The automotive industry is a hotbed of innovation and an exceptional testing ground for many emerging technologies. With several trends leading the market and influencing consumer perception and decision-making, automakers are investing hundreds of billions of dollars in new and exciting technologies that promise a transformative future for how vehicles are designed, manufactured, and used. The impact has even trickled upstream and compelled companies at different levels of the supply chain to get in the race, too. Automotive suppliers today are consciously and actively seeking innovative techniques to enhance design, manufacturing, and supply chain processes.
Here are five next-generation engineering technologies that automotive suppliers are adopting to keep pace with the dynamic scene of the industry:
- Generative AI
- Simulation-Driven Design
- Additive Manufacturing (3D Printing)
- Autonomous Vehicles
- Digital Twin Technology
These are certainly not the only technologies influencing the automotive industry. In the last section of this article, we look at some honorary mentions that are also expected to impact automotive suppliers’ workflows and processes significantly.
Let’s dive into the top 5 technologies empowering automotive suppliers today.
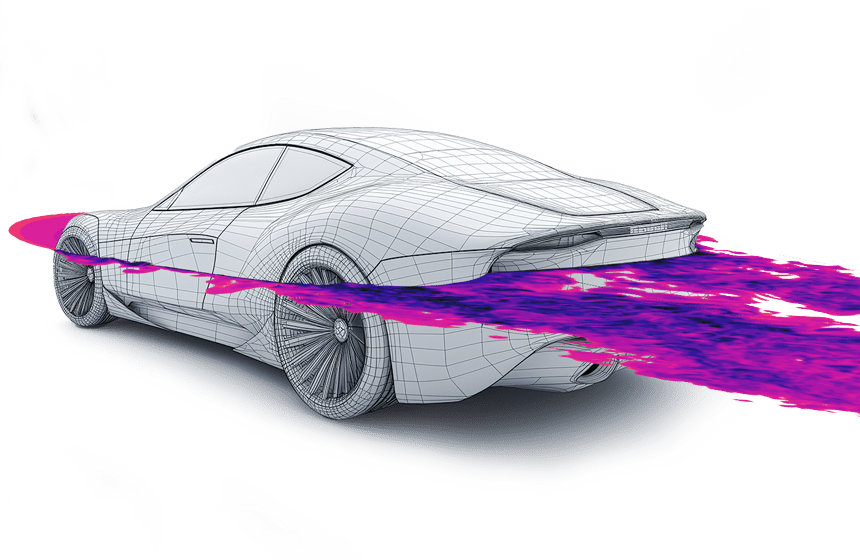
1. Generative AI
Generative AI, also known as generative design, has gotten off to a quick start, with people calling it the next big thing and discussing its influence on increasing productivity, enabling technical automation, and accelerating innovation. Gartner has placed Gen AI at the peak of inflated expectations in its hype cycle report of 2023, projecting its revolutionary impact in the next 2-5 years. Similarly, McKinsey and Co. estimates that Gen AI will compete with the average human worker by 2030 and with the top 25% of workers before 2040 – that is as many as 40 years earlier than previously predicted, and that is crossing the boundaries of industries. Gartner also mentions two sides to the Gen AI movement: Innovations that will be fueled by Gen AI and innovations that will fuel advances in Gen AI.
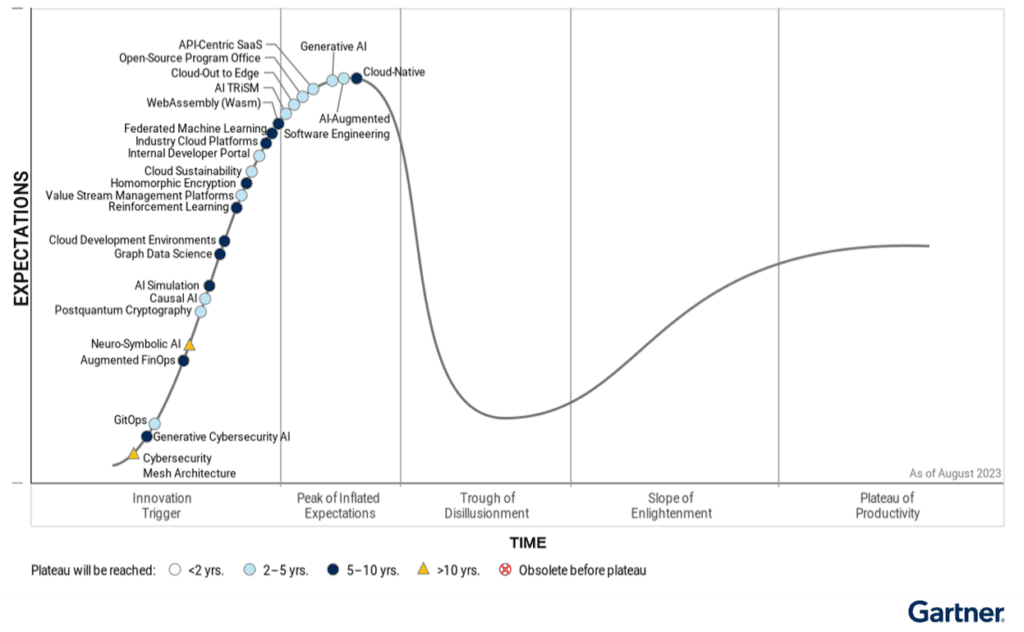
On the automotive front, Gen AI is expected to revolutionize how automotive engineers approach product development. By leveraging machine learning algorithms, generative AI enables engineers to explore a vast array of design possibilities and automatically generate optimized solutions based on specified criteria and constraints. Gen AI works by iteratively generating, evaluating, and refining design alternatives to achieve desired objectives, such as weight reduction, structural integrity, or aerodynamic performance. This approach allows engineers to rapidly explore design variations that may not be immediately obvious or feasible using traditional methods.
