Dynamis PRC is the Formula Student Team of Politecnico di Milano, and has been competing in FSAE events since 2004. FSAE, or Formula SAE, is a student design contest founded and organized by SAE International, the Society of Automotive Engineers). Started in 1980 by the SAE student branch at the University of Texas in Austin, now 40 years later, it is comprised of many different events and competitions held for university teams around the world.
These FSAE engineering competitions allow students to design, test, develop, and produce a single-seater prototype to race against other university teams. The teams are then matched up in groups of different disciplines ranging from acceleration, endurance, performance, and design to cost evaluation of the project.
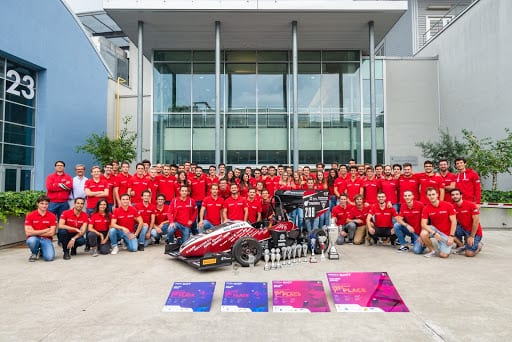
The Challenge: Evaluating for Electric Mobility
In recent years, the team has obtained several wins all over Europe at different events, and has continued to develop their prototypes to ultimately improve their performance year over year. For the upcoming season, the project has shifted its focus towards electric mobility, giving them the chance to start from scratch, and design a prototype like never before. This includes a new monocoque, as well as assessing new aerodynamic properties for the first fully electric prototype of Dynamis PRC, the DP12.
How Dynamis PRC Solved It With SimScale
The basis of the design process is performed through CAE systems. After the 3D model is developed, a simplified version for computational fluid dynamics or CFD simulations is then created. The next step is the actual simulation using SimScale, followed by the post-processing of the results, and finally, some modifications being made to the design based upon the findings. Once the process has been completed, the cycle starts again from the beginning until the team is satisfied with the results of their design’s aerodynamic properties.
“The extensive use of SimScale ensures a flawless workflow for the daily development of the aero package and, more importantly, for Aero Maps. Throughout the whole year, several full car RANS simulations have been performed to develop the basic concepts and to decide on the wing shapes.” – Luca Galimberti, Head of the Aerodynamics Department
In order to extract the maximum potential from the car in each situation, multiple simulations with different ride heights are made to compute aerodynamic loads in each part of the race lap. These studies help to evaluate the overall behavior of the car in a variety of conditions on the racetrack, and with different setups; so that the team is prepared for whatever is around the corner. If implemented with dynamic models, this data can give a holistic view of the vehicle’s performance, and therefore improve the electric vehicle’s lap time.
A Look Under the Hood: Evaluating Ride Heights
For Dynamic PRC, the most extensive analysis has been conducted for the ride height of the car, both for the front and rear axle. By imposing a certain translation from the normal value, which is 30 mm of ground clearance, it’s possible to have a positive or a negative rake angle. The dependence of this angle is very important for this context. In particular, the next table resumes the different ride heights and corresponding rake angles tried.
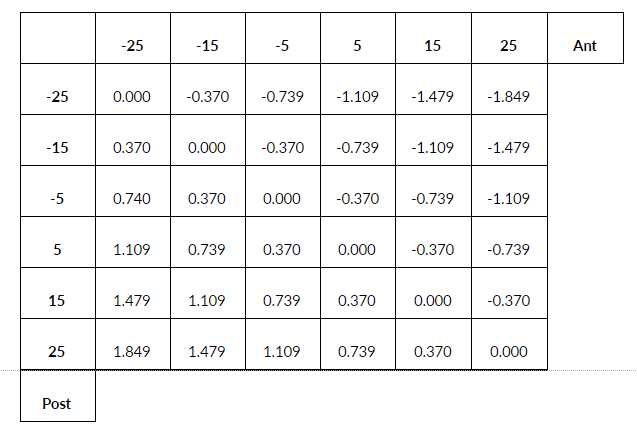
The goal of this evaluation is to keep a stable value of downforce in different conditions (rolling, braking, acceleration, crosswind, and with the wheels steered) to optimize the overall performance.
