In today’s increasingly competitive landscape, it seems as though there are even more pitfalls to potentially fall into, in an engineer’s design process. Ultimately, these hurdles can cause teams to miss their deadlines, and come up short in the final stage. Maybe you’re familiar with these outcomes; a project isn’t delivered on time, within budget, or is delivered, but missing key features that were otherwise agreed upon. Furthermore, a failure such as this in the engineering design phase of a project means that subsequent procurement, construction or production phases will suffer and be delayed.
These inadmissible outcomes are generally the result of either poor project management or issues slowing your design process down. In this article, we will focus on the latter problem area, highlighting three common pitfalls in the design process that can easily be avoided.
Design Process Pitfall One: Documentation Dilemas
Across all industries, design processes are usually followed up with some version of supplementing documentation. This documentation can be either for the end-user, directors, managers or even internal members within your engineering team. Writing with intent to publish is an innately tedious task, and can be a very time-consuming aspect within a design workflow that stifles your time to delivery.
In practice, documentation isn’t always a favorite task, and finding a volunteer to take ownership of such an undertaking… needs it’s own blog to fully berate. On paper, it can seem onerous, time-intensive, and distracting from the overall goal or mission currently at stake. An interesting perspective we will examine on this subject comes to us from Derek Parham, former Deputy CTO for Hillary Clinton’s presidential campaign, and before that, the Technical Lead for the G Suite from Google. On the subject of documentation, he explains:
“People will send out a design doc in an email thread and ask everyone for feedback, then you get this game theory problem where everyone thinks that someone else is going to read it and give feedback, so no one does. Engineers then take this silence as acceptance or apathy and build the feature or system without any feedback. Months later, issues come up that could have been prevented if people actually read the doc and talked about it. So it’s very important to make sure you have a process that actually gets people to read the document.”

Instead of dealing with issues like this, he suggests allowing junior engineers or interns to write the first draft of documentation, then assigning senior engineers as editors. At SimScale, we follow this procedure, as well as having quite a lengthy review process for our documentation, always with opportunity for improvement; as it needs to be constantly updated and added to.
Depending on the size of your company, you may not have enough team members to account for multiple editors/reviewers/writers. If this is the case, you should also explore the opportunity of expanding this function to other departments such as Marketing or HR. All and all, the advice to take away to avoid this pitfall, to avoid having this task left unchecked on your ‘To-Do’ list before it’s too late, is to set up a streamlined documentation process that works for your business.
Design Process Pitfall Two: Why Wait When You Can Automate?
In an engineering team’s design process, there are definitely boring tasks that must be done in order to complete the project. Compiling, unit testing, distribution, Q&A… there are probably some designers/readers yawning as they read this. However, they are essential, and have the propensity to be automated.
At this point, these examples speak more to designers, and less to engineers, but the point that remains can be extended for all disciplines. Autonomous and continuous integration is like an automatic assembly line. You can set it up once, and forget it; it works like clockwork. When you do it correctly, every line of code written is one click away from deployment and reaching customers. Assembly, testing, distribution, and numerous other tasks such as this can be done automatically, giving you more time to focus on the next task at hand.
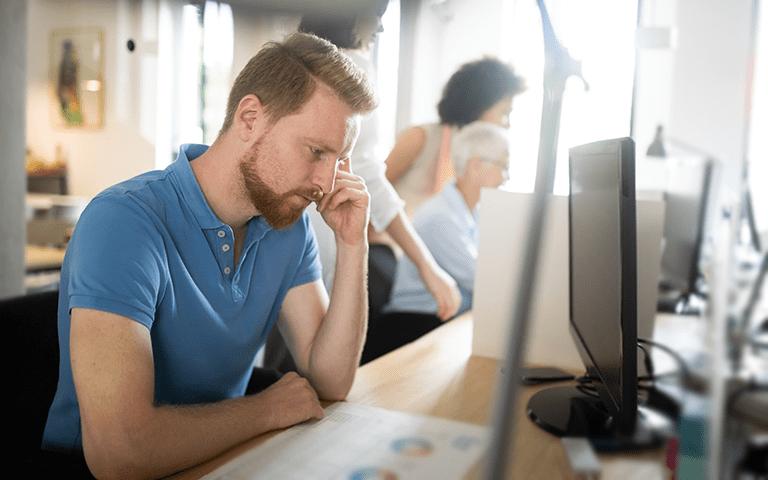
So, why should this process be different for engineers? There should be parts of an engineering team’s workflow that should also be automated, starting with their evaluation and simulation software. Gone are the days of manually installing on-premise simulation software that engineers need to manually update, there are now cloud-based solutions, like SimScale, that roll out updates and new features automatically through the power of the cloud.
With cloud-based software, engineers can easily upload or import CAD models of their designs, run simulations in parallel through their web browser, and then even shut down their computer while the analyses run. This way, teams are able to finish other parts of the design process in the meantime, positively impacting their time to delivery.
Design Process Pitfall Three: Reinventing the Wheel
Lastly, engineering teams should avoid reinventing the wheel in their design process. Using what has worked well previously in other designs should be reused in new designs. By incorporating components, parts or methodologies that have been tried and tested in previous designs and eventually products, engineering teams cut out the time that would have gone into engineering brand new parts.
For example, if you’re designing a new electronics cooling system for an LED spotlight, but you have produced something similar in the past, use this CAD model and simulation project moving forward in your new design. Simply change the configurations until you can meet the new requirements and parameters.

Not only does reusing past work reduces product costs, it makes procurement easier to manage, and streamlines aftermarket services, it most importantly (for your engineering team) results in faster product development and improves time to delivery.
Using SimScale, engineering teams, no matter where in the world they are located, can reuse previous projects of other team members quite easily with our new Team plan. Features include project sharing & collaboration, a shared team dashboard, and a dedicated technical account manager to help facilitate this tip to avoid design process pitfalls.
No longer can engineering teams be bound by project silos, time zones, or physical locations to meet demanding deadlines. So how can engineers use this to their advantage?
Conclusion
Within your engineering team, there is always an opportunity to improve your time to market in more ways than one, and even more, pitfalls to avoid than the ones listed above. According to Derek Parham, size can also be a major factor in engineering excellence—and any team over 15 is headed in the wrong direction, and possible towards, you guessed it, a pitfall. All and all, in order to mitigate design process problems, figure out a way to smoothly turnaround documentation, how to automate any part of the process, reuse as much as you can, make sure to collaborate and keep everything accessible, and you’re off to a good start. For more advice on how to speed up your design process, check out this recent article giving five insightful improvement tips.