In the 1970s, before the widespread adoption of computers, long before anyone could differentiate the cloud from an ordinary cloud in the sky, and the term cloud collaboration was nonexistent, something pretty incredible happened in the way of product development and design process optimization. During this time, the automotive industry was booming, with Ford Motors as a clear front runner, until all of a sudden Toyota began to overtake them, becoming (and still holding their spot today as) the world’s largest automaker.
Now you may be asking yourself, what does this anecdote about automotive giants have to do with improving my design process? Well, hang in there, because a lot. Toyota was successfully able to overtake Ford for one main reason; their innovative process.
How They Did It: Optimized Design Process
The Toyota Production System (TPS) developed and employed by Toyota evaluated the workflows of their competitors, acknowledged the value additions and resource-wasting factors, and adapted their own existing management style to be even better. For example, they were able to bring their vehicles to market twice as fast as any other car manufacturer and did this with 25% fewer engineers per car; saving time and money. Toyota revolutionized waste elimination and performance enhancement in the car manufacturing world, and it all came down to the cutting-edge design process employed.
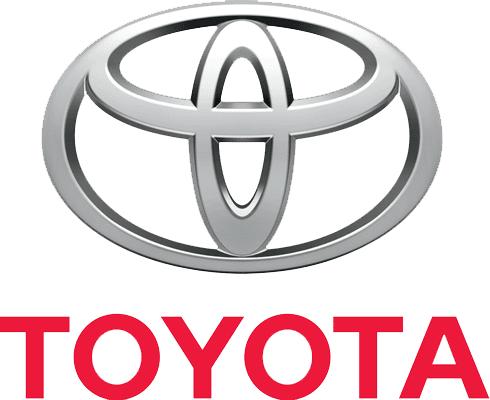
Today, companies large, small, far, and wide across the globe try to emulate Toyota’s success in their own industries, and can also benefit from the assistance of increasingly accessible technological tools at hand. However, the playing field for gaining a competitive advantage has indeed become more saturated, and therefore more difficult to gain any advancement even with a plethora of tools for the taking. Additionally, if you take into consideration the current global pandemic, this situation has become even more exacerbated.
In this article, we will provide tips that have helped us bring ideas to fruition here at SimScale by presenting five ways to enhance and speed up your early design process, to ultimately optimize your overall processes for greatness.
No longer can engineering teams be bound by project silos, time zones, or physical locations to meet demanding deadlines. So how can engineers use this to their advantage?
Tip One: Use Tools to Tackle Time Management
In today’s fast-paced world, time management is one of the hardest things to keep under control. This is because of the simple fact that managing time is closely related to managing the expectations of others—which at the same time, are increasing more than ever before. In a recent study from Salesforce, 76% of customers expect companies they are working with or looking to work with to not only know, but to understand their needs and expectations implicitly. Unless you’re a mind reader, this is nearly impossible to be successful at achieving 100% of the time.
So as business keeps booming coupled with growing expectations, where is the downside? What doesn’t change? It’s simple, the number of hours you have in your day. So how can we possibly remedy this situation? By trying to search for, choose, and utilize the best tool on the market that suits our specific business needs.
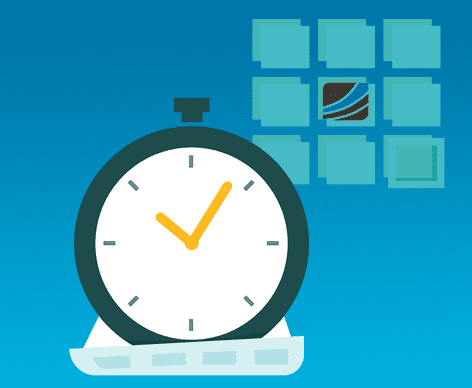
Designers and engineers alike need to set aside time to make sure they are keeping up to date with the latest technology trends. From new applications, plugins, software, as well as new organization tactics and any means that help to facilitate this. Let’s look at a key business component to illustrate our point; digital presence. For example, when it comes to creating your company’s website, used to market both the company brand and product, WordPress is probably the biggest player in the game. WordPress alone powers about 27% of all websites and holds about 76% of the global CMS market share.
