In industries like aerospace and energy, even a minor flaw can mean costly delays or equipment failures. This applies to axial compressor design, a core element in engineering workflows for these sectors. Precision is everything: from blade geometry to stage configurations, engineers face the constant challenge of achieving high efficiency and optimal pressure ratios under unpredictable conditions. Yet, the path to these goals isn’t straightforward. Managing compressible flow dynamics and transient behavior is essential to prevent flow instabilities and losses that can derail performance. With tight schedules and high stakes, engineers must balance efficiency, mechanical integrity, and rapid innovation, a task made easier with advanced simulation tools.
Traditional axial compressor design methods often involve a combination of physical prototyping, simulations, and extensive testing. While these approaches can provide valuable insights, they can be time-consuming and costly, especially when dealing with complex geometries and operating conditions. Physical prototyping, in particular, can be a significant bottleneck, as it requires manufacturing and testing of actual hardware. Traditional simulation tools, while powerful, can be resource-intensive and require specialized expertise and hardware to set up and analyze.
That’s where a modern engineering simulation platform becomes essential in axial compressor design. SimScale has transformed how engineers analyze, optimize, and validate their work. By simulating fluid flow, heat transfer, vibration, and mechanical stress all in SimScale’s AI-powered cloud-native simulation platform, engineers can refine their designs faster and catch potential problems early. This means engineers and designers can iterate quickly, minimize costly physical testing, and speed up their design process significantly.
In this article, we will discuss how simulation is transforming axial compressor design and explore how SimScale’s advanced features streamline the process for engineers, enhancing both speed and accuracy.
Axial Flow Compressor Characteristics
Axial flow compressors work by accelerating air through rotating blades (rotors) and then converting this increased velocity into pressure using stationary blades (stators) arranged in multiple stages. Each stage achieves a small pressure increase, which, when combined over multiple stages, enables high overall pressure ratios suitable for various applications. Increasing the number of stages and achieving higher pressure ratios narrows the operational margin between the compressor’s surge and choke limits [1].
The design requirements for axial flow compressors vary significantly based on the application. For instance, industrial compressors often prioritize efficiency and durability, while aerospace compressors are designed for high-pressure ratios and performance under transonic conditions. Research compressors may operate in supersonic regimes, pushing the boundaries of pressure ratios and efficiency to explore new engineering possibilities. The table below outlines typical characteristics of axial flow compressors for different applications, including flow type, Mach number, pressure ratio per stage, and efficiency [2].
Type of Application | Type of Flow | Inlet Relative Velocity Mach Number | Pressure Ratio per Stage | Efficiency per Stage |
---|---|---|---|---|
Industrial | Subsonic | 0.4–0.8 | 1.05–1.2 | 88–92% |
Aerospace | Transonic | 0.7–1.1 | 1.15–1.6 | 80–85% |
Why Simulation is Crucial in Axial Compressor Design
Designing an axial compressor involves managing multiple complexities, including optimizing pressure ratios, reducing aerodynamic losses, and ensuring mechanical integrity. These machines operate in dynamic environments where the interaction between rotating components and fluid flow is highly unsteady, making it challenging to predict performance accurately using traditional methods.
