Most computer-aided engineering (CAE) software solutions on the market are the traditional, on-premises ones. In recent years, however, many companies have moved or are preparing to move to cloud-based simulation tools, stepping into the new digital world and workplace.
Despite the wide range of simulation features and highly developed technology, on-premises CAE software is accompanied by several barriers that have prevented the technology’s widespread adoption for the past decades. These barriers are related to poor accessibility, steep costs due to hardware investment and software licenses, high expertise required to use the tool itself, and—a more recent need—lack of collaboration options.
Cloud solutions and cloud-based simulation providers are leading the democratization of CAE, bringing to market solutions that run in a web browser from any PC or laptop, have a relatively easy-to-use interface, and allow users to work together on the same project, in real-time.

In short, these are the main benefits of simulation in the cloud:
- Access the simulation tool and your CFD or FEA projects from anywhere, anytime
- Cut down hardware requirements and investment, a standard laptop/PC will suffice
- Share simulation projects and collaborate with colleagues
- Use the CAE platform for live discussions instead of creating slides and presenting to clients, managers or colleagues
- Run complex simulations with parallel computing
- Live support (chat function), with a response time often under 5 minutes during business hours (well, that’s our achievement at SimScale, we cannot tell for other providers)
- Work from home (or Bali) anytime
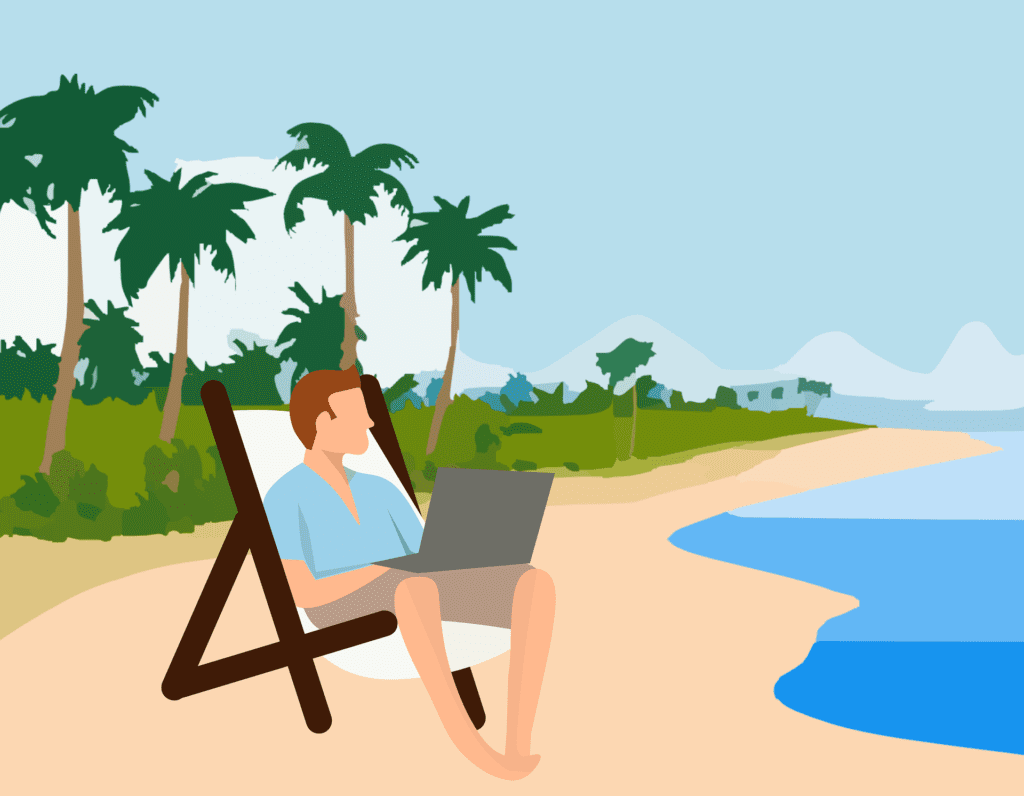
If you have already decided to migrate to the SimScale cloud solution for CAE, the following steps and information might be of use in helping you have a seamless migration.
This paper addresses the difference between on-premises software and SaaS
solutions for computer-aided engineering, explaining how SaaS came to be and its
key benefits.
Tips for Migrating From On-Premises CAE Software to a Cloud Solution
1. Purchase the plan that suits you best (yearly subscription, pricing is based on your needs).
2. Create an account online, no installation, just a standard sign-up like all modern software.
3. Get onboarded with the learning materials that the SimScale team sends you, and with tutorials and user guides you can discover autonomously.
4. Copy a simulation project (from the public library) and use it as a template to familiarize yourself with the platform. Public projects are free, they do not use up the core hours from your paid plan. Pay attention to the type of projects you create (private or public) depending on the purpose (learning/playing around versus work projects; for the latter, you should always create private projects to protect your geometry and results).
5. Name your files and simulations. This is very important when importing and creating data in the cloud; you will rapidly end up with 20 different designs in 20 different simulation setups which themselves have multiple runs.
6. Plan your time wisely. With cloud-based tools, you are not restricted by computational power; it is not uncommon to run meshes of 10M to 20M cells for a few hours and obtain converged, and accurate results. Our users and team members usually start the runs before going to bed and close the laptop. They then post-process the results in the morning.
7. On most standard CAD packages, when you create configurations (sometimes called families of parts for one design), you can batch export all the configurations in either the native format or a neutral file format (STEP, IGES, Parasolid, etc.).
