Vehicle designers, no matter if they specialize in motorsport cars, trucks, common vehicles, or even motorbikes, have to fight every day with an invisible enemy — air resistance. To put it simply, when a body moves, the air around it generates resistance in the opposite direction of the movement. For vehicles, air resistance affects the comfort of the passengers, fuel consumption, stability, and many other performance factors.
Air Resistance Measuring Air Resistance
Source: By TheOtherJesse, Wikimedia CommonsBelow is the drag equation that represents the drag force experienced by a body due to the movement through the air (or any other fluid). It is composed of the density of the fluid
(which we can’t change), the reference area
(the frontal area in the case of cars or motorbikes), the drag coefficient
(defined by the body’s shape), and the flow velocity
(relative to the object)
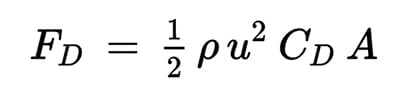
The equation shows that the only parameters the designer can modify are the reference area of the object and the drag coefficient. For automobiles and many other kinds of objects, the reference area is the projected frontal area of the vehicle.
The drag coefficient ranges upwards from 0, and a lower drag coefficient indicates that the vehicle will be less air-resistant, which reduces the drag coefficient and improves the performance of the vehicle as it pertains to speed and fuel efficiency. These are the two values that need to be focused on to reduce the aerodynamic resistance of a vehicle.
SimScale’s CEO David Heiny tests the capabilities of cloud-based simulation to solve an engineering problem. Fill out the form and watch this free webinar recording to learn more!
Air Resistance Design The Evolution of Streamline Vehicle Design
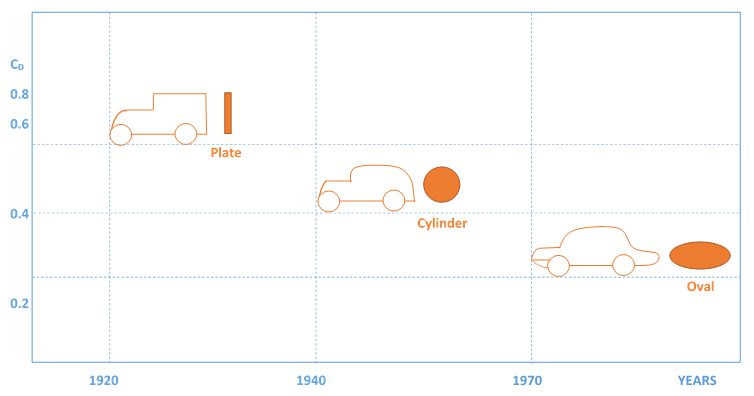
Some decades ago, when nobody studied the aerodynamics of vehicles, their designs were generally rather “boxy,” with angular forms. A lot has changed since then, with car manufacturers steadily improving the aerodynamics in an effort to make each new model more smooth and ‘slippery’ than the one before, allowing air to flow easily around it with the least possible resistance.
Modern vehicle design techniques that help reduce air resistance include, in addition to the smoothness of the overall vehicle shape, recessing the windscreen wipers and door handles, streamlining outside mirrors, eliminating raised gutters around the edges of the roof, and many more — all of which help reduce drag and prevent loss of efficiency.
Wind Tunnels & Air Resistance The Introduction of Wind Tunnels in Vehicle Design
These are still fairly recent developments, however. Before the 1980s, a streamlined vehicle design was restricted to racing and high-end sports cars until the introduction of wind tunnel testing, which brought aerodynamically optimized consumer vehicles to the market. Wind tunnels soon became one of the most important tools to improve vehicle aerodynamics.
In a wind tunnel, the prototype of the vehicle is fixed in place as a stream of air is blown towards it to simulate the airflow that the vehicle would encounter when driven on a real road. The amount of generated drag is then measured to estimate the drag coefficient and assess the overall aerodynamic performance of the vehicle.
Improving Air Resistance Improving Vehicle Design Aerodynamics with Simulation
Physical wind tunnels had been the industry standard for car manufacturers and designers until the introduction of fluid flow simulations with virtual wind tunnels. In addition to the high costs of the initial setup, physical wind tunnel testing is time-consuming and can considerably stretch the product design cycle. On the other hand, computational fluid dynamics (CFD) tools are significantly more efficient and they reduce design costs and time to a great extent while enabling engineers to test their designs under a much larger variety of operating conditions.
To illustrate the application of virtual wind tunnel testing in the external aerodynamic analysis of vehicles, we chose several simulation projects from the SimScale Public Projects Library. Our simulation engineers, along with our active community of users, have performed numerous simulations of vehicle aerodynamics, including trucks, sports cars, futuristic vehicles, F1 cars, FSAE, LMP1 race cars, in addition to airplanes, race bobsleds, and other miscellaneous projects.
In the automotive industry, the most focused application of car aerodynamics optimization can be found in Formula 1. Since the late 60s, F1 engineers have been working on the aerodynamics of their cars with a double target: minimize the aerodynamic resistance and maximize the downforce. To achieve both objectives, engineers have created a lot of different and extravagant solutions. For example, the Brabham BT46B design, which generated a high level of downforce using a fan, not only increased cooling but also extracted air from beneath the car.
Air Resistance Conclusion
Minimizing air resistance and optimizing aerodynamic performance remains one of the key challenges for designers in the car manufacturing industry. It is no longer the exclusive domain of race car engineers and has a real tangible influence on various aspects of the performance of consumer-grade vehicles, including fuel consumption, passenger comfort, and more. However, there is no denying that the emergence of virtual prototyping and simulation tools has made tackling this problem far easier than before. If you want to learn more about how to minimize air resistance using engineering simulation, start a free trial with SimScale and leverage the platform’s CFD functionalities to optimize your own designs.
To learn how to use SimScale, watch the “How to Optimize Race Cars with Cloud-Based CFD” webinar in partnership with Racecar Engineering magazine. Just fill out this short form and it will play automatically.