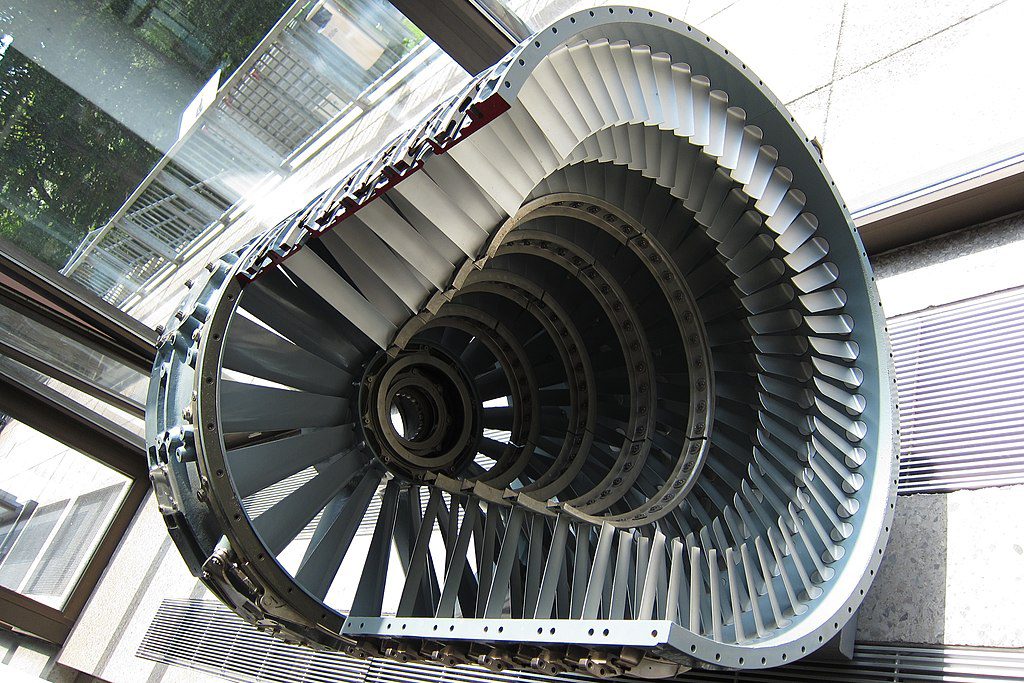

Engineers must account for issues like turbulence, cavitation, and pressure fluctuations, which heavily impact the compressor’s efficiency and reliability. Aerodynamic instabilities, such as rotating stall and surge, can lead to performance reductions, increased vibrations, and induced low-frequency instabilities, eventually causing mechanical failure. These phenomena require precise modeling to minimize efficiency losses and reduce the need for conservative safety margins that would otherwise limit efficiency and over-dimensions the system.
Multi-objective optimization techniques can enhance efficiency by reducing low-velocity separation zones and improving stall margins [4]. Similarly, advanced numerical simulation helps balance high-efficiency, high-pressure ratio, and surge margin goals through precise parameterization, which is otherwise difficult to achieve with physical prototyping alone [5].
Building and testing physical prototypes often requires multiple iterations, with each new prototype taking substantial time and resources to develop. This approach delays time-to-market and restricts the ability to explore innovative design concepts. Additionally, physical testing alone may not offer the detailed insights needed to fully understand fluid dynamics, pressure behavior, or mechanical wear, especially when compressors operate close to the surge line. Axial compressors are more sensitive to operating conditions compared to their centrifugal counterparts, making it crucial to ensure they operate within optimal parameters to avoid issues like surges, which can significantly impact performance and reliability.
For instance, an engineer might face fluctuations in RPM during real-world testing, requiring hours or even days to gather enough data on the effect on performance. Traditionally, this means relying on test beds and, often, a lengthy process of retrofitting designs on the fly. By contrast, SimScale enables engineers to generate a comprehensive performance map in minutes, offering a rapid overview of how different RPM levels impact compressor behavior. This allows for precise adjustments early in the design phase, saving time, cutting costs, and reducing the risk of performance issues later on.
SimScale’s cloud-native simulation further enhances the design process by offering scalable resources, automating workflows, and enabling rapid, parallel testing of multiple configurations. This cloud-based infrastructure allows engineers to streamline simulations without the need for on-premises hardware, making high-fidelity simulations accessible and cost-effective. With AI-driven capabilities, engineers can accelerate iterations even more and optimize design spaces, uncovering deeper insights into complex flow behaviors and generating predictive insights with reduced need for full simulations. This combination of cloud scalability and AI-powered analytics shortens time-to-market, reduces project costs, and helps engineers achieve performance targets faster than with traditional methods.