At first, the prototype was simulated in various height configurations in a straight line stationary condition at 16 m/s. These simulations were the simplest, yet require a lot of man-hours as there are multiple combinations. For this reason, the use of SimScale proved to be beneficial to the team as it provides a lot of computational power, allowed the team to run simulations in parallel, and in a quick and user-friendly manner.
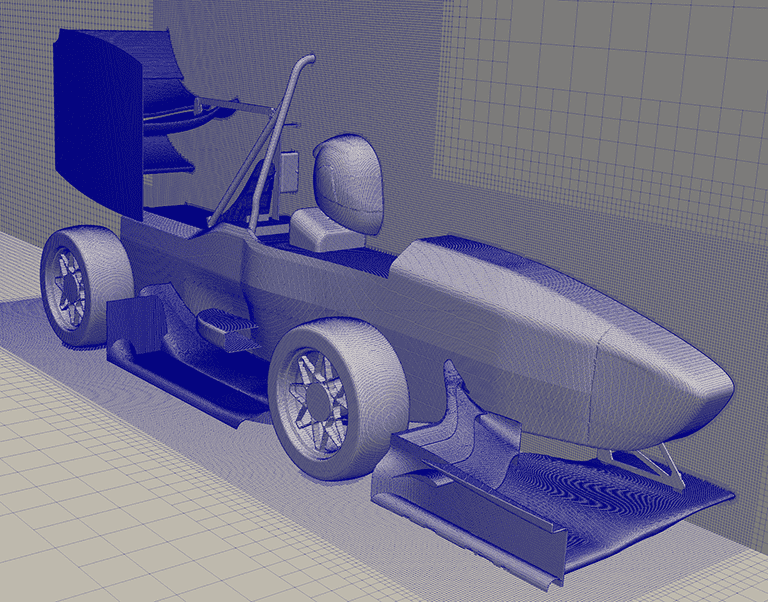
After some convergence studies, a mesh with around 20 – 25 million cells was created on the platform and then used for further investigations. The level of refinement of the cells within the vicinity of the car was very high.
It was possible to obtain between 5 and 6 boundary layer cells (depending on the area of the car), with an extrusion percentage always higher than 87%. Furthermore, averaged y + values of around 30 were obtained. To reduce the computational costs, half of the straight-line car simulations were run with a symmetry plane splitting the car.
Dynamis PRC: Car Simulation Results
The results of the simulations were targeted towards the maximum possible downforce. This is because of this type of competition, in which not very high speeds are reached. In the pictures, it’s possible to visualize the pressure distribution in the form of a pressure coefficient on the surface of the car.

The plot of all the aerodynamic data at the different ride heights (the Aero map), allows one to easily comprehend the dynamic behavior of the vehicle. In this particular case, we can evaluate the lift coefficient, in order to see the downforce contribution in each rake configuration. Such a result is obtained through a linear interpolation of the data computed with various simulations.
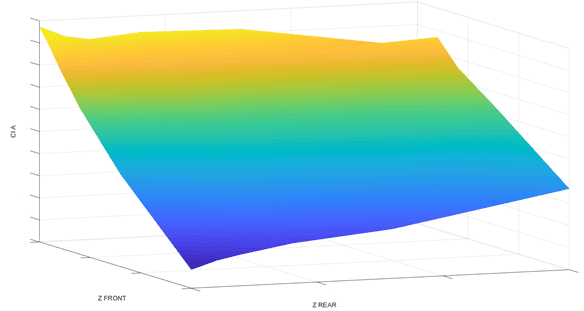
At the same time, the results were dynamically analyzed with a complete model of the car including suspensions, mass distribution, and several parameters that contribute to the overall performance of the vehicle.
Overall, the team successfully performed with SimScale more than 125 simulations with around 20000 CPU hours used. Moreover, the work with the software has helped to improve the downforce from the previous car by about 12.5% and in general, has given a better understanding of the car prototype’s aerodynamics.
As the season has come to an early ending, the team is now looking forward to starting again where it stopped and will surely work hard with SimScale in its virtual pit crew, to bring the best possible vehicle for 2021.