One of the key advantages of Gen AI is its ability to uncover novel and unconventional design solutions. By breaking free from preconceived notions and exploring the entire design space, engineers can discover innovative approaches that optimize performance while minimizing material usage and manufacturing complexity. Moreover, it can significantly accelerate the design process by automating repetitive tasks and leveraging computational power to explore design alternatives in parallel. This enables engineers to focus their time and expertise on evaluating and refining the most promising design concepts, ultimately leading to faster innovation cycles and more competitive products. Other use cases of Gen AI in automotive include manufacturing, quality control, testing and validation, supply chain management, predictive maintenance, and personalized modeling.
Generative AI empowers automotive engineers to push the boundaries of design creativity and process efficiency in order to develop next-generation vehicles that are lighter, stronger, smarter, and more sustainable.
2. Simulation-Driven Design
Simulation-driven design is reshaping the automotive industry by enabling engineers to leverage engineering simulation, particularly cloud-native simulation technology, for faster and more efficient development processes. This approach accelerates the design process, allowing for quicker iteration and optimization of vehicle and component designs. As such, engineering simulation has evolved from a mere validation step at the end of the design cycle to a crucial element underlying the entire design cycle.
Simulation-driven design, leveraging computer-aided engineering (CAE) and simulation, offers multiple advantages to automotive suppliers. It eliminates the need for extensive physical prototyping and testing, resulting in bottom-line savings on cost and time. It also enables design engineers to explore and innovate various design options in a simulated environment. Furthermore, virtual testing and analysis enhance accuracy and reliability, and iterative design refinement helps optimize performance and efficiency.
By harnessing the power of cloud computing, engineers can conduct complex simulations without the need for costly hardware or extensive IT infrastructure. Furthermore, they can leverage the scalable computing resources available on demand to perform as many simulations as needed in parallel, leading to more efficient development cycles, shorter simulation lead times, and reduced time to market for new vehicles and components.
According to a study conducted by CIMdata, businesses that adopt simulation-driven design methodologies have experienced time-to-market reductions of up to 35% and overall product development cost savings of up to 25%.
A cloud-based simulation platform like SimScale integrates seamlessly with advanced analytics tools, providing engineers with deeper insights into performance metrics and areas for improvement. Collaboration is also enhanced, as engineers from different locations can easily access and collaborate on simulation data, fostering innovation and knowledge sharing across teams. This helps decentralize simulation use while maintaining simulation quality control centrally with simulation experts. Therefore, cloud-native simulation facilitates simulation process and data management (SPDM), elevating the automotive suppliers’ bottom line and accelerating their innovation and adoption of digitalization.
Simulation-driven design represents a significant advancement in automotive engineering. It enables faster, more collaborative, and cost-effective development of next-generation vehicles and components for automotive suppliers.
Whitepaper: Real-Time Automotive Design & Simulation in the Cloud
Learn more about how you can optimize your automotive design process with SimScale and get industry insights for free.
3. Additive Manufacturing (3D Printing)
Additive manufacturing, commonly known as 3D printing, has already been disrupting the automotive industry over the past decade. Unlike traditional manufacturing methods that involve subtracting material from a solid block, additive manufacturing builds objects layer by layer from digital 3D models. This approach offers several advantages, including creating complex geometries, reducing material waste, and producing custom components on demand.