SimScale for Axial Compressor Design
1. Fluid Flow and Heat Transfer Analysis
The SimScale Multi-purpose CFD solver is designed to handle complex fluid dynamics, which is critical for optimizing axial compressor efficiency, pressure ratios, and overall performance. Leveraging a finite volume-based approach, this solver uses a proprietary variant of the SIMPLE algorithm to solve the Navier–Stokes equations, making it well-suited for analyzing compressible flow within axial compressors. These capabilities allow engineers to simulate both laminar and turbulent flow regimes in a single environment, capturing the transient behavior of rotating compressor components with high precision.
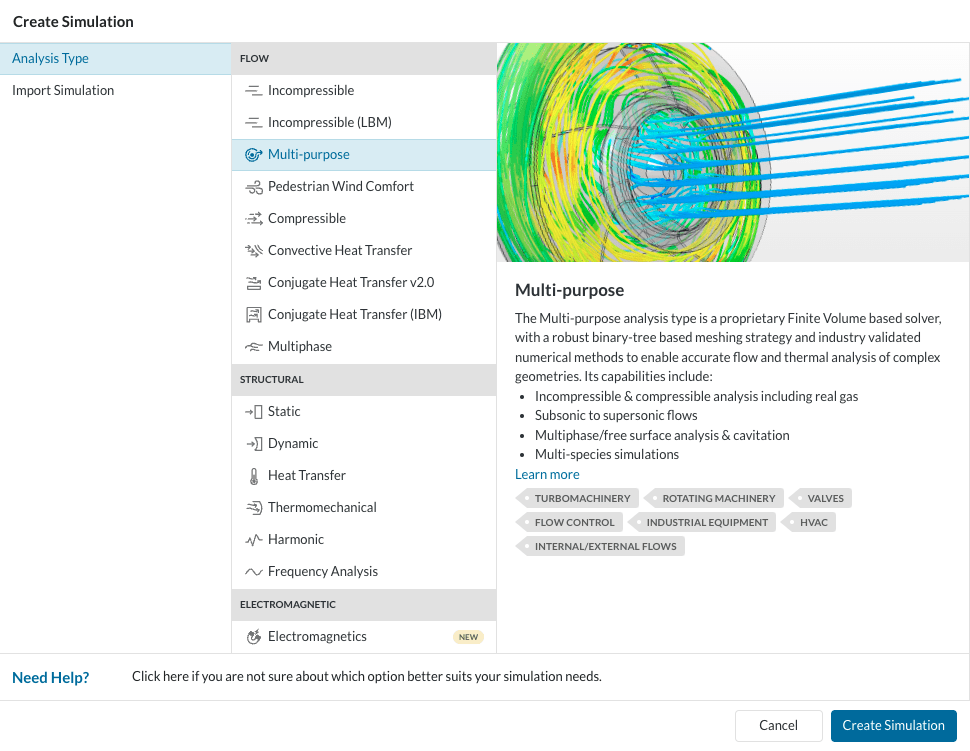
SimScale’s sliding mesh feature enables realistic modeling of interactions between moving blades and fluid, providing detailed insight into pressure and velocity distributions. Engineers can assess compressor maps, surge and choke lines, and overall pressure ratios under different operational conditions. With these tools, you can obtain outputs such as compressor performance maps, temperature fields, and efficiency curves, giving a comprehensive view of thermal and aerodynamic performance early in the design process. This helps reduce simulation lead times, enabling faster iterations and quicker design refinements. With these capabilities, engineers achieve faster, data-backed insights into thermal and aerodynamic performance, streamlining the path to design optimization.
