Engineering simulation tools have undergone significant transformations over recent decades. From the early days of locally installed, dedicated expert simulation tools to the integration of these tools within CAD systems, and now to the latest generation where online simulation platforms serve as the backbone of engineering operations, the evolution is marked by increased accessibility, efficiency, and strategic value.
This development has occurred alongside advancements in the computer industry and the refinement of engineering processes. Traditionally associated with the manufacturing sector, simulation has played a critical role in enhancing production efficiency and capacity. In its early days, simulation was largely inaccessible due to its time-consuming nature, ambiguous models, and the need for highly specialized experts, making it prohibitively expensive.
The landscape began to change in the 1970s with the adoption of computing algorithms, modern programming languages, and improved visualization tools. These advancements made simulation models more reliable, easier to create, and clearer to interpret. Enhanced computational power over the following years and decades allowed for more complex simulations, while better graphics provided intuitive insights, making simulation an integral part of various industries.
Today, simulation technology continues to advance, integrating with emerging technologies like AI and machine learning to further optimize engineering processes and drive innovation. As we delve into the generational shifts in engineering simulation, it becomes evident that simulation has expanded in accessibility, cost-effectiveness, scalability, and innovation enablement.
Generation 1: Dedicated Expert Simulation Tools
The first generation of advanced engineering simulation tools emerged in the latter half of the 20th century. These tools were sophisticated, highly specialized, and designed for expert use. They provided detailed and accurate simulations, enabling engineers to predict the behavior of complex systems under various conditions. However, these tools were not without their limitations:
- Expert-Driven: The tools required high expertise to operate, limiting their use to specialized engineers. This exclusivity created a bottleneck, as only a small group within the company could utilize these powerful tools effectively. It also led to a knowledge gap between simulation experts and other engineering team members, potentially hindering collaboration and innovation.
- High Cost: The software was expensive, often requiring substantial investment in both the software itself and the hardware needed to run it. Companies had to allocate significant portions of their budgets to acquire and maintain these tools, including the initial purchase price and ongoing costs for updates, training, and support. This financial barrier meant that only larger companies with significant resources could afford to implement these tools effectively.
- Isolated Operation: These tools operated independently of other engineering processes, leading to inefficiencies and potential miscommunications. The lack of integration with other design and analysis tools meant that data had to be manually transferred between systems and teams, increasing the risk of errors and data loss. This siloed approach also made it difficult to create a cohesive workflow, as simulation results were not easily accessible to other team members or departments.
Despite these challenges, dedicated expert simulation tools laid the foundation for modern simulation capabilities, providing invaluable insights and driving technological advancements across various industries. Yet, the need for more accessible, cost-effective, and integrated solutions became increasingly apparent as engineering demands grew in the years to follow.
Generation 2: CAD-Integrated Simulation Tools
The second generation of simulation tools came around the turn of the millennium. It brought about a significant shift with the integration of Computer-Aided Engineering (CAE) simulation capabilities with Computer-Aided Design (CAD) systems. This integration addressed many of the challenges faced by the first generation and introduced several key benefits.
With CAD-integrated simulation tools, engineers could perform simulations of real phenomena directly within their design environment, leading to an improvement in workflow efficiency and iteration cycle time. From structural integrity to fluid dynamics, thermal properties, and other real-world behavior, engineers became better equipped with integrated simulation capabilities to refine their designs.
Such an integration meant design changes could be tested and validated more quickly. This helped speed up the product development process and reduce the need for physical prototyping, which in turn led to savings in time, costs, and resources. In addition, graphic technology developments enhanced the reliability and accuracy of data visualizations in depicting real-world scenarios. This provided a more effective way for design engineers to demonstrate their ideas.

However, these integrated tools were still locally hosted, which required local, private computing farms. Their performance was still tied to local hardware capabilities, which was a bottleneck for complex simulations. Engineers often faced challenges related to limited computing power, restricting the size and complexity of the models they could simulate. Companies still needed to invest heavily in expensive hardware to ensure sufficient computing power.