In automotive engineering, 3D printing is used for prototyping, tooling, and end-use part production. Engineers can quickly iterate on designs by 3D printing prototypes and functional parts, enabling rapid validation and refinement of concepts. Additionally, additive manufacturing enables the production of lightweight and optimized components that improve vehicle performance and fuel efficiency.
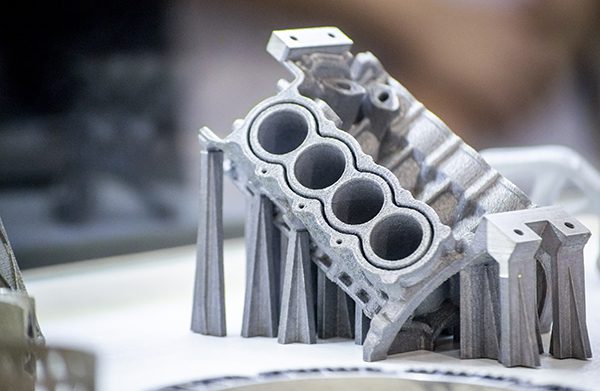
One of the key benefits of additive manufacturing is its versatility. Engineers can choose from a wide range of materials, including plastics, metals, and composites, to suit the specific requirements of automotive applications. This flexibility allows for the creation of parts with tailored properties, such as strength, stiffness, and thermal conductivity, leading to enhanced performance and durability.
Furthermore, additive manufacturing offers significant supply chain advantages. By decentralizing production and reducing reliance on traditional, central manufacturing processes, automotive suppliers can streamline their operations and respond more effectively to changing market demands. Additionally, 3D printing enables on-demand manufacturing, reducing inventory costs and eliminating the need for large-scale warehousing.
As the technology continues to mature, additive manufacturing is expected to play an increasingly important role in developing and manufacturing next-generation vehicles by enabling faster prototyping, lightweight design optimization, and on-demand production.
4. Autonomous Vehicle Development and Simulation
As the “A” in the automotive industry’s ACES trends, autonomous vehicle (AV) technology represents a paradigm shift in the automotive sector, promising to revolutionize the way we commute and transport goods. Engineering techniques related to autonomous vehicle development and simulation are critical for ensuring the safety, reliability, and efficiency of self-driving vehicles. Autonomous vehicle development involves integrating advanced sensors, actuators, and control systems to enable vehicles to perceive their environment, make decisions, and navigate autonomously. Engineers use simulation tools, machine learning (ML), and analysis platforms to model and test autonomous driving algorithms in virtual environments, allowing for rapid iteration and validation of software systems.
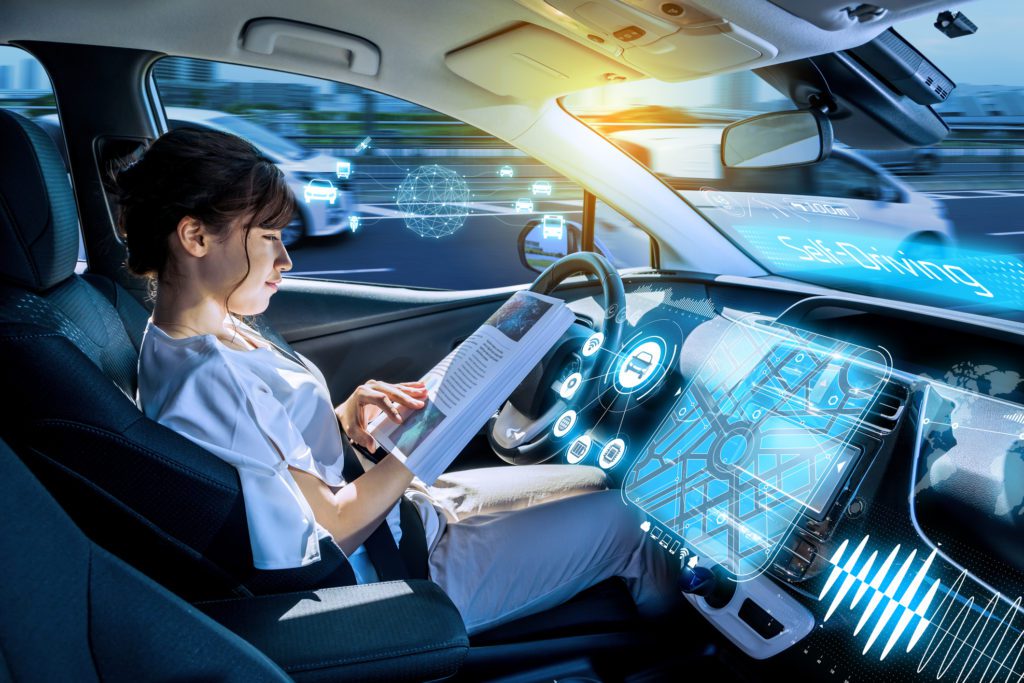
Simulation plays a crucial role in the development of AVs by enabling engineers to conduct extensive testing in diverse scenarios, including various weather conditions, traffic patterns, and road environments. This virtual testing approach allows for identifying and resolving potential safety hazards and performance limitations before deploying autonomous vehicles on public roads.