Why does it continue to be the leader in web development and design year after year? Because not only does the product meet the needs of a wide range of users (from beginners to professionals), but WordPress constantly adapts to new needs and trends, boasting thousands of plugins so users can customize to fit their workflow.
In other words, they are pros at managing the expectations of their customers, while also facilitating the expectation management of their customers’ customers. Design and CMS tools like WordPress can come in very handy for saving effort and headache, allowing you to adapt to how your business needs change, ultimately benefiting your time management.
More Time-Saving Design Tools to Check Out
- InVision Studio: This powerful UI tool figures out if you prefer UI at the beginning or end of your design process, and then adheres to your workflow.
- ProofHub: This design editing and proofing tool allows teams to easily pass messages regarding the changes required, such as adding color to the design, text positioning, etc. It also eliminates the need for emails and meet-ups throughout the web design project, reducing the time for completing the project.
Tip Two: Try New Technologies of the Trade
Much like the design solutions of the trade, engineering tools are also being created and made public at an increasing rate. Computer-aided engineering (CAE) software, also referred to as simulation software, supports engineering analysis tasks. CAE software encompasses finite element analysis (FEA), computational fluid dynamics (CFD), multibody dynamics (MDB), and optimization capabilities.
CAE software enables users to simulate, validate, and optimize designs and must:
- Enable users to create product and structure simulations through a graphical user interface (GUI)
- Allow users to test and verify components of a simulation with customizable environmental variables
- Help users optimize a process or product development
Time-Saving CAE Software Solutions to Check Out
In 2020, the top 10 CAE software was listed on G2, a site that compares best business software and services based on user ratings and social data. The top includes names like MATLAB, SimScale, and Fusion 360.
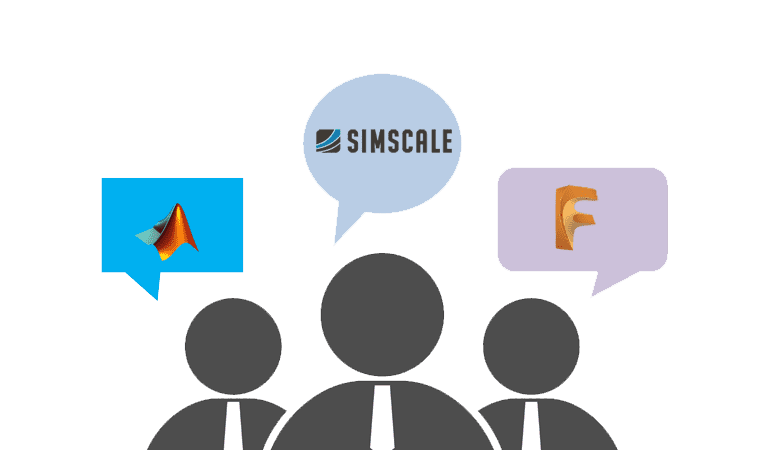
Yet, while you might be happily using one of the above tools for current or even newer quarterly business goals, it doesn’t hurt to always be looking at what other solutions are available. For example, while Fusion 360 is a handy CAD-CAE integrated application that allows users to design and simulate in the same environment, it might not actually fit the needs of your business, depending on the required features.
In 2016, SimScale actually introduced a Fusion plugin to our platform, so that users could create their CAD or project on Fusion and then import it into SimScale for evaluation, despite having simulation features available in Fusion already. All and all, the main message is to keep up-to-date with what is out there, what is changing or optimizing, and what you need in a tool to meet your ever-changing and expanding business needs.
This paper addresses the difference between on-premises software and SaaS
solutions for computer-aided engineering, explaining how SaaS came to be and its
key benefits.
Tip Three: Patch-Up or Part With Your Existing Processes
The next tip follows the first two pieces of advice quite nicely. As new tools are released all the time, there is a great opportunity to rethink and refurbish your in-place processes.
Sadly, although this may be true, I think many can agree that amidst all the hustle and bustle of an average work day, week, month, year… this is often forgotten. Most of us subconsciously operate with the ‘if it ain’t broke, don’t fix it’ mindset, hurried and focusing on the most urgent thing. So let this be a gentle reminder to look back upon how you’ve been operating.