In some cases, CAD-integrated simulation tools often lacked the depth and specialization of dedicated simulation tools, which meant that for highly complex or specialized simulations, companies still needed to rely on first-generation tools. While integration improved workflows, it also introduced new complexities. Ensuring compatibility between CAD and simulation components could be challenging, mainly when dealing with updates and new releases. Companies had to invest in training and support to help engineers navigate these integrated environments effectively.
Expertise, accessibility, and computing power remained the fundamental challenges of CAD-integrated simulation tools. As these challenges persisted, the need for a more flexible, scalable, and collaborative approach to engineering simulation became clear, paving the way for the third generation of simulation tools.
Generation 3: Simulation as a Company Backbone
Since the 2010s, we have witnessed a paradigm change in the technology underlying engineering simulation and the role of simulation within engineering companies. As cloud computing became increasingly prevalent, cloud-based and cloud-native CAE technologies emerged, enabling a shift from local, siloed workflows to more collaborative and efficient workflows.
No longer confined to usage by simulation experts or limited by local hardware constraints, simulation has become an integral part of the entire engineering design process, supporting both engineering and business goals. This generation of cloud-native simulation tools has transformed simulation from an isolated task into a strategic enabler of innovation, efficiency, and competitiveness.
Such a holistic approach takes simulation beyond its mere validation stage at the end of a design cycle to an underlying factor spanning the whole design process. It introduces simulation early in the design process as a way for engineers to analyze and optimize their design iterations efficiently. In other words, it ensures that insights gained from simulations early on can drive more informed decisions, accelerate innovation, and ultimately lead to better products and business outcomes. This is referred to as simulation-driven design and engineering.
The cloud-native approach of such simulation tools breaks down traditional barriers of the previous generations, allowing for real-time collaboration across geographically dispersed teams, scalability to handle complex simulations, and integration with other enterprise systems to create a seamless engineering ecosystem. By deploying simulation across the whole enterprise, companies are leveraging cloud-native simulation tools not only for product development but also for strategic decision-making, market differentiation, and continuous improvement of processes and products. This also gives companies access to talent pools worldwide and shortens the product development cycle.

While simulation is democratized, allowing more team members to participate in the simulation process, simulation experts remain in charge of simulation quality control. With cloud-native simulation tools, the backlog for simulation experts is reduced, and the resulting simulation lead time is minimized. In other words, design engineers could now create, parametrize, validate, and optimize their designs early and often, reducing their waiting time and over-reliance on specialized simulation experts.
Meanwhile, simulation experts ensure the selected design(s) are fit for production based on their simulation expertise. All this collaborative work takes place on a single, cloud-native platform accessible by all stakeholders anytime and anywhere, enabling effective simulation process and data management (SPDM). SimScale offers such a platform.
SimScale: Leading the Third Generation of Simulation
As a cloud-native simulation platform, SimScale is at the forefront of the third generation of engineering simulation tools. Over the past decade, SimScale has become a leading player in the engineering simulation market, paving the way for companies across various industries to deploy enterprise-wide simulation and leverage it as a backbone for their businesses, especially in accelerating innovation and increasing efficiency.
With its accessibility, scalability, and multiphysics simulation capabilities integrated into a single platform, SimScale enables process integration and data optimization (PIDO) and ensures it is scalable across the whole enterprise. Here’s how SimScale distinguishes itself in the market and sets new standards for the industry:
- Cloud-Native Accessibility: By leveraging cloud computing, SimScale makes high-performance simulation accessible to any engineer with an internet connection. This eliminates the need for expensive local hardware, removes the limitations of on-premise software, and democratizes access to advanced simulation capabilities.
- Enterprise-Wide Deployment: SimScale’s platform can be deployed across an entire enterprise, breaking down silos and enabling seamless collaboration among engineering teams. This ensures that simulation is not just an isolated activity but a core component of the company’s engineering strategy.
- Scalability and Flexibility: The cloud-native nature of SimScale allows for unparalleled scalability. Companies can run multiple simulations in parallel, scale up resources on demand, and handle complex simulation tasks without worrying about hardware limitations.
- Integration and Collaboration: SimScale integrates easily with other engineering tools and platforms, providing a cohesive and collaborative environment. This integration ensures simulation data can inform design decisions throughout the product development lifecycle, enhancing overall efficiency and innovation.