2. Structural Analysis and Vibration Modeling
Beyond fluid flow, SimScale offers robust tools for analyzing the mechanical integrity of axial compressors. The platform’s Rotational Modal Analysis feature, for example, is tailored to compressor design by accounting for centrifugal forces and gyroscopic effects that arise in high-speed rotating machinery. This capability allows engineers to create Campbell diagrams, which map resonant frequencies of rotating components and identify risks of mechanical failure or instability. This is essential for ensuring the mechanical stability of the compressor, especially in high-speed operations where resonance can degrade performance or cause damage.
For compressors operating under extreme conditions, SimScale’s Real Gas Model simulates accurate pressure and temperature variations, ensuring realistic behavior in high-pressure environments. This level of detail is crucial for capturing stress distribution, potential deformations, and the impacts of fluctuating loads on mechanical components. By combining fluid flow and structural analysis, engineers can ensure compressors are designed for both aerodynamic and structural resilience, with accurate data that informs choices to enhance durability and reliability.
Advantages of Using SimScale
SimScale’s cloud-native infrastructure, combined with AI-enhanced simulations, allows engineers to explore larger design spaces with improved accuracy and speed. This approach leads to shorter simulation lead times, the ability to run multiple configurations in parallel, and high-fidelity insights without needing on-premises hardware investment. This cloud-based infrastructure enables scalable simulations that adjust according to project needs, keeping costs predictable.
The Multi-purpose CFD Solver and other advanced tools help engineers run complex simulations quickly while maintaining accuracy. The platform also has the ability to run multiple simulations in parallel, which reduces the time-to-market and accelerates the design process. SimScale also eliminates the need for costly on-premises hardware as it operates on the cloud. This allows engineers to scale their simulations according to project requirements and only pay for the resources they use, making high-fidelity simulation accessible to businesses of all sizes.
SimScale’s interface is designed to be user-friendly, with a wide library of templates and tutorials that simplify the setup of simulations. Automated features such as body-fitted meshing and rotating region creation reduce setup time, making it easier for engineers to perform advanced simulations regardless of experience level. The platform’s seamless integration with CAD tools enables quick updates to design iterations without losing important data, improving workflow efficiency.
SimScale also offers real-time collaboration, enabling teams to work together from any location by sharing simulations and results through a web browser. This improves collaboration and speeds up decision-making, especially for teams spread across different locations. SimScale’s continuous updates ensure engineers have access to the latest tools and features, keeping them up-to-date with advancements in axial compressor design.
With the flexibility to scale simulations and collaborate in real time, SimScale supports streamlined axial compressor design workflows without the need for expensive hardware. By incorporating simulation early and consistently, engineers can develop high-performance axial compressors and other turbomachinery that meet demanding industry requirements, all while reducing costs and time-to-market.
References
- M. P. Boyce, “Case Histories,” in Gas Turbine Engineering Handbook, 4th ed., M. P. Boyce, Ed. Butterworth-Heinemann, 2012, pp. 885-921. doi: 10.1016/B978-0-12-383842-1.00022-6.
- M. P. Boyce, “Axial-Flow Compressors,” in Gas Turbine Engineering Handbook, 4th ed., M. P. Boyce, Ed. Butterworth-Heinemann, 2012, pp. 303-355. doi: 10.1016/B978-0-12-383842-1.00007-X.
- M. P. Boyce, “An Overview of Gas Turbines,” in Gas Turbine Engineering Handbook, 4th ed., M. P. Boyce, Ed. Butterworth-Heinemann, 2012, pp. 3-88. doi: 10.1016/B978-0-12-383842-1.00001-9.
- S. Huang, C. Yang, and P. Wang, “Aerodynamic optimization design and experimental verification of a high-load axial flow compressor,” Journal of Turbomachinery, 2023.
- W. Zhao, J. Chen, Y. Liu, H. Xiang, and B. Li, “Prescreening surrogate-model-assisted multi-objective aerodynamic optimization design of highly loaded axial compressor in heavy-duty gas turbine,” International Journal of Gas Turbine, Propulsion, and Power Systems, 2023.