Pick Apart Your Process
Jumping back to our introductory example, let’s revisit Toyota. The initial part of the automotive development process can be deemed the heaviest. This is because the early design phase must consider, identify, and resolve all problems that could potentially occur. When you begin brainstorming ‘what if’s’, there is an innately complex and comprehensive task at hand. So what were their steps to shorten the time frame to solve?
Pick Up the Pieces
In order to build a consensus quickly, they utilized a three-pronged approach. Before thinking about what could possibly go wrong, Toyota created cross-functional product development teams to determine the specific and technical requirements. This pioneering agile method benefits from various team members from several corners of the business coming together to express different points of view, sources of knowledge, and expertise that can be then banded together towards one goal.
Next, they employed a product development framework to keep employees on track. Finally, the company’s overarching focus on meeting current customer needs also worked in their favor. These three guiding forces worked together to create the shortest time-to-market—from design drawings to open road acceleration—the world had ever seen. What would have happened if Toyota had just followed suit with its American competitors, using the same tried and tested process? The world will never know.
Design Process Made Perfect
From this example, a few things can be learned when it comes to process improvement. The first is that it will always benefit you to scrutinize the status quo or day to day operation at your business; from finding no room for improvement to a lot, positive and actionable outcomes always follow. Next, a cross-functional team approach can be a great way to save time and facilitate collaboration, by getting people from different fields to work with a product altogether.
Lastly, an ever-present reminder of your company’s mission, and why you and your employees come to work each day, should be an interlaced motif throughout all of these activities. At SimScale, we define this within our quarterly OKRs that we refer back upon throughout. Sometimes our overall goal and objective can get away from us, and having our desired customer commitment written and accessible at all times does help put things in perspective.
If you find that you struggle with changing your process: get out of your comfort zone and don’t be afraid of altering the way things are completed. At the end of the day, the work will get done. It may take you a few hours to learn and to get used to a new way of doing it, but it will save weeks of work in the future.
Tip Four: Don’t Multitask, Manage Tasks Better
Although this tip sounds quite obvious, we find that a lot of teams (including our own) can sometimes get caught up in one task. This isn’t always a bad thing, and sometimes needed for different cases. Yet, you’ve also probably experienced the drawbacks of having ‘too many cooks in the kitchen’, or too many people inputting and trying to solve one problem.
Why Multitasking Doesn’t Work
On the other hand, one person trying to do the job of too many also has its drawbacks. This results in multitasking, or the perceived human ability to perform and complete multiple tasks at once. In fact, some researchers suggest that multitasking can actually reduce productivity by as much as 40%. One study found that, on a larger scale, only 2.5% of people are actually able to multitask effectively. At SimScale, we currently have around 80 employees. This effectively means that two of our employees can multitask, while the rest of us are lying to ourselves as we try to; that doesn’t sound very effective!
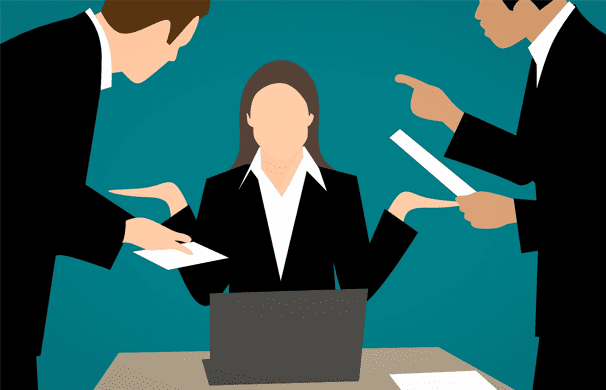
So now that we’ve established that multitasking isn’t a legitimate task management solution, how do we carry on? We can’t possibly relay to customers that work is delayed because of our genetic predisposition as a species. If multitasking seems to be taking over, the best thing businesses can do is to refrain from panicking to work more or faster to overcome this, but to instead work smarter and spread the load.
How to Multi-Manage Tasks in the Design Process
Some companies have even built themselves upon solving this essential issue (and hats off to them for capitalizing on nothing more than the human condition). For example, US-based Rockwell Automation provides industrial automation and information technology to its customers through mechatronics.
Mechatronics is the collaboration, if you will, of precision mechanical engineering, electronic control, and systems thinking in the design of products and manufacturing processes. This multidiscipline design approach not only helps its customers by managing tasks quicker, but does so through a collaborative application of motion design software and products; Mechanical, electrical, and control engineers working in parallel helps develop optimized machines more quickly.
