivity gap filler material set at the lowest thickness, we can see the actual mechanical stress in the steel casing around the battery model itself. Here, we observe maximum mechanical stress to the point of yielding at that joint section. So, in those regions where we have significant stress, we could expect to see some damage and plastic deformation. This asks us to consider resizing the casing thickness or maybe use a more ductile material for the casing, in order to reduce those stresses and increase the lifetime of the product. If we want to go into further detail, beyond a linear static analysis that identifies the areas above yield stress, we can convert this into a non-linear simulation. This will allow us to see the absolute maximum stresses that we would experience during the thermal cycling of the battery module. The same goes for the total strain in the pouch cell. We have roughly 1 to 2 percent of total strain magnitude in the pouch cells due to thermal behavior.
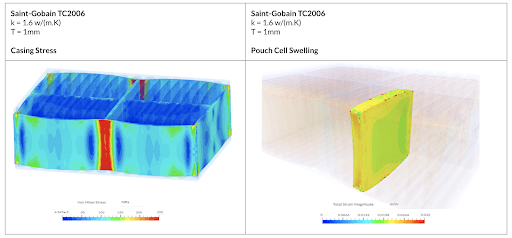
Maintaining battery packs within a specific temperature range is essential for ensuring the performance of the product and the safety of users. With cloud-native engineering simulation, you have the ability to run multiple design iterations in parallel means that simulating a battery pack module from CAD preparation to post-processing can be performed with fast turnaround times.