8. Run as many simulations in parallel as you need to compare different designs under the same conditions.

9. Run as many simulations in parallel as you need to compare the performance of one design under different conditions.
10. There are no restrictions in terms of data storage or a number of simulations within a single cloud-based simulation project. You can duplicate a simulation setup and reutilize it as many times as you need for other designs, like a template.
11. Similarly, you can run as many meshing jobs as you need, this turns out to be very useful when performing a mesh independence study.
12. No need to schedule maintenance for software updates. No need to schedule regular hardware upgrades. Everything is taken care of in the background, by the cloud-based simulation software provider. This means users see the latest version of the platform at all times.
13. Within the platform, you have an option to instantly connect with one of our support engineers, they can even edit your project directly if you allow them to.
These were some of the steps and tips that we think are useful to know. The endeavor of migrating to a new solution, especially one that is deployed differently, certainly raises more questions. So here are the answers to some that you might have.
How Will I Access Old Data After the Migration?
Moving to a cloud solution means you don’t need to store simulation data (3D models, specification files, result files, etc.) locally. This being said, you might still need to access your old simulation data, when comparing runs and retrieving old simulations of designs. Organizing these archives is an essential part of the migration process, as the data should be easily accessible, readable, and comparable with online results. Think of your old files like an outdated Rolodex. Now you just need to digitize it, and away you go, to the cloud!
How Will I Know Results Are Consistent with the Old Software?
You’ll need testing time. Comparisons between the traditional, on-premises CAE solution and the cloud-based platform should be taking place for additional validation and to ensure your results are converging. Some tests and potential adjustments need to be performed so that the transition is as smooth as possible for the end user.
How to Train on the New Software?
The end user should be fully familiar with the new interface, workflow, and settings of the cloud-based tool. This means that some time should be allocated for training sessions with specific and relevant material to cover your particular industry. This way, your engineering team can be up and running as soon as possible, while already knowing how to get from A (CAD upload) to B (interpreting data/results), and shortening time to delivery on even the first project. Also, you should leverage the support services that SimScale offers.
Will I Need My Old Machines with Simulation in the Cloud?
Migrating a workflow to a cloud solution comes with the benefit that dedicated high-performance hardware is no longer required. You can feel the weight of heavy equipment being lifted off your shoulders, and more literally, off your desk. Of course, it depends if other software solutions, for CAD, rendering or CAE are used, as these will still require onsite computational resources.
No longer can engineering teams be bound by project silos, time zones, or physical locations to meet demanding deadlines. So how can engineers use this to their advantage?
Will the New Workflow Help or Hinder the Design Process?
Evaluate your new workflow by analyzing every step of the process; how are the original 3D CAD models created? Are multiple configurations of a design exported from a standard CAD package? How are they stored before being uploaded to the cloud? Will the current naming convention used for the online projects work? It can also be important to establish some project templates if the workflow, product to be simulated or type of analyses are often reused.
Conclusion
For this article, we asked our application engineers to share their input and advice for a seamless migration. Along with useful tips, some also shared their experience. If you remain undecided about migrating to the cloud, here is what a fellow engineer had to say after one year and a half working with a cloud-based simulation tool.
“These were my biggest problems when I was using simulation at home. Firstly, my laptop is a workstation but still has limited hardware. I had to deal with software and hardware issues (cooling, software crash, overall maintenance). Secondly, my laptop’s hardware was limiting me to use large meshes. In industrial applications, we need a good and detailed mesh. You cannot even start a simulation because the laptop does not generate the required mesh density. Third, when I did manage to create a mesh, the simulation was very slow. It takes days to converge simple cases. And lastly, if I was unsure whether my simulation strategy or settings are right, there was no one to ask for assistance. With cloud-based simulation, one can free their PC for local processing and move towards truly scalable simulation.”
– Mehmet Özcan, CFD Application Engineer at SimScale
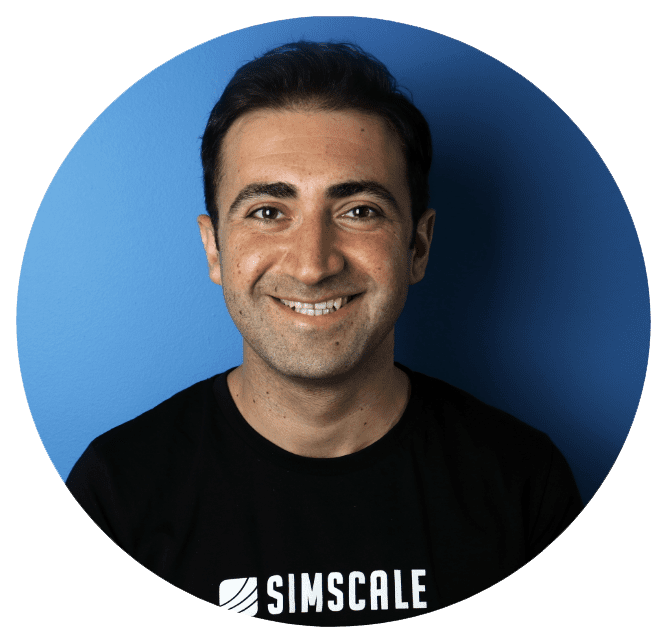
If you have already decided to make the move to the cloud, welcome! We hope these tips will help to ease any transition woes. Rest assured, the SimScale support team is available nearly around the clock, in two separate time zones, if you do in fact need support. Yet don’t just take our word for it, online reviews from our customers always mention how helpful our application engineers are, along with nearly every case study we have on our customers’ page. We have to admit, we’re all quite proud of them.
This is it! Let the migration to the cloud begin. It might not be very easy to move to a new solution, but once done, cloud-based simulation will provide an entire new universe to explore. We’ll be with you for the ride!