How to Manage Tasks Through The Cloud and Cloud Collaboration
At SimScale, users and engineering teams alike can also benefit from working in parallel, through the paralleled running and processing of simulations. Customers from around the globe have experienced the time-saving benefits of this functionality, and explained their experience; like the following example:
“One other big factor is the speed in which SimScale can deliver results, through its great parallelization capacity. Without SimScale, we wouldn’t be able to deliver high-quality results in the required time period.” – David Akeret, Gruner Roschi AG, VDC Specialist
Read more about Gruner Roschi AG’s experience here.
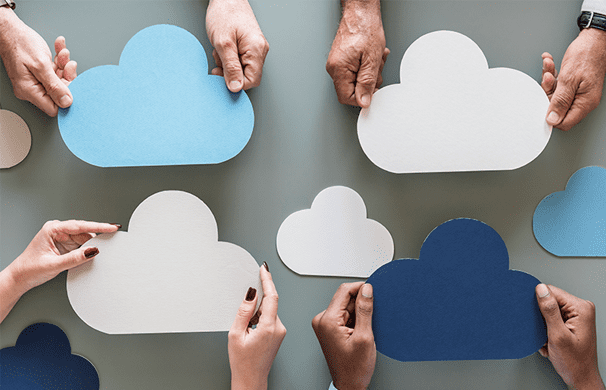
How is this made possible? Through harnessing the power of the cloud. The cloud, as well as cloud collaboration capabilities, increasingly contributes to effective task management across all professional disciplines. There is a reason why Forbes began tracking the top 100 cloud companies four years ago; cloud-based is becoming, if not already, the new normal. This annual update includes top companies that are “transforming how we communicate and collaborate at work”.
Tip Five: Create through Collaboration
As touched upon in the first two tips, platforms and tools with collaboration features are big time savers for large and small teams alike for any design process. Yet, even though the concepts of teamwork communication are instilled in us from a young age, you would be surprised to find out that, statistically speaking, failure in these respects is the biggest cause of waste in global business.
This comes down to the simple fact that not everyone has the same understanding of the aforementioned terms, and what collaboration means. Workplace collaboration aims to evenly distribute workload, keep team members from getting individually overwhelmed, and effectively harness the best out of each person. A common mistake made here is the assumption that collaboration will just naturally occur in the office. While we wait with bated breath for that to happen, next to our tree that should start growing money, other companies make this a priority by implementing cloud collaboration technology.
What Are Cloud Collaboration Tools?
Cloud-based collaboration tools enable and allow employees to access data from any location, facilitating collaboration on a common and familiar platform. For example, cloud-based project management software like ProofHub, Wrike, Clarizen, etc. allow teams to share files simultaneously, communicate in real-time, and have an interactive collaboration, bringing out more creativity. Cloud collaboration functionality isn’t limited to project or task management software, and is also very popular for anything from video conferencing software like Zoom to CAE platforms like SimScale.
How Do We Provide Collaboration Tools for Our Customers?
At SimScale, cloud collaboration features are available along with a multi-user licensing package to support design, engineering, and architecture teams with many people who utilize simulation in medium and large companies. SimScale is the first and only tool in the CAE market with cloud collaboration functionality. The cloud-based platform and public project library houses a collaborative community of over 200K users worldwide that can access, copy, and share projects, yet this only comes as a benefit to singular users, consultants, and students. So how does SimScale facilitate collaboration between professional teams that need to work together, from the same project, and iterate as quickly as possible?