Moreover, simulation facilitates the optimization of autonomous vehicle algorithms for efficiency and robustness. Engineers can leverage machine learning and optimization techniques to fine-tune control strategies, improve sensor fusion algorithms, and enhance decision-making capabilities, ultimately leading to safer and more reliable autonomous driving systems.
AV technology significantly impacts automotive suppliers across various aspects of their operations, including:
- R&D Collaboration: With the complexity of autonomous vehicle development, automotive suppliers often collaborate closely with automakers and technology companies in research and development efforts. Suppliers contribute their expertise in areas such as sensor technology, software development, and vehicle integration, playing a crucial role in advancing autonomous vehicle technology.
- New Component Demand: As autonomous vehicles require advanced sensors, actuators, control systems, and other components to operate safely and efficiently, automotive suppliers have the opportunity to innovate and provide these specialized parts. This creates a new market for suppliers to develop and supply components tailored to autonomous vehicles.
- Supply Chain Adaptation: Autonomous vehicle technology may require changes in the automotive supply chain to accommodate new components, materials, and production processes. Suppliers must adapt their manufacturing processes, logistics, and quality control measures to meet the unique requirements of autonomous vehicle production.
- Testing and Validation Services: Automotive suppliers may offer specialized testing and validation services to automakers and technology companies developing autonomous vehicles. This includes providing test vehicles, simulation platforms, and test tracks for evaluating autonomous driving algorithms, sensor performance, and overall system reliability.
- Regulatory Compliance: Autonomous vehicle technology is subject to stringent regulatory requirements and safety standards. Automotive suppliers must ensure that their components and systems comply with relevant regulations and standards, which may involve investing in certification processes and compliance testing facilities.
While AV technology requires adaptation and investment in new technologies and processes, it also opens up new markets and collaboration opportunities for automotive suppliers to contribute to the advancement of autonomous driving systems on the path toward realizing the full potential of self-driving vehicles. By leveraging advanced simulation tools and methodologies, automotive engineers can accelerate the development process, improve system performance, and ensure the widespread adoption of autonomous technology in the near future.
5. Digital Twin Technology
Digital twin technology provides automotive engineers with virtual replicas of physical components, systems, vehicles, and production processes. By creating digital twins, engineers can monitor, analyze, and optimize the performance of automotive systems in real time, leading to improved reliability, efficiency, and cost-effectiveness. Digital twins consist of virtual models that replicate the behavior and characteristics of their physical counterparts. These models are connected to sensors and actuators embedded in vehicles or manufacturing equipment, allowing for the collection of real-time data on operating conditions, performance metrics, and environmental factors.
In automotive design, digital twins enable engineers to simulate and validate vehicle performance under different driving scenarios and environmental conditions. By integrating data from onboard sensors and external sources, engineers can optimize vehicle designs for factors such as fuel efficiency, emissions, and passenger comfort, leading to more sustainable and user-centric vehicles.