- Business and Engineering Alignment: SimScale’s platform supports engineering and business goals by providing insights that can drive product optimization, cost reduction, and time-to-market improvements. The ability to run extensive simulations early in the design process helps identify potential issues, reducing costly late-stage changes.

What the Future of Engineering Simulation Holds
As we move forward, the third generation of engineering simulation tools, epitomized by platforms like SimScale, will continue to evolve. The emphasis will be on further enhancing accessibility, improving integration with other enterprise systems, and leveraging advancements in cloud computing to deliver even more powerful and insightful simulations. But that’s not all.
With the advent of artificial intelligence (AI) and its convergence with simulation, a new generation of simulation could be knocking on the door: the generation of AI Simulation. By incorporating AI-driven insights and functionalities, AI simulation’s core strength is its capacity to speed up and improve the simulation process, making it more efficient, intuitive, and accessible for engineers and designers throughout the design cycle.
Cloud-native simulation provides the most robust and compatible infrastructure for AI Simulation to run effectively. This is why SimScale is leading the industry in integrating AI into simulation, with the aim of building the next generation of simulation and paving the way for future innovations in simulation-driven design.
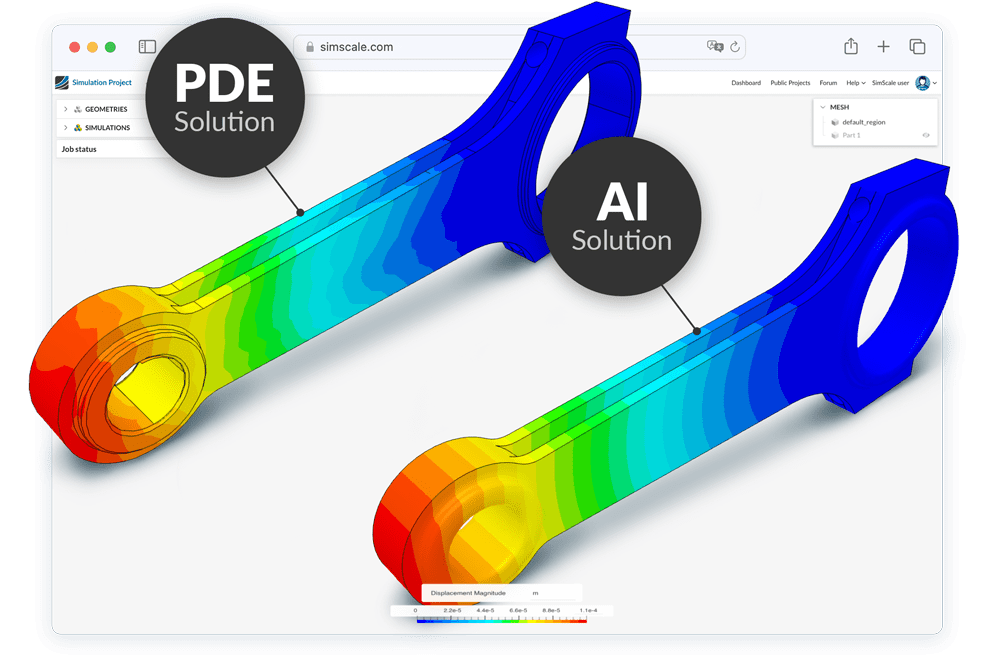
The journey from the early days of simulation through the three generations of modern simulation tools reflects the dynamic nature of engineering simulation. Each generation has built upon the strengths and addressed the weaknesses of its predecessors, leading to tools that are more powerful, accessible, and integral to engineering success.
SimScale’s leading role highlights its commitment to transforming engineering simulation into a strategic advantage for companies. By providing a robust, cloud-native platform, SimScale ensures that simulation is an integral part of the engineering and business landscape, driving innovation and efficiency in unparalleled ways.
References
- Teschemacher, T., Bauer, A.M., Oberbichler, T. et al. Realization of CAD-integrated shell simulation based on isogeometric B-Rep analysis. Adv. Model. and Simul. in Eng. Sci. 5, 19 (2018). https://doi.org/10.1186/s40323-018-0109-4