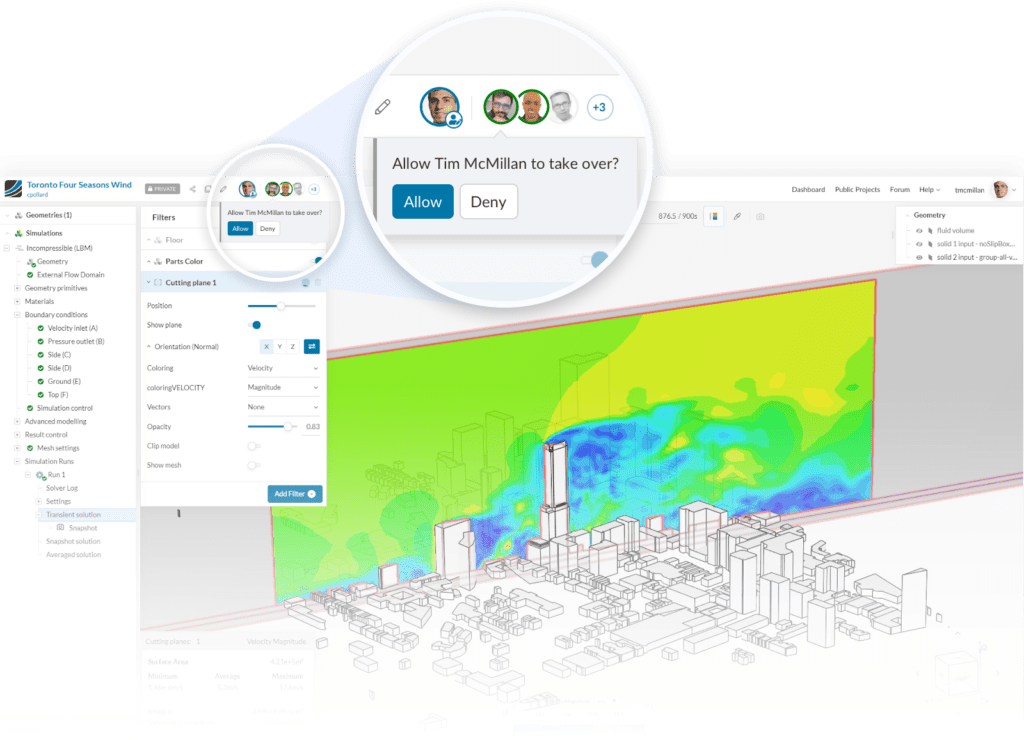
In order to meet the needs of engineering and architecture teams with multiple people who additionally need collaboration abilities, SimScale unveiled collaboration features that you can read more about here.
How Does Cloud Collaboration Improve the Design Process?
In short, multiple users can work simultaneously from any location, eradicating the need to copy projects and start over from scratch. Simulations will all be able to be kept within one project, instead of having multiple projects for the same application. Moreover, team members can share knowledge and know-how more quickly, even in remote work set-ups, as different members can access the same project in real-time. All of this, managed through a dashboard that can display computing usage overview and more, enables engineering teams to accomplish tasks more collaboratively than ever before.
Across virtually any industry, collaboration is the final product of interactive creation and an integral part of the design process. This can be achieved through:
- System feedback loops
- Visibility and transparency across the business
- Defined ownership for different project or process attributes
- Consistent, constant, and controlled communication
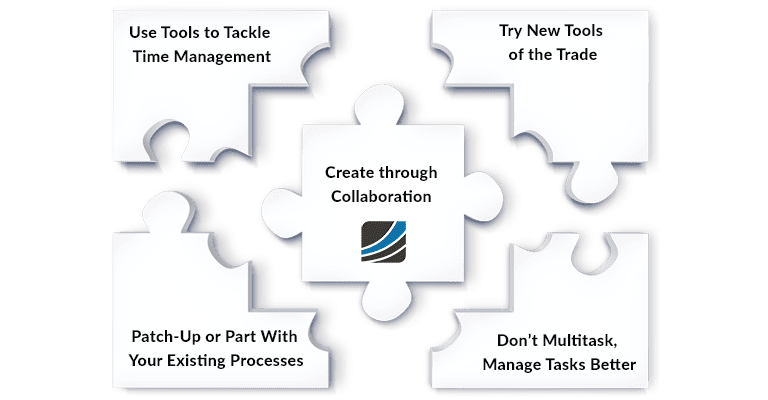
Collaboration is the final piece of the design process puzzle that you couldn’t find at first because it was hiding under the chair, the secret ingredient used for the McDonald’s Big Mac; it’s a small part of the big picture but makes the biggest difference. As Henry Ford once said, “Coming together is a beginning, keeping together is progress; working together is a success”. Did he say this before or after Toyota’s redefinition of success took away the lion share of the automotive market? It’s hard to be sure, but the sentiment is inspiring nonetheless.
#teamworkmakesthedreamwork