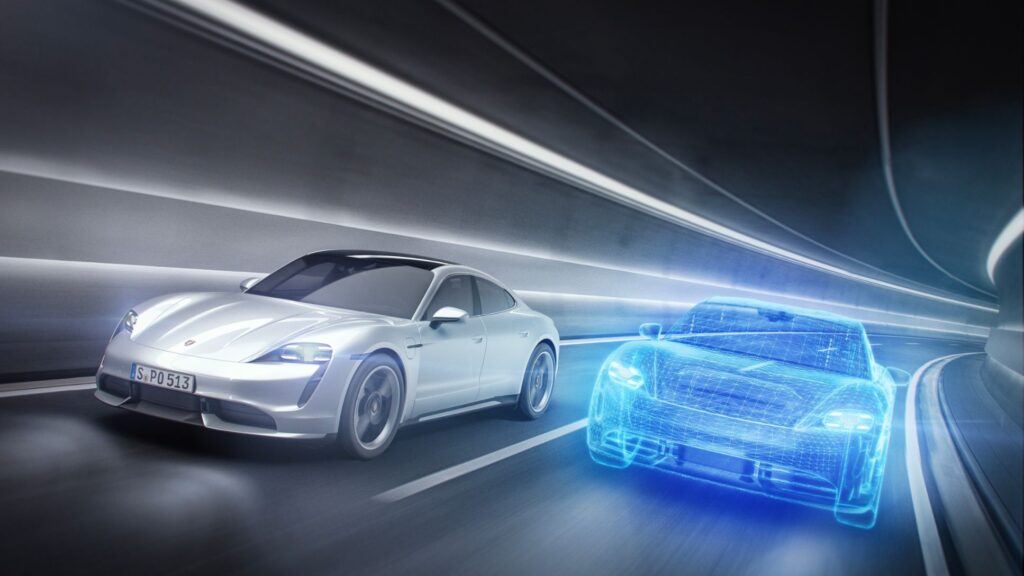
Digital twins also facilitate predictive maintenance and process optimization in manufacturing by monitoring equipment health and performance in real time. By analyzing sensor data and historical maintenance records, engineers can anticipate potential failures, schedule maintenance activities proactively, and minimize downtime, thereby improving overall productivity and efficiency. Furthermore, digital twins enable automotive suppliers to optimize their supply chain operations by providing real-time visibility into inventory levels, production schedules, and logistics activities. By leveraging data analytics and machine learning algorithms, suppliers can forecast demand, optimize inventory management, and identify opportunities for cost savings and process improvements.
Automotive suppliers can also develop collaborative partnerships with other suppliers and OEMs by capitalizing on the digital twin technology. By sharing digital twins of components, systems, and production processes, they can collaborate more effectively to optimize product performance, streamline manufacturing processes, and enhance overall competitiveness in the automotive industry.
The digital twin technology offers automotive engineers and suppliers a powerful tool for improving product performance, production efficiency, and supply chain management. By creating virtual replicas of physical assets and leveraging real-time data, engineers can optimize vehicle designs, manufacturing processes, and supply chain operations, driving innovation and competitiveness in the automotive industry.
Next-Gen Technologies: Honorary Mentions
Now that we have covered five of the most impactful next-generation technologies in the automotive industry, particularly for automotive suppliers, let’s have a look at some other emerging technologies that are equally important. Suppliers can employ some of these technologies simultaneously to ensure more efficient engineering and faster innovation.
Edge Computing for Real-Time Data Processing
Edge computing technology enables automotive systems to process data closer to the source, reducing latency and bandwidth requirements. By deploying edge computing solutions in vehicles and manufacturing facilities, engineers can achieve real-time analytics, predictive maintenance, and autonomous decision-making, enhancing operational efficiency and performance.
Robotics and Automation in Manufacturing
Robotics and automation are crucial in modern automotive manufacturing, enabling precision assembly, flexible production, and human-robot collaboration (HRC). Automotive manufacturers can improve productivity, quality, and worker safety on the production line by deploying robotic systems for tasks such as welding, painting, and assembly.
Computer Vision for Advanced Manufacturing and Quality Control
Computer vision technology is revolutionizing automotive manufacturing processes by enabling machines to interpret and understand visual information. Using cameras, sensors, and machine learning algorithms, computer vision systems can analyze images and video streams in real time. This allows for automated inspection, quality control, and defect detection on the production line. By harnessing computer vision, automotive manufacturers can achieve higher levels of precision, consistency, and efficiency in manufacturing processes, ultimately improving product quality and reducing costs.
Augmented Reality (AR) and Virtual Reality (VR) for Design and Training
AR and VR technologies can be utilized in automotive design and manufacturing processes for immersive design reviews, virtual prototyping, and training simulations. These technologies enhance collaboration, visualization, and training experiences, leading to improved design quality and workforce productivity.
Advanced Materials and Nanotechnology
The development of advanced materials, such as carbon fiber composites, lightweight alloys, and nanomaterials, enables automotive engineers to design lighter, stronger, and more fuel-efficient vehicles. These materials offer superior mechanical properties, thermal conductivity, and corrosion resistance, driving innovation in vehicle design and performance.
Final Thoughts
The automotive industry is undergoing a transformative period driven by next-generation engineering techniques impacting both OEMs and automotive suppliers. From cloud-native simulation and generative AI to additive manufacturing, autonomous vehicle development, and digital twin technology, these techniques are reshaping the way vehicles are designed, manufactured, and supplied.
By embracing these innovative approaches, automotive engineers and suppliers can unlock new opportunities for efficiency, performance, and sustainability, ultimately delivering better products and experiences to customers. As these technologies continue to evolve, it is essential for industry professionals to stay up-to-date with the latest developments and leverage them to drive continued progress and innovation in the automotive sector.